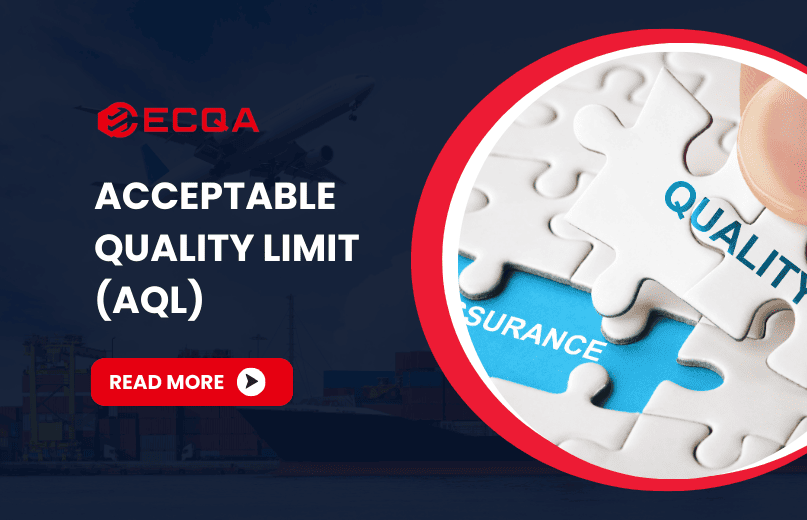
Acceptable Quality Limit (AQL)
The Acceptable Quality Level (AQL) is a key concept in quality assurance that helps businesses ensure products meet required standards before reaching customers. This method, based on statistical sampling, offers a straightforward way to determine if a production batch meets the necessary quality requirements. For manufacturers, importers, and retailers, using AQL helps strike the right balance between maintaining quality and keeping inspection costs manageable.

At its core, AQL sets the highest number of defects—whether by unit or percentage—that can be tolerated in a sample. It’s an essential part of the inspection process, allowing businesses to decide whether a batch is good to go, needs to be rejected, or requires further work. Industries such as electronics, textiles, toys, and medical devices commonly use AQL to maintain consistency and high quality across global supply chains.
In this article, we’ll take a close look at AQL, diving into how it works, its applications, and how businesses can use it to improve product quality and meet customer expectations. By the end, you’ll see why AQL is so crucial for achieving compliance and staying competitive in the marketplace.
Importance of AQL in Quality Assurance
Quality assurance (QA) is a crucial part of any successful manufacturing or production process, and AQL plays a key role within QA frameworks. It acts as a standard for determining whether a product batch meets customer and regulatory requirements, giving businesses a reliable way to evaluate quality.
One of AQL’s biggest advantages is its ability to simplify inspections without the need to test every single item. By focusing on representative samples, businesses can save both time and money while still ensuring the products are reliable. Plus, AQL helps companies reduce the risks that come with defective products, like costly recalls, legal issues, and damage to their reputation.
For companies operating in global markets, adhering to international standards such as ISO 2859 or ASTM D4753 often means implementing AQL inspections. Using AQL shows a company’s commitment to quality, which is key to building customer trust and securing long-term contracts with distributors and retailers.
AQL inspections also promote accountability throughout the supply chain. Suppliers are more likely to meet agreed-upon quality levels, leading to stronger partnerships and fewer disputes. In industries like healthcare, where product reliability is critical, AQL ensures that only safe and functional items reach the end users, protecting public health and safety.
The AQL is a statistical approach used for sampling and inspecting products, helping manufacturers and inspectors assess quality efficiently. The main goal of AQL is to provide a reliable way to determine whether a production batch meets acceptable quality standards, without the need to inspect every single item.
Key Components of the AQL
1. Lot Size
This is the total number of units in a production batch, and it plays a key role in determining the sample size that needs to be inspected.
2. Sample Size
This refers to the number of units selected from the lot for inspection. A predefined sampling plan, like the one in ISO 2859-1, is used to calculate the appropriate sample size.
3. Acceptance Quality Limits
These are the preset thresholds for critical, major, and minor defects. If the number of defects in the sample exceeds these limits, the batch fails the inspection.
4. Inspection Levels
- General Levels: There are three levels (I, II, and III) used for standard inspections, with Level II being the most commonly applied.
- Special Levels: These are used when a more specific inspection is needed, such as for highly sensitive products.
5. AQL Tables
- The AQL system uses standard tables, like the AQL Sampling Tables, to determine the sample size and acceptable defect limits. These tables help inspectors choose the right sampling plan based on the lot size and the desired quality standards.
6. Steps in an AQL Inspection
- Define the lot size and determine the appropriate AQL level.
- Use the AQL table to figure out the required sample size.
- Inspect the selected items for defects and categorize them as critical, major, or minor.
- Compare the number of defects to the acceptable threshold.
- Decide whether to accept or reject the batch based on the inspection results.
The AQL system offers a clear, structured process that ensures consistent quality assessments across industries. Its flexibility makes it a popular choice for businesses that want to maintain high standards while keeping inspection costs in check.
Types of Defects in AQL Inspection
In AQL inspections, defects are grouped into three main categories: critical, major, and minor. Understanding these classifications is key for businesses that want to keep product quality high while minimizing rejection rates. Each type of defect has different implications for usability, compliance, and customer satisfaction.
Critical Defects
Critical defects are the most serious, posing significant risks to user safety, product functionality, or regulatory compliance. Products with critical defects are generally considered unfit for sale or use. Examples include:
- A sharp edge on a children’s toy that could cause injury.
- A malfunctioning part in a medical device that affects its performance.
- Contamination in food products that violates health regulations.
The tolerance for critical defects is often set to zero, meaning that no critical defects are acceptable under any circumstances.
Major Defects
Major defects reduce the product’s usability or performance but typically don’t pose an immediate safety risk. These defects are more likely to cause customer dissatisfaction and returns. Examples include:
- A torn garment or noticeable stitching errors.
- A malfunctioning feature in an electronic device.
- Packaging that doesn’t protect the product well during transport.
The threshold for major defects is usually higher than for critical defects, but still stringent to ensure product reliability.
Minor Defects
Minor defects are small cosmetic issues that don’t affect the product’s functionality or intended use. While they don’t impact performance, these defects can reduce the perceived quality of the product. Examples include:
- A tiny scratch on a metal product’s surface.
- Slight discoloration on plastic parts.
- Misaligned labels or logos on packaging.
The tolerance for minor defects is more relaxed, as their impact on overall quality is minimal.
By classifying defects, AQL inspections help businesses focus their quality control efforts where it matters most, balancing high standards with operational efficiency.
The AQL Sampling Plan
The AQL sampling plan is the foundation of the inspection process, offering a structured approach to assess product quality. It’s a statistical framework that helps determine how many units should be inspected and how to decide if a batch meets the acceptable quality level.
Steps in Creating an AQL Sampling Plan
- Define the Inspection Parameters: Choose the lot size, inspection level, and AQL levels for critical, major, and minor defects.
- Consult the AQL Table: Use the AQL sampling tables to find the sample size code letter and its corresponding sample size.
- Conduct the Inspection: Inspect the chosen sample size and note any defects.
- Analyze the Results: Compare the defect count to the acceptable thresholds for acceptance or rejection.
- Make a Decision: Accept or reject the batch based on the inspection results.
Calculating AQL: A Step-by-Step Guide
Calculating AQL involves applying statistical principles to determine the acceptable defect levels in a product batch. By learning how to calculate AQL, businesses can make informed decisions about quality control and ensure their products meet industry standards.
Step-by-Step Guide to AQL Calculation
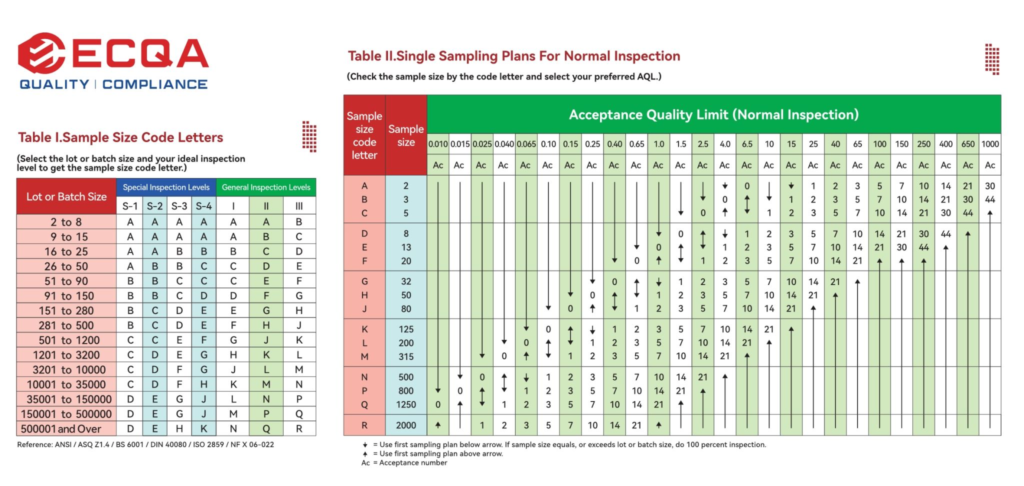
- Identify the Lot Size: Determine the total number of units in the batch to be inspected.
Example: A batch contains 5,000 units.
- Select the Inspection Level: Choose the appropriate inspection level based on the product type and quality requirements.
Example: General Inspection Level II.
- Determine the AQL Levels: Set the AQL thresholds for critical, major, and minor defects.
Example: Critical defects = 0%, Major defects = 1.5%, Minor defects = 4.0%.
- Consult the AQL Table: Find the row corresponding to the lot size and chosen inspection level. Identify the sample size code letter and its corresponding sample size.
Example: Lot size of 5,000 units with Level II gives code letter L, corresponding to a sample size of 200.
- Inspect the Sample: Examine the selected sample units and categorize any defects.
Example: Inspect 200 units and record 1 critical defect, 2 major defects, and 5 minor defects.
- Compare to AQL Thresholds: Refer to the AQL table to check the acceptance and rejection thresholds for the defects.
Example: AQL thresholds allow 0 critical defects, 7 major defects, and 10 minor defects.
- Make the Decision: Accept or reject the batch based on whether the defects fall within the acceptable range.
By mastering the AQL calculation process, businesses can improve their quality assurance practices and uphold high standards across all production batches.
AQL and Industry Applications
The Acceptable Quality Level (AQL) is a flexible tool used across many industries to ensure products meet quality and compliance standards. Each sector adapts AQL to address its specific challenges, risks, and requirements.
Electronics and Electrical Appliances
In the electronics industry, precision and reliability are crucial. AQL helps manufacturers maintain consistency while meeting strict safety regulations.
- Critical Defects: Electrical short circuits, faulty wiring, and overheating components.
- Major Defects: Malfunctioning buttons, improper assembly, or damaged screens.
- Minor Defects: Scratches on casings or slight misalignments in ports.
- By using AQL, manufacturers can ensure complex products like smartphones or home appliances meet both performance and aesthetic standards.
Textile and Apparel
AQL is widely used in the textile and apparel industry to manage large production volumes and minimize quality issues.
- Critical Defects: Hazardous sharp objects left in clothing.
- Major Defects: Incorrect sizing, ripped seams, or fading prints.
- Minor Defects: Uneven stitching or slight color mismatches.
- AQL inspections help catch defects early, ensuring customer satisfaction and reducing returns.
Food and Beverage
In the food industry, AQL is crucial for maintaining health and safety standards, with a focus on critical defects due to the risks they pose to consumer health.
- Critical Defects: Contaminated products, foreign objects, or mislabeled allergens.
- Major Defects: Packaging errors or significant portion inconsistencies.
- Minor Defects: Slight labeling inaccuracies or minor dents in cans.
- AQL helps ensure compliance with regulatory standards and fosters consumer trust.
Automotive
In the automotive industry, safety and functionality are top priorities. AQL inspections ensure that both components and finished vehicles meet rigorous quality standards.
- Critical Defects: Faulty brakes or airbags.
- Major Defects: Improper fitting or assembly errors.
- Minor Defects: Cosmetic issues like scratches or small dents.
- AQL plays a key role in reducing recalls and enhancing brand reputation.
Benefits of Implementing AQL in Quality Control
The Acceptable Quality Limit (AQL) system is an essential part of modern quality control processes. It provides businesses with a reliable way to maintain product quality while managing inspection costs. By incorporating AQL into their operations, companies gain a range of benefits that not only ensure top-quality products but also boost operational efficiency, customer satisfaction, and brand reputation. Here’s how AQL adds value to quality control:
Enhanced Product Quality and Consistency
AQL ensures significant improvements in product quality by catching defects early and preventing them from reaching the customer. This proactive approach helps maintain consistency in product quality across all production batches, no matter the scale. When done right, AQL can identify even minor defects, creating a more rigorous quality control process that consistently meets or exceeds customer expectations.
- Early defect detection prevents defective products from being shipped.
- Ensures consistent product quality from batch to batch.
- Boosts customer satisfaction with reliable, high-quality products.
Cost-Effective and Efficient Quality Control
AQL optimizes the inspection process by focusing on sampling rather than inspecting every item. This reduces time and resources spent on inspections, leading to cost savings. Even though fewer items are inspected, AQL ensures that the sample represents the entire batch, making it a cost-effective way to maintain quality.
- Lowers inspection costs by focusing on a representative sample.
- Saves time by eliminating full-scale inspections.
- Maximizes resources by allowing focus on other important areas.
Improved Risk Management and Reduced Liability
AQL inspections help minimize risks related to product defects, which could lead to expensive recalls, legal issues, or harm to brand reputation. By identifying defects early in production or shipping, businesses can stop faulty products before they hit the market, mitigating the risk of recalls and legal problems while ensuring compliance with industry regulations.
- Minimizes the risk of legal disputes, recalls, or reputational damage.
- Proactively detects defects, preventing faulty products from reaching consumers.
- Ensures compliance with regulations to avoid costly fines or penalties.
Strengthened Supplier Relationships and Accountability
AQL strengthens relationships with suppliers by setting clear, mutual quality standards. Suppliers who know their products will be inspected using AQL are more motivated to maintain high-quality standards in their own production processes. This shared accountability reduces quality issues and fosters a collaborative partnership between businesses and suppliers, leading to more reliable supply chains.
- Clear quality standards improve communication and relationships with suppliers.
- Mutual accountability helps suppliers maintain consistent quality.
- Strengthened collaboration to address any quality issues early.
Streamlined Production and Supply Chain Processes
AQL doesn’t just improve quality control—it helps streamline the production process. By catching defects early, businesses can quickly address issues without causing major delays. This leads to greater efficiency across the supply chain, from manufacturing to distribution. With fewer defective products and better quality assurance, companies can improve inventory management and ensure only high-quality products reach customers.
- Early defect detection minimizes production delays.
- Improved inventory management ensures only high-quality products are shipped.
- Optimized supply chain processes result in faster delivery times.
Strengthened Brand Reputation
Consistently high-quality products, ensured through AQL inspections, can significantly boost a company’s reputation. Consumers are more likely to trust and remain loyal to a brand that consistently delivers quality. This reputation not only encourages repeat business but also drives positive reviews and word-of-mouth marketing. In competitive markets, a strong brand reputation is often the key differentiator.
- Builds consumer trust by maintaining high-quality standards.
- Increases brand loyalty with a consistent commitment to quality.
- Enhances market positioning, offering a competitive advantage.
Facilitates Compliance with Industry Standards
Many industries have strict quality and safety standards. AQL inspections help businesses ensure they comply with these regulations, such as ISO certifications and safety standards. By following AQL practices, businesses maintain high quality and meet necessary compliance benchmarks, avoiding penalties or the loss of certifications.
- Ensures adherence to industry regulations and standards.
- Prevents costly compliance violations by exceeding requirements.
- Supports international trade by ensuring compliance with global standards.
Increased Operational Control and Transparency
AQL inspections offer greater control and transparency over product quality. By tracking and documenting inspection results, businesses can spot trends, monitor supplier performance, and continuously improve quality management processes. This insight helps companies make informed, data-driven decisions and continuously refine their quality systems.
- Provides visibility into quality at each production stage.
- Data-driven insights help improve future inspections and processes.
- Supports continuous improvement of quality control and supplier performance.
Benefits of AQL in Supply Chain Management
Implementing the Acceptable Quality Limit (AQL) system across the supply chain offers significant advantages, enabling businesses to streamline operations and maintain a competitive edge. Below are some key benefits of incorporating AQL inspections in supply chain management:
1. Reducing Product Defects and Improving Supplier Relationships
AQL inspections play a crucial role in reducing product defects by identifying issues early in the production process, preventing defective products from reaching customers. This proactive approach helps avoid costly recalls and returns, saving businesses money and safeguarding their reputation. Furthermore, AQL fosters stronger supplier relationships by holding suppliers accountable for product quality. Clear and consistent quality standards encourage open communication, collaboration, and a shared commitment to maintaining high-quality products.
- Preventing costly defects by identifying them before shipment.
- Strengthening supplier accountability through regular and consistent quality checks.
- Fostering collaborative problem-solving when defects are identified, building trust and long-term relationships with suppliers.
2. Cost Savings Through Optimized Inspections
AQL enables businesses to implement cost-effective inspection processes by only inspecting a sample of products rather than inspecting every item in a batch. This reduces the time and resources spent on inspections while ensuring that quality remains high. Early identification of defects can also result in substantial cost savings through reduced rework, returns, and replacements. With AQL, companies can focus their resources on the most critical aspects of production, streamlining operations and maximizing efficiency.
- Resource optimization by inspecting only a representative sample instead of the entire lot.
- Reducing rework and returns by catching issues early in production, preventing costly post-production corrections.
- Streamlining operations by minimizing unnecessary inspections and focusing on critical product quality aspects.
3. Enhanced Brand Reputation Through Consistent Quality
Consistently high product quality is vital for maintaining a strong brand reputation. AQL inspections ensure that products meet customer expectations, resulting in higher levels of customer satisfaction and loyalty. When businesses can consistently deliver high-quality products, it reinforces their brand image as reliable, trustworthy, and committed to excellence. This reputation not only attracts repeat business but also encourages positive word-of-mouth referrals and enhances the company’s position in the market.
- Customer satisfaction driven by consistently high product quality.
- Building brand trust by consistently meeting or exceeding customer expectations.
- Fostering customer loyalty through dependable, high-standard products.
Common Challenges and Solutions in AQL Implementation
While the benefits of AQL are clear, implementing AQL inspections can come with certain challenges. It’s essential for businesses to understand these potential obstacles and find effective solutions to overcome them, ensuring the successful integration of AQL.
Common Challenges Businesses Face with AQL Inspections
Implementing AQL inspections across a supply chain may seem straightforward, but several common challenges can arise:
- Inaccurate Sampling
Without the right sampling techniques, AQL inspections may not accurately reflect the overall quality of a batch. Poor sampling can lead to either overestimating the quality or unnecessarily rejecting acceptable lots, both of which impact efficiency and cost.
- Inconsistent Defect Classification
Classifying defects correctly is essential for AQL to be effective. Misclassifying defects—whether by underestimating or overstating their severity—can lead to misleading conclusions about a product’s quality and affect decision-making.
- Supplier Resistance
Some suppliers may view AQL inspections as an added cost or burden. Without the right approach, this resistance can cause delays or even create conflict within the supply chain, affecting timelines and overall quality.
Mistakes to Avoid During Sampling and Defect Evaluation
To ensure AQL inspections are as effective as possible, businesses should avoid these common mistakes during the sampling and evaluation process:
- Incorrect Sampling Size
One of the most common mistakes is selecting a sample size that’s either too small or too large. A sample that’s too small may not represent the overall lot accurately, while an overly large sample can unnecessarily increase inspection costs.
- Failure to Define Clear Defect Categories
A lack of clear criteria for defining critical, major, and minor defects can lead to inconsistencies in evaluation. It’s essential that businesses and suppliers agree on these categories upfront to avoid any discrepancies during inspections.
- Lack of Documentation
Not maintaining detailed records of inspections can create confusion and make it difficult to track trends, analyze results, or resolve disputes. Proper documentation is crucial for verifying compliance and improving the inspection process over time.
How to Overcome These Obstacles with Expert Guidance
The challenges associated with AQL can be managed effectively with the help of experienced inspection service providers. Here’s how expert guidance can help:
- Optimize Sampling Plans
Professional inspection providers are skilled at calculating and implementing accurate sample sizes, ensuring that results are representative and reliable, while keeping costs in check.
- Ensure Accurate Defect Classification
Experienced inspectors are trained to identify and categorize defects based on well-established standards, reducing the chances of misclassification and ensuring consistency in evaluations.
- Facilitate Supplier Collaboration
Third-party experts can mediate discussions with suppliers, explaining the benefits of AQL inspections and helping them understand the process, which can reduce resistance and improve collaboration across the supply chain.
- Create a Clear Process for Documentation
Professionals can assist in setting up standardized documentation procedures, ensuring all inspection activities are recorded accurately and can be referenced in future inspections or audits.
By proactively addressing these challenges, businesses can maximize the benefits of AQL in their quality control processes, ensuring more accurate and reliable inspections. If you want to learn more read our FAQ: Acceptable Quality Level (AQL) in Quality Control and Product Inspections.
The Acceptable Quality Limit (AQL) system remains an indispensable tool in quality control, empowering businesses to deliver products that meet stringent standards and exceed customer expectations. By defining clear defect thresholds, adopting robust inspection methods, and leveraging advanced technologies, companies can streamline operations and achieve consistent excellence in product quality.
Adopting AQL goes beyond compliance—it reflects a commitment to superior craftsmanship, customer satisfaction, and long-term success. As industries evolve, embracing innovations like AI-driven inspections and sustainable practices ensures that AQL remains relevant and impactful. Organizations that prioritize quality through AQL gain a significant competitive advantage, securing their position as industry leaders.
At ECQA, we specialize in providing world-class AQL-based quality control services tailored to the unique needs of diverse industries. Partnering with us ensures your products meet the highest standards while streamlining your inspection processes. If you’re looking for a more in-depth guide on AQL, download our free AQL ebook today.