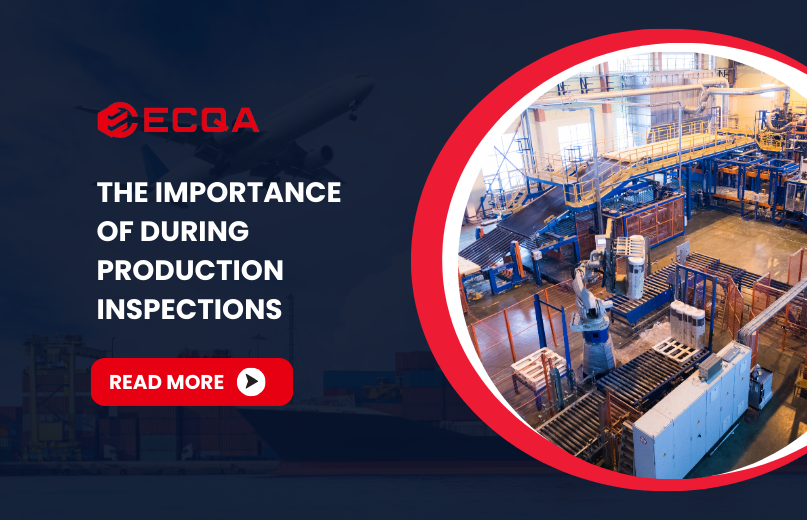
The Importance of During Production Inspections
Effective quality management is essential for businesses engaged in manufacturing, as it directly impacts product consistency, customer satisfaction, and market reputation. During production inspections, also known as DUPRO inspections, play a crucial role in ensuring that production processes remain on track and meet the required standards. Conducting inspections during the production phase helps manufacturers identify defects early, mitigate risks, and maintain product quality throughout the entire manufacturing cycle. Below, we delve into the significance of these inspections, their benefits, and how they can optimize manufacturing operations.
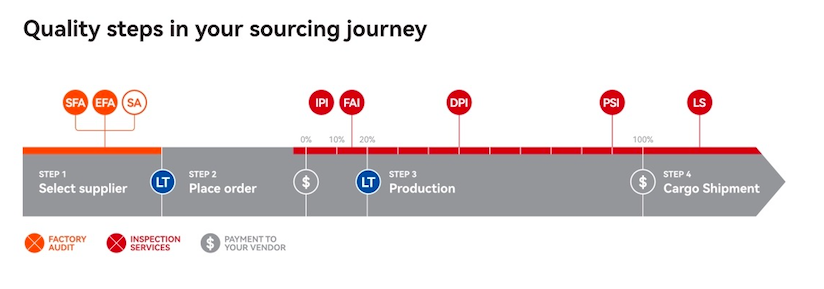
During Production Inspections
During production inspections refer to quality control checks performed at different stages of the production process, typically when approximately 20-80% of the goods have been completed. Unlike pre-shipment inspections, which only occur after production is finished, DUPRO inspections offer a real-time assessment of product quality. This inspection method enables manufacturers to identify any non-conformities early on, allowing for prompt corrective actions to prevent further issues.
Benefits of Conducting During Production Inspections
Early Detection of Defects
One of the primary benefits of during production inspections is the early identification of potential defects. By inspecting products while they are still being manufactured, quality control teams can detect problems before they become widespread. This early detection allows manufacturers to address issues immediately, preventing defective products from reaching the market. As a result, it minimizes the likelihood of costly recalls, returns, or customer complaints.
Improved Quality Control
Incorporating during production inspections into the quality management system helps maintain consistent standards throughout the manufacturing process. By regularly monitoring production quality, companies can ensure that each batch meets the specified requirements. Any deviations can be addressed on the spot, reducing the risk of producing large quantities of defective items. This proactive approach enhances overall quality assurance and promotes continuous improvement.
Reduced Production Costs
When defects are caught early during the manufacturing process, the cost associated with rework, scrap, or production delays can be significantly reduced. During production inspections help identify quality issues before additional materials and labor are invested in completing defective products. This efficiency not only saves money but also improves productivity, allowing manufacturers to focus resources on creating high-quality products.
Enhanced Supplier and Factory Communication
Engaging in during production inspections fosters better communication between suppliers, factories, and quality control teams. The inspection process often involves reviewing and discussing specifications, tolerances, and production methods. These interactions can lead to stronger partnerships, clearer expectations, and more effective collaboration in resolving quality-related concerns. A well-informed production team is more likely to deliver products that meet or exceed customer expectations.
Increased Customer Satisfaction
Maintaining high standards during the manufacturing process translates directly to better products for customers. During production inspections help ensure that products meet the desired quality before they leave the factory, reducing the risk of delivering subpar goods to consumers. This proactive quality management approach improves customer satisfaction and fosters brand loyalty, which can lead to repeat business and positive referrals.
Key Elements of Effective During Production Inspections
To maximize the benefits of during production inspections, it is essential to implement a structured inspection process. Here are some key elements to consider:
Defining Inspection Criteria
Clearly outline the inspection criteria and quality standards for each product. This may include material specifications, dimensions, tolerances, functionality, and appearance. The inspection criteria should be based on customer requirements, industry standards, and any specific product-related regulations.
Establishing Inspection Milestone
Set predetermined inspection milestones during the production process. These checkpoints may vary depending on the complexity of the product and the length of the manufacturing cycle. Typically, inspections are conducted when 20%, 50%, and 80% of the goods have been completed. Milestones ensure that quality control measures are consistent throughout production.
Using Sampling Techniques
Employ sampling techniques to inspect a representative portion of the production lot. While 100% inspection may be impractical, statistical sampling allows for a thorough assessment of product quality while keeping costs manageable. Sampling plans should be based on the acceptable quality level (AQL) criteria to ensure accuracy in detecting defects.
Documentation and Reporting
Keep detailed records of inspection findings, including any non-conformities, corrective actions, and follow-up measures. Proper documentation helps track quality trends over time and provides valuable insights for improving manufacturing processes. Comprehensive reports should be shared with relevant stakeholders to ensure transparency and accountability.
Corrective Action and Follow-Up
When defects are identified during inspections, it is important to implement corrective actions promptly. This may involve adjusting production processes, retraining staff, or revising quality control procedures. Follow-up inspections should be conducted to verify that corrective actions have been effective in resolving the issues.
Common Challenges in During Production Inspections and How to Overcome Them
While during production inspections offer many benefits, there are challenges that can arise. Understanding these challenges and implementing strategies to address them can improve inspection outcomes.
Inconsistent Quality Standards Across Suppliers
When dealing with multiple suppliers, quality standards may vary, making it difficult to maintain consistency. To address this, establish uniform inspection criteria and ensure all suppliers are well-versed in the expectations. Regular training and audits can help align quality standards across different suppliers.
Limited Access to Production Facilities
Manufacturers may not always have easy access to production sites, especially when dealing with overseas suppliers. Engaging third-party inspection companies can provide an independent assessment of product quality, ensuring that standards are maintained regardless of geographic location.
Balancing Inspection Costs with Quality Assurance
While during production inspections can reduce the risk of defects, they also come with associated costs. To balance these expenses, prioritize inspections for high-value or high-risk products. Employing risk-based inspection strategies ensures that resources are allocated effectively.
Best Practices for Implementing During Production Inspections
To fully leverage the benefits of during production inspections, companies should adhere to best practices that enhance inspection efficiency and quality control.
Integrate Inspections Into the Production Schedule
Schedule inspections at critical stages of production to avoid disruptions. By planning ahead, manufacturers can seamlessly integrate inspections without delaying the manufacturing process. Proper scheduling allows quality control teams to be more proactive in identifying and addressing potential issues.
Utilize Digital Inspection Tools
Digital tools, such as tablets and quality management software, can streamline the inspection process. These tools enable inspectors to record findings in real-time, automate report generation, and track trends over time. Digitalization also improves data accuracy, allowing for more effective decision-making.
Train Inspectors on Product Specifications and Standards
Ensure that quality inspectors are well-trained in understanding the specific requirements of the products they are inspecting. Familiarity with product specifications, industry standards, and inspection techniques is essential for identifying defects accurately and consistently.
Continuous Improvement Through Feedback Loops
Encourage continuous improvement by creating feedback loops between the inspection team and the production staff. Sharing inspection results and discussing corrective actions fosters a culture of quality and helps reduce defect rates over time.
During production inspections are an indispensable component of effective quality management in manufacturing. By conducting inspections throughout the production process, companies can ensure that their products meet the highest standards of quality, reduce costs associated with defects, and enhance customer satisfaction.
The Role of Third-Party Inspection Companies in During Production Inspections
For businesses that do not have the internal resources to conduct thorough during production inspections, partnering with third-party inspection companies can be a valuable solution. These companies provide unbiased evaluations and can offer specialized expertise in quality control. By utilizing third-party inspection services, businesses can benefit from additional insights, improved compliance with international standards, and enhanced credibility with customers.
Need a reliable partner for your during production inspections? ECQA offers professional third-party inspection services tailored to your business needs. Contact us today to ensure quality and compliance at every stage of your production process.