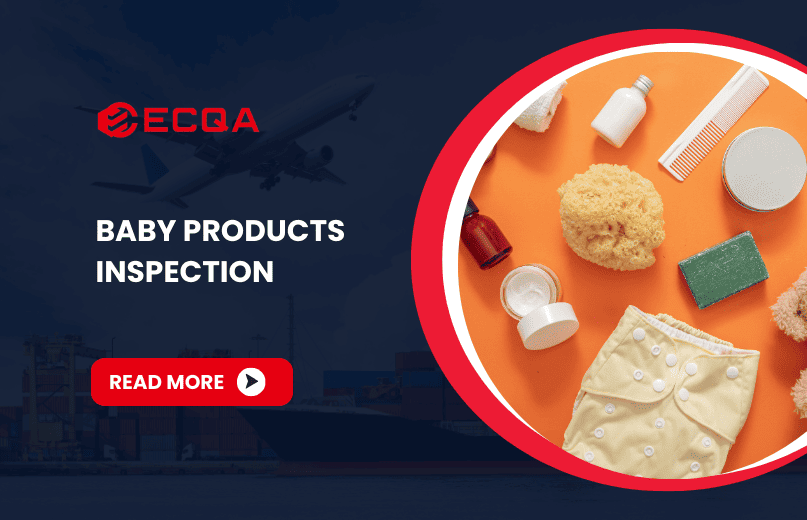
Baby Products Inspection
Baby products inspection plays a vital role in protecting infants and toddlers by ensuring each item meets strict safety and quality standards before reaching the market. Ensuring the safety and quality of baby products is not just a regulatory requirement, it’s a moral responsibility. From the tiniest pacifier to the most complex stroller, every item that reaches a baby’s hands, mouth, or skin must meet the highest standards of care and scrutiny.
We’ve seen firsthand how a single oversight can lead to a product recall, reputational damage, or worse—harm to a child. That’s why brands, retailers, and manufacturers who prioritize safety and compliance turn to independent third-party inspection companies to safeguard their operations.
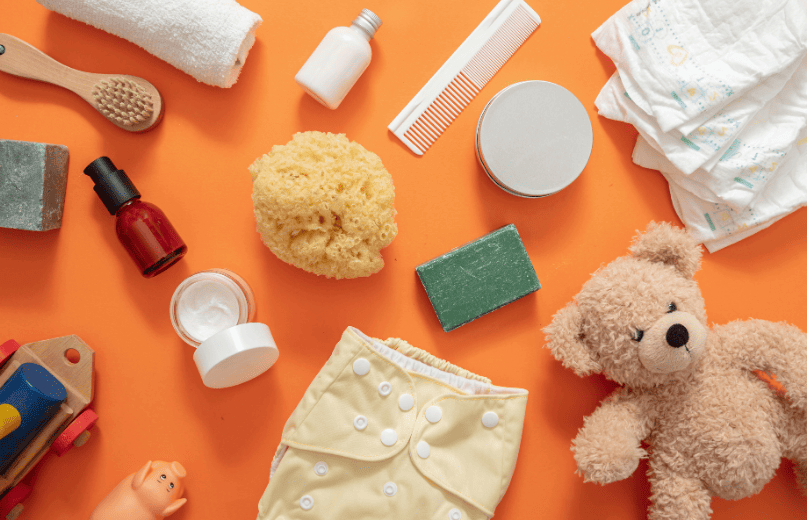
Common Quality Issues in Baby Products Inspection
No matter how sophisticated the production line or how experienced the supplier, quality issues in baby products still crop up far too often. In our years of conducting inspections, we’ve seen everything from minor cosmetic flaws to major safety hazards that could lead to choking, poisoning, or injuries.
Let’s walk through the most frequent—and potentially dangerous—problems uncovered during baby products inspection.
1. Small Parts and Detachable Components
Tiny components might seem insignificant, but for babies, they’re a choking hazard waiting to happen. Inspectors often discover:
- Loose buttons, beads, or toy eyes
- Poorly secured fasteners in rattles or plush toys
- Decorative elements glued rather than stitched
2. Sharp Edges and Burrs
Even the most adorable toy can hide a hidden danger. Sharp points, rough plastic seams, or poorly finished metal parts can scratch or cut a baby’s delicate skin.
This is especially common in:
- Molded plastic toys with flashing or sprue marks
- Metal frames on strollers or high chairs
- Zippers, snaps, and other clothing fasteners
3. Toxic Materials or Unapproved Substances
Toxic exposure is one of the gravest risks in baby products. That’s why chemical compliance testing is often paired with physical inspections—especially for items that are mouthed or worn.
Frequent culprits include:
- Lead paint, often found in colorful toys or cheap coatings
- Phthalates and BPA in plastics, especially feeding gear
- Formaldehyde in baby clothes or bedding
- Unregulated dyes that may cause skin irritation
4. Structural Weakness and Instability
If a stroller collapses mid-use or a high chair tips over, the consequences can be severe. That’s why inspectors apply real-life stress during load testing and stability checks.
Common findings include:
- Weak joints or loose screws in baby furniture
- Carriers with overstretched stitching
- Wobbly wheels or handles on walkers
- Foldable products that don’t lock securely
5. Inaccurate or Missing Labels and Instructions
You’d be surprised how often instructions are unclear—or missing altogether. Labels aren’t just a formality—they’re a vital part of product safety and legal compliance.
Typical issues include:
- Missing age recommendations or warning labels
- Labels not in the required language for the destination market
- Incorrect material disclosures (e.g., claiming “100% cotton” when it’s a blend)
- Poor translations that cause confusion
6. Poor Workmanship and Finish
Finally, many inspections turn up aesthetic or workmanship defects that, while not life-threatening, can ruin the user experience—and your reputation.
These might include:
- Misaligned seams or visible stitching errors in clothing
- Paint drips, discoloration, or uneven molding on toys
- Excess fabric threads, loose padding, or wrinkled covers
- Misprinted designs or logos
Key Categories of Baby Products That Require Inspection
The baby product industry spans a wide spectrum of items—each with its own materials, mechanics, and safety challenges. While every product deserves scrutiny, some categories carry higher risk profiles and are subject to tighter compliance standards. That’s why tailored inspection protocols are so important.
Let’s break down the most critical baby product categories where quality control can’t be left to chance.
Baby Toys and Rattles
Toys may look innocent, but when it comes to product safety, they’re one of the most highly regulated categories in the world. That’s because babies explore the world through touch and taste—meaning anything in their hands often ends up in their mouths.
Inspections for baby toys focus on:
- Choking hazards from small, detachable parts
- Sharp points or edges from broken or poorly molded components
- Tensile and torque testing to simulate pulling, twisting, and biting
- Sound level testing (for toys that produce noise) to protect sensitive hearing
- Compliance with EN 71, ASTM F963, and other regional toy safety standards
Feeding Bottles, Pacifiers, and Teething Products
Items that go directly into a baby’s mouth demand the highest level of scrutiny. That’s why inspections for feeding and teething products go beyond physical checks—material safety is front and center.
Critical inspection points include:
- Chemical testing for BPA, phthalates, and other restricted substances
- Heat resistance and sterilization durability
- Leak-proof testing for bottles, nipples, and valves
- Strength and flexibility of pacifier teats and teething rings
- Correct warning labels, age grades, and usage instructions
Lab testing is often required in tandem with on-site inspections to confirm compliance with food-grade and child-safe material standards.
Baby Clothing and Sleepwear
You wouldn’t think a onesie could pose a safety hazard, but baby apparel inspections reveal issues more often than expected. Fabrics, fasteners, and flammability are all potential red flags.
Inspection procedures for apparel typically involve:
- Stitch quality checks to prevent unraveling
- Flammability testing, especially for sleepwear
- Label verification (size, care instructions, fiber content)
- Snap and button strength tests to prevent detachment
- Chemical residue testing for dyes and textile treatments
Strollers, Carriers, and Walkers
These high-use mobility baby products must endure rough treatment while keeping babies safe and supported. That’s a tall order—and one that inspections aim to guarantee.
Key testing and inspection points include:
- Structural load testing to simulate weight under real use
- Brake and locking mechanism reliability
- Tipping and stability tests
- Fabric and frame durability under folding cycles
- Harness and strap strength
Cribs, Playpens, and High Chairs
Baby Products used during rest and feeding are held to especially high standards. One overlooked design flaw or build issue could result in suffocation, entrapment, or even falls.
Inspection teams typically evaluate:
- Spacing between slats or panels to prevent head or limb entrapment
- Weight and stability under uneven loading
- Locking mechanisms and assembly integrity
- Finish and surface smoothness to prevent splinters or cuts
- Instruction clarity and safety labels
Types of Baby Products Inspection
1. Pre-Production Inspections
Think of this as your first line of defense. A pre-production inspection takes place before the actual manufacturing begins. It focuses on evaluating raw materials, components, and the manufacturer’s readiness to start production.
Here’s what’s typically checked:
- Quality and conformity of raw materials (e.g., fabric for baby clothes)
- Supplier capability and production setup
- Storage conditions for sensitive materials
- Factory hygiene standards, especially for items like bottles or pacifiers
2. During Production Inspections (DUPRO)
Once production is underway, it’s not enough to trust that everything’s going to plan. That’s where a DUPRO inspection comes in. Conducted when 20–80% of production is complete, it offers a real-time snapshot of product quality and assembly practices.
What inspectors look for:
- Random sampling of finished and semi-finished goods
- Workmanship quality and defect rates
- Assembly line process control
- Compliance with approved specs
- Progress versus production timeline
3. Pre-Shipment Inspections
This is your last opportunity to verify product quality before it leaves the factory. Typically carried out when 80–100% of the goods are finished and packed, pre-shipment inspections offer a full picture of your order’s compliance with specifications.
Key checks include:
- AQL sampling for defect classification (critical, major, minor)
- Functionality and safety testing (e.g., pull test for toys, weight test for high chairs)
- Visual inspection and overall workmanship
- Packaging, barcoding, and labeling accuracy
- Carton integrity and count verification
4. Container Loading Checks
Imagine your baby product passed every test—but arrives at the warehouse damaged due to poor handling or loading. That’s where a Container Loading Check becomes crucial. It’s not just about verifying that cartons are counted correctly—it’s about ensuring your baby products are loaded safely and securely.
Inspections at this stage often involve:
- Verifying container condition and cleanliness
- Confirming the correct SKUs and quantities are loaded
- Ensuring stacking, bracing, and sealing follow best practices
- Preventing water, odor, or pest contamination
- Recording the loading process for transparency
Each of these inspections serves a specific purpose, but together they form a holistic quality control strategy. Partnering with a third-party inspection firm like ECQA ensures every baby product that carries your brand meets the highest global standards—before it ever meets a child.
If you’re ready to take your baby product quality control to the next level, don’t settle for anything less than the best. Partnering with a trusted, experienced third-party inspection company ensures your baby products meet international safety standards and exceed customer expectations.
At ECQA, we specialize in offering comprehensive, tailored baby products inspection services to keep your baby products safe, compliant, and market-ready. Contact us today to learn how our expert team can help you navigate the complexities of product inspections and build a trustworthy, quality-driven brand.