
How Packaging Inspection Reduces Product Damage During Shipping
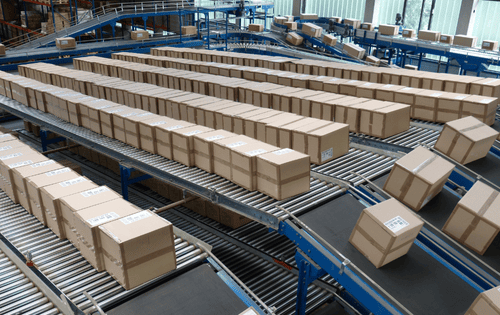
Packaging inspection is the process of examining and assessing the quality and suitability of packaging materials and designs. This is crucial for ensuring that products are protected, preserved, and presented appropriately during transportation, storage, and display. This process ensures that packaging not only meets industry standards but also possesses the strength and durability required to protect products throughout transit.
By identifying weaknesses in packaging materials and implementing robust quality control measures, companies can significantly reduce product damage, prevent costly returns, and deliver a consistently high-quality experience to their customers.
The Importance of Packaging Inspection in Product Quality Control
Packaging serves as the first line of defense for products against physical, chemical, and environmental threats. Without appropriate packaging materials, goods are vulnerable to damage from shocks, vibrations, moisture, and temperature changes.
Packaging quality control ensures that types of packaging used for various products meet industry standards and are capable of protecting items throughout the logistics process. For more insights into how this aligns with comprehensive quality strategies, see our article on Why Product Inspection Is Essential for Quality Assurance.
By incorporating comprehensive packaging inspection and testing procedures, companies can effectively assess the packaging quality before shipping. This approach involves a series of tests to verify whether the packaging materials can endure the stresses and strains associated with transportation. Such tests are essential to ensure that products are well-protected against potential hazards and to avoid costly returns or repairs.
Common Types of Packaging Defects
During transportation, products can be roughly handled during shipping, which places stress on the packaging. There are several common defects that may arise due to inadequate packaging materials or faulty packaging quality control, including:
Weak Packaging Materials
Using low-quality materials can cause packaging to tear, collapse, or fail under pressure, leading to shipping damage and product loss. Choosing durable materials that meet industry packaging standards ensures better protection and reduces the risk of customer complaints.
Incorrect or Missing Labels
Misprinted, missing, or unreadable labels can result in shipping delays, regulatory fines, or confusion in handling. Packaging labels must be clear, accurate, and compliant with international shipping regulations to avoid disruptions in the supply chain.
Poor Sealing and Adhesion
Weak adhesive, improper heat sealing, or loose tape can compromise packaging integrity, making products prone to leaks, contamination, or tampering. Using tamper-evident seals and testing adhesive strength can prevent these issues.
Incorrect Packaging Size
Packaging that is too small can crush the product, while oversized packaging allows excessive movement, increasing the risk of damage. Proper packaging design and fit testing help minimize breakage and optimize shipping efficiency.
Contaminated Packaging
Dirt, moisture, and foreign particles inside packaging can affect product quality and pose health risks, especially for food, pharmaceuticals, and electronics. Strict quality control inspections can prevent contamination and ensure compliance with safety regulations.
Lack of Protective Cushioning
Insufficient padding, shock absorption, or waterproof layers make fragile products vulnerable to transit damage. Adding bubble wrap, foam inserts, or corrugated layers ensures better protection during international shipping.
Low-Quality Printing
Faded, smudged, or peeling print can make handling instructions or branding unreadable, leading to customer dissatisfaction and compliance issues. Using high-quality printing techniques ensures labels remain intact throughout distribution.
Non-Compliant Packaging
Failure to meet packaging compliance standards, such as incorrect recycling symbols, missing safety warnings, or banned materials, can lead to shipment rejection, fines, or recalls. Regular regulatory audits help businesses stay compliant with global trade laws.
Key Steps in the Packaging Inspection Process
1. Visual Inspection for Quality Control
The first step in packaging inspection is a thorough visual inspection of the packaging materials. Inspectors check for signs of visible damage, defects, or irregularities in the packaging. This includes examining the exterior for scratches, tears, or dents, as well as assessing the quality of seals and closures.
Visual inspection also involves verifying the accuracy of labels, barcodes, and shipping information to ensure that products are correctly identified and traceable throughout the supply chain.
2. Testing Packages for Strength and Durability
A crucial aspect of packaging quality control is testing the strength and durability of packaging materials. Various testing methods are used to simulate real-world shipping conditions, ensuring that the types of packaging can withstand the rigors of transit. Some standard testing methods include:
- Drop Testing: Packages are dropped from specified heights to simulate accidental drops during handling. This test helps to assess the impact resistance of the packaging.
- Compression Testing: This involves applying pressure to the package to evaluate its resistance to stacking loads. It ensures that the packaging can support the weight of other packages during storage and transportation.
- Vibration Testing: This test simulates the vibrations that occur during transportation, especially when goods are shipped by road or rail. It helps to identify potential weaknesses in the packaging that may lead to product damage.
- Climatic Testing: This involves exposing the packaging to different environmental conditions, such as extreme temperatures, humidity, and moisture, to ensure that it can withstand varying climates.
By performing these tests, companies can assess the protective capabilities of their packaging solutions and make necessary adjustments to improve packaging quality.
3. Evaluating the Suitability of Packaging Materials
Different products require different types of packaging to ensure adequate protection during shipping. For example, fragile items such as glassware or electronics may need specialized packaging materials like foam inserts or bubble wrap, while perishable goods may require insulated packaging to maintain the correct temperature.
Evaluating the suitability of packaging materials for each product type is a critical step in the packaging inspection process. It ensures that the chosen materials provide the right balance of strength, flexibility, and cushioning needed to protect the product.
For more information on packaging standards and testing procedures, visit the International Safe Transit Association (ISTA)
Packaging is just one critical step in the pre-shipment inspection process. However, many importers make costly mistakes that compromise product quality and delivery. Avoid these pitfalls by reading 10 Common Mistakes of Pre-Shipment Inspection.
Proper packaging quality control ensures that products reach their destinations intact, ready for use or sale, regardless of the shipping conditions. By prioritizing packaging inspection and testing procedures, businesses can strengthen their supply chain resilience, protect their brand reputation, and deliver a superior experience to their customers.
ECQA provides pre-shipment inspection to ensure your packaging meets the highest standards and minimizes the risk of shipping damage. Our expert inspection services help you deliver exceptional quality from production to the final destination. Contact ECQA today to learn more about how we can support your packaging and product quality needs.
Leave a Comment