
Comprehensive Guide to Pre-Shipment Inspection (PSI)
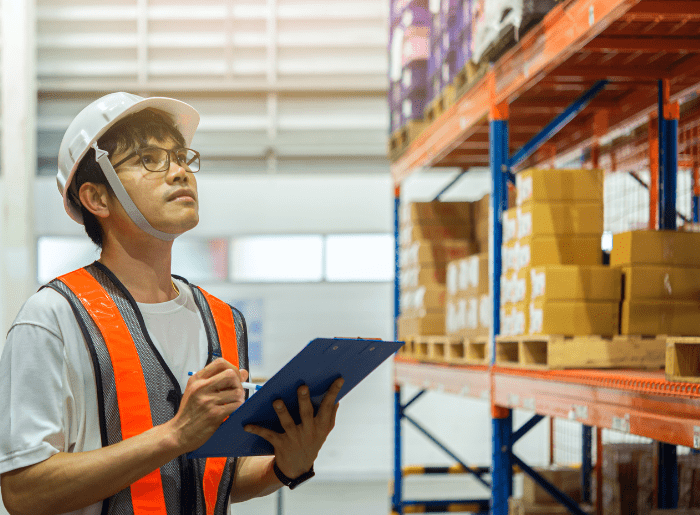
What is Pre Shipment Inspection (PSI)
Pre shipment inspection (PSI) is a crucial quality control process carried out before products are shipped from the manufacturer or supplier to the buyer. Its main purpose is to ensure that the goods being shipped meet the required specifications, standards, and contractual agreements between the buyer and seller.
PSI helps prevent issues like poor quality, incorrect quantities, packaging defects, or regulatory non-compliance, which could lead to disputes, delays, or financial losses.
A pre shipment inspection is typically conducted when 80% of the production is complete, ensuring the goods meet the agreed-upon specifications. This guide outlines the comprehensive steps involved in PSI, the benefits of the process, and best practices for businesses looking to enhance product quality and compliance while reducing the risk of defects and delays.
Key Objectives of Pre Shipment Inspection
Avoiding Costly Disputes
Disputes over defective or non-compliant goods can strain relationships and lead to financial losses. A thorough inspection minimizes the chances of disputes by ensuring that products align with the agreed-upon terms before shipment.
Ensuring Compliance With Regulations
Many countries have strict regulations governing imported goods. Non-compliance can result in customs delays, hefty fines, or even outright rejection of shipments. Pre-shipment inspection ensures that all products meet local and international standards, avoiding such setbacks.
Building Trust in Supply Chain Relationships
Trust is the cornerstone of successful trade relationships. Buyers who receive products that consistently meet their expectations are more likely to maintain long-term partnerships with sellers. Similarly, sellers who prioritize inspections demonstrate their commitment to delivering value.
Enhancing Customer Satisfaction
Satisfied customers are the backbone of a successful business. By delivering high-quality, defect-free products, businesses can exceed customer expectations, leading to repeat orders and positive word-of-mouth referrals.
Protecting Brand Reputation
A single defective shipment can tarnish a brand’s reputation, especially in the age of social media where news spreads rapidly. Pre-shipment inspection helps businesses maintain their credibility and uphold their brand image in the marketplace.
Pre shipment inspection services can uncover potential issues early, allowing businesses to take corrective action before goods are shipped, thus preventing costly returns or disputes with customers.
To learn more about potential problems, read Common Defects in Pre-Shipment Inspections.
Steps Involved in a Pre Shipment Inspection
1. Quantity Verification
During a pre shipment inspection, the inspector will first verify the quantity of products. This ensures that the correct number of units has been produced and packed according to the purchase order or contract.
2. Product Quality Check
The inspector assesses the overall quality of the products by selecting random samples from the batch. They evaluate the materials used, the workmanship, and whether the final product matches the approved sample or product specifications. This is a critical step in quality control.
3. Functionality Testing
For certain product categories, such as electronics or machinery, functionality tests are performed to ensure that the product operates as expected. This helps businesses avoid delivering defective products, which could damage their reputation and reduce risks.
4. Visual Inspection
A visual inspection checks for any visible defects such as scratches, dents, color discrepancies, or incorrect branding. These inspections are critical for consumer goods that need to maintain a high level of aesthetic quality and ensure the products meet the buyer’s expectations.
5. Packaging Inspection
Proper packaging ensures the safe transportation of goods. The inspector verifies that the packaging materials meet safety standards and that the products are packed securely to withstand potential shipping hazards. This step also includes checking the labels and any regulatory information printed on the packaging.
6. Compliance with Regulatory Standards
This is a critical aspect of pre-shipment inspection, as it ensures that products meet all applicable health, safety, and environmental regulations. Compliance with standards like CE marking for products exported to the European Union is essential to avoid legal issues and ensure safe trade practices.
7. Review of Documentation
The PSI also involves reviewing the shipping documents, such as the packing list, invoice, and bill of lading, to ensure they align with the actual shipment. This step helps reduce the chances of delays at customs due to discrepancies in the paperwork and provides a thorough inspection report.
Types of Pre Shipment Inspection
Pre shipment inspections typically offer customizable options for the inspection process. They usually adhere to the AQL (Acceptable Quality Limits) standard, which sets thresholds for acceptable quality based on the severity of defects. However, if you require every item to be checked, you can opt for a full inspection.
1. Full Inspection
In this type of inspection, every single unit of the production batch is examined for quality, quantity, and defects. Full inspections are typically requested for high-value goods or when the buyer requires absolute certainty that no defective products are being shipped.
2. Random Inspection (AQL Inspection)
A more common approach, random inspections are performed based on Acceptable Quality Level (AQL) standards. Inspectors randomly select a sample size from the batch, and the number of acceptable defects is pre-determined. If the defects exceed this number, the batch is rejected. This method is widely used in international trade to ensure the goods meet the buyer’s requirements while reducing the risk of defects.
For a comprehensive guide on AQL standards, download our free AQL table ebook here.
Why Pre-Shipment Inspections Are Crucial
1. Ensuring Product Quality
The most important benefit of PSI is ensuring that the product meets the quality control standards expected by the customer. Poor-quality products can lead to customer dissatisfaction, complaints, and negative reviews, ultimately harming your business’s reputation in international trade.
2. Avoiding Shipping Delays
By catching potential issues early, pre-shipment inspection services help you avoid shipment delays that could arise from incorrect product labeling, documentation errors, or non-compliance with regulatory standards. The inspection report helps you stay on top of any inconsistencies that may require immediate correction.
3. Reducing Costs Associated with Returns and Refunds
Without proper pre-shipment inspection services, businesses may unknowingly ship defective or non-compliant products. This leads to costly returns, refunds, or even product recalls. A well-executed PSI process can reduce risks and minimize these financial setbacks.
4. Compliance with Import Regulations
Different countries have strict import regulations, and non-compliance can lead to fines, shipment holds, or product rejections. PSI ensures that your products comply with these regulations, making customs clearance smoother and faster in international trade.
5. Enhancing Supplier Accountability
Pre-shipment inspections act as a layer of quality control and accountability for suppliers. By implementing PSI, you ensure that your suppliers adhere to the agreed-upon specifications and maintain high standards in their manufacturing processes, providing peace of mind that the products meet expectations.
Challenges and Limitations of Pre-Shipment Inspections
While pre-shipment inspections are invaluable for ensuring product quality and compliance, they come with specific challenges and limitations. Businesses must be aware of these aspects to effectively navigate potential issues.
1. Subjectivity in Quality Assessment
Inspectors may occasionally interpret quality standards differently, leading to inconsistencies in evaluation. Establishing clear and objective criteria minimizes this risk.
2. Limited Scope
Pre-shipment inspections focus on detecting visible and measurable defects. They may not identify latent issues, such as long-term durability problems, unless additional testing is conducted.
3. Dependence on Supplier Cooperation
Suppliers must provide access to facilities, samples, and documentation. Non-cooperative suppliers can delay or compromise the inspection process.
4. Logistics and Time Constraints
Coordinating inspections in remote or high-volume production sites can be logistically challenging and time-consuming, especially for last-minute orders.
5. Costs
While inspections mitigate significant risks, the associated costs can be prohibitive for smaller businesses. Striking a balance between affordability and thoroughness is essential.
By acknowledging and addressing these challenges, businesses can maximize the effectiveness of pre-shipment inspections.
Industries That Rely on Pre-Shipment Inspections
The importance of pre-shipment inspections spans across numerous industries, each with unique requirements and standards. Below are some sectors where these inspections are particularly critical:
1. Consumer Goods
From electronics to apparel, pre-shipment inspections are vital in verifying that consumer goods meet quality and safety standards. Defective products in this sector can lead to customer dissatisfaction and damage to brand reputation.
2. Food and Agriculture
In the food industry, inspections ensure that products comply with health and safety regulations, including checks for contamination, freshness, and proper packaging. Agricultural exports often require inspections for pests, diseases, and compliance with import restrictions.
3. Industrial Machinery
Heavy machinery and industrial equipment demand rigorous inspections to confirm functionality, durability, and compliance with technical specifications. Defects in this sector can lead to operational failures and significant financial losses.
4. Textiles and Apparel
For textiles, inspections focus on verifying color, stitching, measurements, and fabric quality. Ensuring these elements align with buyer expectations is crucial in this highly competitive industry.
Each industry benefits from tailored inspection services, highlighting the adaptability and significance of pre-shipment inspections in global trade.
Who Conducts Pre-Shipment Inspections?
Pre-shipment inspections are typically conducted by third-party inspection companies like ECQA or professional inspectors with expertise in quality control. These professionals play a vital role in ensuring that inspections are impartial, thorough, and accurate.
Third-party inspection companies specialize in conducting unbiased evaluations of products before shipment. Their services include: Providing experienced inspectors trained to handle a wide range of products and industries. Offering detailed reports that help buyers and sellers address quality concerns. Ensuring that inspections are conducted in accordance with international standards.
A comprehensive pre-shipment inspection is a critical component of any successful business involved in international trade. By verifying product quality, quantity, and compliance before shipment, businesses can significantly reduce risks of shipping defective goods, avoid costly returns, and ensure customer satisfaction. Pre-shipment inspection services effectively safeguard your business, strengthen supplier relationships, and ensure compliance with global quality control standards.
A critical component of any quality control strategy is selecting the right inspection partner. To ensure that your business is fully protected during the inspection process, it is essential to choose an experienced and reputable inspection company. For guidance on making this important decision, check out our detailed article on How to Choose the Best Pre Shipment Inspection Provider.
FAQ of Pre Shipment Inspection
1. What is a pre-shipment inspection?
A pre-shipment inspection is a thorough examination of goods before they are shipped to the buyer. It ensures that products meet agreed specifications, comply with regulations, and are free from defects, reducing risks and protecting both buyers and suppliers.
2. When should a pre-shipment inspection be conducted?
Pre-shipment inspections are typically carried out when 80% to 100% of the production is complete. This timing ensures that inspectors can review a representative sample of finished goods while leaving time for any necessary adjustments.
3. Who performs pre-shipment inspections?
Pre-shipment inspections are conducted by third-party inspection companies, in-house quality control teams, or government-authorized agencies. Third-party inspectors are often preferred for their impartiality and expertise.
4. What standards are used during a pre-shipment inspection?
Inspections adhere to internationally recognized standards like ISO 2859-1 (AQL standards) for sampling and quality control. Specific industry standards and buyer-supplier agreements may also be applied.
5. What is checked during a pre-shipment inspection?
Inspectors evaluate various aspects, including product quantity, physical appearance, dimensions, functionality, labeling, packaging, and compliance with legal and regulatory requirements.
6. How long does a pre-shipment inspection take?
The duration depends on the complexity and volume of the shipment. On average, inspections for standard goods may take one to two days, while specialized products may require additional time.
7. What happens if defects are found during a pre-shipment inspection?
If defects are discovered, the inspector provides a detailed report highlighting the issues. Buyers can request corrective actions, renegotiate terms, or reject the shipment depending on the severity of the defects.
8. Is a pre-shipment inspection mandatory?
While not always mandatory, pre-shipment inspections are often required for regulatory compliance, especially in industries like pharmaceuticals, electronics, and food. Many buyers also insist on inspections to ensure quality assurance.
9. How much does a pre-shipment inspection cost?
Costs may vary depending on factors such as product type, inspection complexity, and location. Please feel free to email us at market@ecqa.com to request a quotation.
10. Can pre-shipment inspections be customized?
Yes, inspections can be tailored to meet the specific requirements of the buyer or industry. This includes focusing on particular product attributes, compliance standards, or additional testing protocols.