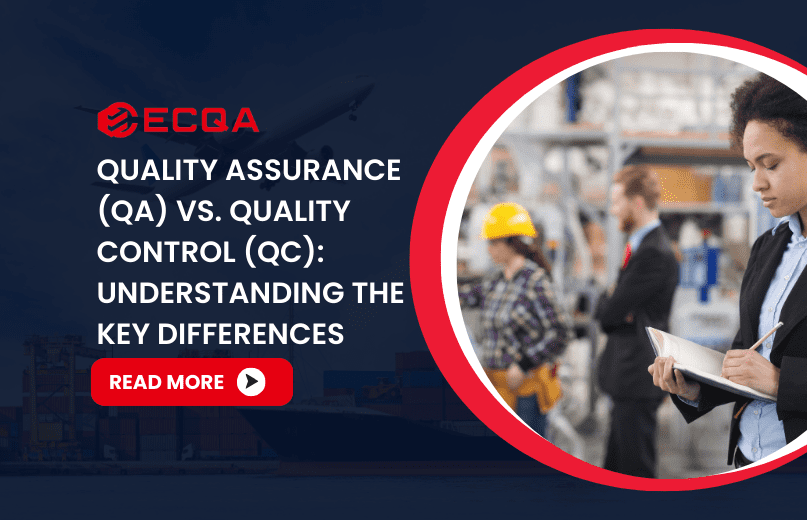
Quality Assurance (QA) vs. Quality Control (QC): Understanding the Key Differences
Quality Assurance (QA) and Quality Control (QC) are two essential components of the quality management process. Both are crucial in ensuring that products and services meet the required standards and specifications. While they are closely related, they have distinct roles and approaches in maintaining and improving quality.
Definition of Quality Assurance (QA)
Quality Assurance (QA) refers to the planned and systematic activities implemented in a quality system to ensure that the product or service will fulfill given requirements for quality. It focuses on preventing defects and errors in the processes used to create products or deliver services.
Definition of Quality Control (QC)
Quality Control (QC), on the other hand, involves the activities and techniques used to fulfill requirements for quality. It is a process-oriented approach that focuses on identifying and correcting defects in the finished product or service.
Key Differences Between QA and QC
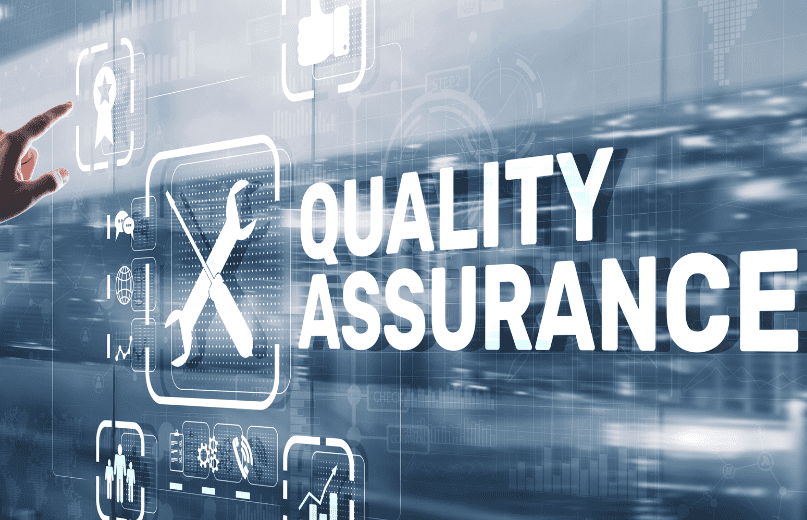
Focus of QA: Preventing Defects and Errors
The key distinctions between Quality Assurance (QA) and Quality Control (QC) lie in their core focus and approach. QA is a proactive process that aims to prevent defects by establishing and maintaining robust quality standards and procedures throughout the entire development or production lifecycle. It emphasizes the implementation of processes, training, and audits to ensure that the product or service is designed and developed correctly from the outset.

Focus of QC: Identifying and Correcting Defects and Errors
In contrast, QC is a reactive product-oriented approach that focuses on identifying and correcting defects in the final output. QC utilizes inspection, testing, and measurement to verify that the finished product or service meets the specified requirements and is free from defects. While QA strives to build quality into the system from the beginning, QC acts as a final checkpoint to ensure customer satisfaction and compliance with standards.
Methods Used in QA and QC
QA involves activities such as process documentation, quality planning, and implementation of quality management systems. It focuses on proactive measures to prevent defects, such as training, process control, and continuous improvement.
QC, on the other hand, involves activities such as product inspections, testing, and statistical process control. It is a reactive approach that aims to identify and correct defects in the final product or service.
Relationship Between QA and QC
While QA and QC have different focuses and approaches, they are interrelated and complementary. QA sets the framework for establishing processes and standards to prevent defects, while QC ensures that the processes are effectively implemented and the final output meets the desired quality criteria.
Feature | Quality Assurance (QA) | Quality Control (QC) |
---|---|---|
Focus | Preventing defects and ensuring compliance with standards and specifications | Identifying and correcting defects in the final product or service |
Approach | Proactive and preventive | Reactive and corrective |
Activities | Establishing quality standards, processes, and procedures; Monitoring and evaluating the quality management system | Testing, inspecting, and evaluating products or services |
Aim | Ensuring the product or service is designed and developed correctly | Ensuring the product or service meets the customer’s requirements and is free from defects |
Understanding the differences between QA and QC is crucial for organizations to effectively manage and improve the quality of their products and services. By implementing both QA and QC processes, businesses can ensure that their products and services meet the required standards and specifications, leading to customer satisfaction and business success.
QA and QC work together to ensure overall quality management by preventing defects in processes and identifying/correcting defects in the final output. Their significance is evident in various industries, including manufacturing, healthcare, construction, and technology, where quality management is essential for success and competitiveness.
At ECQA, we understand the importance of both Quality Assurance and Quality Control in achieving supply chain excellence. Our third-party inspection services encompass a wide range of QA and QC activities, including inspections, testing, audits, and certification. Partner with ECQA to leverage our expertise and global reach to ensure your products meet the highest quality standards, minimize risks, and achieve sustainable success.
Leave a Comment