
Home Appliance Inspection: How to Avoid Electrical Hazards
Home appliance inspection is the technical process of evaluating household electrical devices to ensure they comply with safety standards and pose no electrical hazards during use. It involves a series of physical, functional, and electrical tests designed to detect potential risks before the products reach consumers.
Electrical hazards in household appliances are a leading cause of residential fires, product recalls, and personal injuries. These hazards may not always be visible but can result from subtle design flaws, faulty components, or inconsistent manufacturing. Left unchecked, even minor defects can evolve into serious threats under everyday usage.
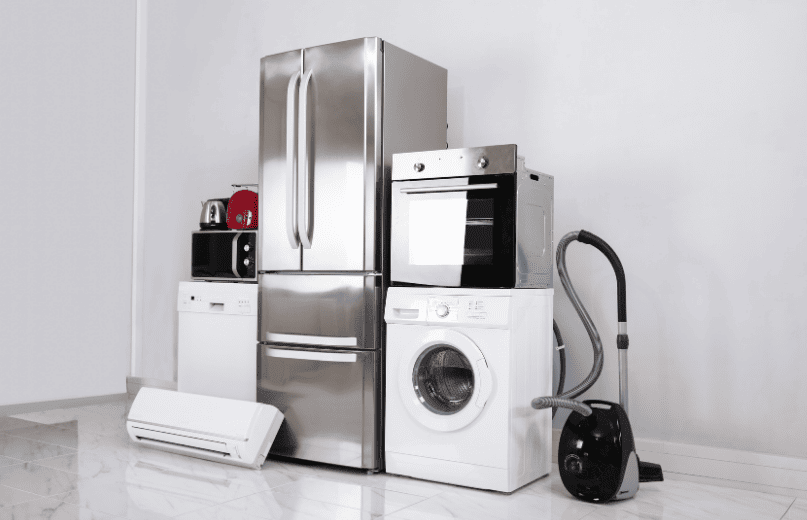
For manufacturers, importers, and retailers, the implications are significant. Non-compliant appliances not only endanger users but also expose brands to legal action, product seizures, and damaged reputation. Regulatory frameworks across markets require strict adherence to electrical safety, with enforcement agencies routinely conducting spot checks and post-market surveillance.
Common Electrical Hazards Found in Home Appliances
Household appliances are subject to wear, environmental stress, and electrical load. Several electrical hazards are frequently identified across various categories:
Overheating and Short Circuits
Appliances that draw excessive current or contain poorly rated components may overheat. If heat isn’t dissipated properly or thermal cutoffs fail, insulation can degrade and short circuits may occur, potentially igniting nearby flammable materials.
Electric Shock from Insulation Failure or Poor Earthing
Live parts must be securely insulated. When insulation breaks down due to aging, physical damage, or poor design, users may be exposed to electrical shock. Similarly, appliances without proper earthing mechanisms allow leakage current to accumulate on metal surfaces, creating high-risk conditions during operation.
Arcing and Component Failure Due to Moisture Ingress
In moisture-prone environments, such as kitchens or bathrooms, ingress protection becomes critical. Condensation or liquid exposure inside the appliance can cause arcing, corrosion of terminals, or even electrical fires particularly in units lacking appropriate IP ratings.
Cable Damage and Plug-Related Hazards
Power cords often endure repetitive bending, pulling, and pressure. Without sufficient strain relief or reinforcement, internal wires can fray or snap, leading to intermittent connections, exposed conductors, or short circuits. In some regions, plugs that don’t comply with national specifications (e.g., missing ground pins) may introduce additional risks.
Critical Inspection Areas for Electrical Safety
Effective home appliance inspection involves a structured checklist of critical tests. These tests are aligned with international safety standards and are designed to simulate real-life usage, stress conditions, and fault scenarios.
Insulation Resistance Testing
This test checks whether the insulation material between live and non-live parts maintains high resistance under test voltages. Inadequate insulation can allow leakage current to flow to accessible surfaces.
Dielectric Strength Verification
High-voltage is applied between live parts and earth or accessible surfaces to ensure insulation doesn’t break down. This test ensures that accidental overvoltage conditions won’t compromise user safety.
Leakage Current Testing
Measuring leakage current is essential to assess whether electricity is unintentionally flowing through the appliance casing or other non-conductive parts. High leakage can cause electric shock, particularly in Class I devices.
Polarity and Continuity Checks
Incorrect wiring , such as reverse polarity or broken circuit paths , can impair the appliance’s function and create fire hazards. Polarity testing ensures live and neutral wires are correctly configured; continuity checks confirm that circuits are intact and complete.
Plug, Cord, and Terminal Inspection
The physical integrity of the power cord, plug type, terminal strength, and internal connections are verified. This includes pull-force testing for cords, as well as compliance with local plug standards (e.g., BS 1363 in the UK, Schuko in Europe).
Grounding Continuity
In Class I appliances, grounding must provide a low-resistance path to safely discharge fault current. The grounding system is verified for continuity and resistance, ensuring a fail-safe path in case of insulation breakdown.
Load and Power Consumption Accuracy
Appliances are tested under rated load conditions to verify actual current draw and power consumption. Underrated internal components can fail under load, while over-spec units may exceed household circuit limits.
Together, these inspection points serve as a technical barrier against latent hazards, helping ensure that only safe, compliant units reach end users.
Appliance Categories and Their Specific Electrical Risk Profiles
Each appliance category presents unique stress points and operational risks. Inspection strategies must adapt accordingly.
Heating Appliances (e.g., Toasters, Kettles, Irons)
These devices operate at high wattage and often reach temperatures above 200°C. Risk areas include:
- Thermal protection system failure
- Inadequate heat shielding or over-temperature cutoffs
- Wiring insulation degradation under thermal stress
Refrigeration and Cooling Units
These appliances operate continuously and combine electrical and mechanical components:
- Compressor overload protection failures
- Faulty capacitors or relay wiring
- Grounding continuity for metallic frames
Portable Devices and Handheld Tools
Portability introduces mechanical risk, which compounds electrical exposure:
- Cable strain or fray due to mobility
- Moisture ingress from outdoor or wet use
- Weak plug structures prone to bending or cracking
Washing Machines and Dryers
These operate in moisture-rich environments and involve high-amperage loads:
- Water leakage onto electrical components
- Faulty insulation leading to conductive casing
- Improper grounding or unbalanced drum causing mechanical-electrical stress
Kitchen Countertop Appliances
These combine heat, moisture, and daily handling:
- Loose internal connectors due to vibration
- Inconsistent thermostat calibration
- Cord anchorage defects
Personal Care Products (e.g., Hair Dryers, Razors)
Close proximity to the body increases safety stakes:
- Insufficient double insulation (Class II devices)
- Poor quality motors causing arcing
- Exposure to water in bathrooms without IP-rated sealing
Understanding category-specific risk profiles ensures inspections are not only compliant but contextually effective.
Electrical hazards in home appliances are preventable but only when inspection is taken seriously, early, and often. Relying solely on factory self-checks or visual reviews is insufficient. A rigorous, technically structured inspection process is essential for protecting consumers, meeting regulatory obligations, and maintaining product integrity. Need reliable inspection support? Contact our team to schedule a comprehensive appliance safety evaluation.