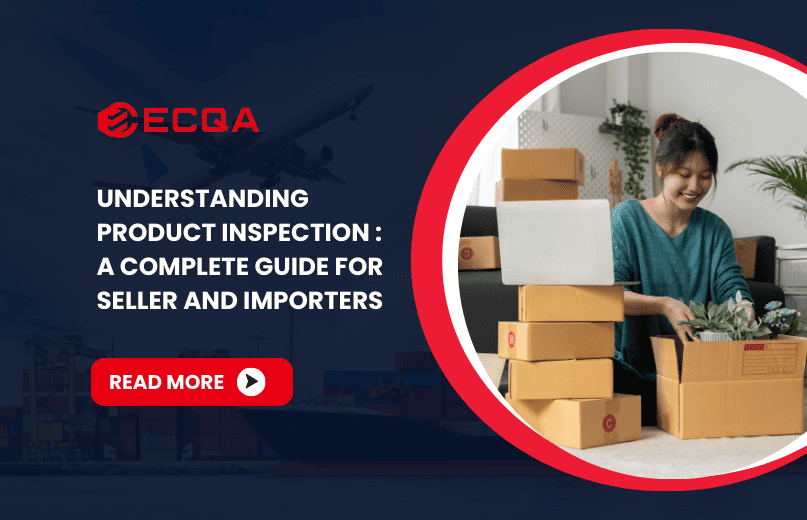
Product Inspection Guide
Product inspection is the process of verifying that goods meet your specified requirements before they move forward in the supply chain. It involves a physical check of products—either during or after production—to ensure they meet quality, safety, and compliance standards.
In global trade, where supply chains stretch across continents and time zones, this process becomes essential. You may never set foot inside your supplier’s factory. You might never meet the production manager in person. Yet you’re expected to deliver a consistent, compliant product to your customers. That’s where product inspection steps in—as your eyes and ears on the ground.
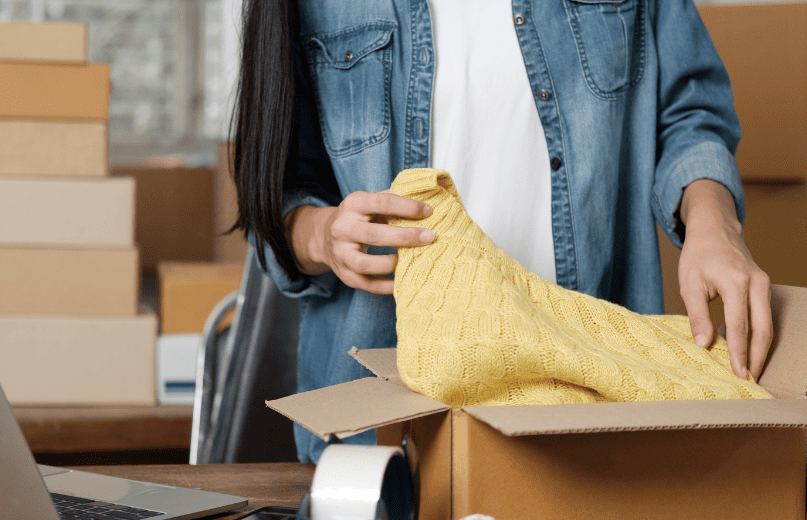
Product inspection isn’t just about catching defects—it’s about prevention. It acts as an early warning system within your quality assurance framework, identifying potential issues before they snowball into costly recalls or reputation damage.
It also plays a key role in risk management. In sectors like electronics, toys, medical devices, or industrial equipment, failing to meet regulatory standards can mean hefty fines—or worse, unsafe products reaching end users. Inspection ensures compliance with legal requirements and buyer expectations, whether you’re shipping to the EU, the U.S., or any other market with strict standards.
By inspecting your goods at the right stages, you not only protect your bottom line—you preserve the trust you’ve built with customers.
4 Types of Product Inspection
Product inspection can be tailored to different stages of your production and shipping timeline. Depending on your product type, production volume, and risk level, choosing the right type of inspection can make all the difference between a smooth delivery and a supply chain disaster.
Let’s walk through the four main types of product inspection, each serving a unique role in ensuring quality and reliability.
1. Pre-Production Inspection (PPI)
A Pre-Production Inspection (PPI) is conducted before the first unit rolls off the production line. This is when inspectors evaluate raw materials, components, and factory preparedness—long before your goods are even assembled. It’s especially valuable when working with a new supplier or launching a new product.
Ideal use cases:
- New supplier relationships where trust hasn’t yet been established
- Custom or high-value products requiring precision
- Orders involving specialized materials or components
- Projects with tight deadlines where rework time is limited
2. During Production Inspection (DPI / DUPRO)
A During Production Inspection (DPI)—also known as DUPRO—is performed when roughly 20% to 80% of the goods are completed. This mid-production checkpoint allows you to evaluate work-in-progress units and overall production consistency.
By reviewing products while they’re still on the line, you can catch issues like inconsistent stitching in garments, misaligned components in electronics, or incorrect logo placement. This gives your team the opportunity to make real-time adjustments before defects affect the entire batch.
Common checkpoints:
- Overall product quality and workmanship
- Assembly line practices and consistency
- Internal and external product dimensions
- Color, texture, labeling, and packaging accuracy
- Compliance with buyer specifications
3. Pre-Shipment Inspection (PSI)
The Pre-Shipment Inspection (PSI) is the most commonly requested form of product inspection—and for good reason. Conducted when 80% to 100% of the order is finished and packed, it provides a comprehensive review of the final product before it leaves the factory.
Critical elements reviewed before dispatch:
- Product appearance and workmanship
- Functional testing (where applicable)
- Quantity verification
- Packaging and labeling accuracy
- Barcode and marking compliance
- Carton drop tests and packaging durability
- Adherence to AQL (Acceptable Quality Limit) standards
Without a PSI, you’re essentially signing off on a product you haven’t seen. This is where many importers run into issues—receiving goods that are off-spec, poorly packaged, or non-compliant with buyer requirements. A PSI gives you the final say before shipment, ensuring what’s inside the container matches what you paid for.
4. Container Loading Check (CLC)
A Container Loading Check (CLC) doesn’t just confirm that products were manufactured correctly—it verifies that they were loaded and shipped properly. Inspectors are present at the factory or warehouse during loading, overseeing everything from packaging condition to container seals.
Key elements inspected during a CLC include:
- Container cleanliness and condition
- Verification of product quantity loaded
- Carton handling and stacking methods
- Packaging durability to avoid transit damage
- Proper labeling for export and customs clearance
- Security seals and documentation
Each of these product inspection types serves a distinct purpose. In many cases, a combination of inspections offers the best protection, especially for complex or high-stakes shipments.
Next up, we’ll dive into What a Product Inspection Covers—because knowing what gets checked is just as important as knowing when to check it.
What Do Inspectors Check During Product Inspections
When you hire a third-party to conduct a product inspection, what actually happens on the ground? It’s more than just a quick glance at the goods. Professional inspectors follow a structured and meticulous process to verify whether your products meet the agreed-upon specifications—and whether they’re fit for market.
Let’s break down the key elements that are typically assessed during a product inspection.
1. Visual Inspection
The first and most immediate aspect of any product inspection is the visual check. Inspectors carefully examine the physical appearance of the product to identify any visible defects, poor craftsmanship, or inconsistencies.
What they look for:
- Surface defects like scratches, dents, discoloration, or uneven finishes
- Incorrect or missing labels (such as barcodes, logos, compliance marks)
- Poor packaging quality (crushed boxes, missing inserts, weak sealing)
- Inconsistent branding or incorrect printing
- Workmanship flaws like loose stitching, rough edges, or misalignment
2. Function and Performance Testing
This is where inspectors roll up their sleeves and put the product to the test. For functional items—whether it’s a coffee maker, a power tool, or a Bluetooth speaker—inspectors check whether it works as intended under real-world conditions.
What this may involve:
- Turning electronic devices on and off to check power functions
- Verifying buttons, switches, or touchscreens work properly
- Testing mechanical movement (e.g., zippers, hinges, sliding parts)
- Conducting basic durability checks (can it survive normal use?)
- For toys or electronics: battery tests, connectivity tests, or signal checks
3. Measurement and Specifications
In many industries—especially apparel, electronics, and industrial components—precision matters. Inspectors use calibrated tools to verify that product dimensions match your technical specifications or engineering drawings.
Typical tools and measurements:
- Calipers to measure width, thickness, and diameter
- Measuring tapes and rulers for length and height
- Multimeters for electrical resistance or current checks
- Scales for verifying product and packaging weight
4. Compliance and Safety Standards
One of the most important aspects of any product inspection is ensuring that the product meets regulatory and safety requirements for its destination market.
Inspectors will check for:
- Required certification labels (such as CE, FCC, RoHS, FDA, UKCA)
- Proper warning labels, language translations, and user manuals
- Safety-critical features (e.g., child-safe locks, electrical insulation)
- Presence of batch numbers or traceability codes
- Evidence of restricted substance testing (like lead, BPA, phthalates)
5. Sampling Methods and AQL (Acceptable Quality Limit)
Inspectors don’t check every single unit in a shipment (unless you pay for a full inspection). Instead, they follow internationally recognized sampling procedures to check a statistically valid portion of the goods.
The most widely used method is based on:
- ANSI/ASQC Z1.4 (used in the U.S.)
- ISO 2859-1 (international standard)
These standards define how many units should be inspected from a given lot size and set thresholds for what’s considered an acceptable defect rate—known as the Acceptable Quality Limit (AQL).
For example: If your AQL for major defects is 2.5%, and inspectors find more defects than the threshold allows, the batch fails inspection. This protects you from receiving an unacceptable quantity of defective items and gives you the leverage to demand rework, replacement, or compensation.
AQL-based inspections ensure that decisions are made based on data—not guesswork or gut feeling.
Who Needs Product Inspection Services
Not all businesses operate on the same scale or in the same industry—but when it comes to quality, consistency, and compliance, the risks of skipping inspection are universal. Whether you’re sourcing goods overseas, shipping under your own brand, or selling through third-party platforms, product inspection services are a critical safeguard that help you maintain control over your supply chain.
Let’s take a closer look at the key players who rely on product inspection to protect their brand, their margins, and their reputation.
Importers and Exporters
For importers and exporters navigating the complex world of global trade, product inspection is not just a precaution—it’s an essential quality gate. When goods are produced thousands of miles away, there’s often little visibility into what’s really happening on the factory floor.
Why inspection matters for importers and exporters:
- Verifies that goods match order specifications before they leave the factory
- Reduces risk of shipping delays, costly rework, or rejected shipments
- Ensures compliance with customs, labeling, and regulatory standards
- Helps prevent container space from being wasted on defective or incorrect items
Without on-site verification, you’re flying blind—and the cost of errors can be staggering. A single rejected shipment can trigger extra tariffs, storage fees, or customer disputes that cut deep into profit margins.
Brand Owners and Retailers
Whether you’re running a boutique label or managing a multi-national retail brand, consistency is key. Customers expect the same level of quality every time they interact with your product. That’s why brand owners and retailers turn to product inspection services to ensure their brand promise isn’t compromised.
For brand managers, inspection helps:
- Maintain consistent product quality across multiple suppliers or factories
- Avoid negative reviews, returns, or customer churn due to poor craftsmanship
- Confirm packaging, labeling, and visual elements meet brand standards
- Spot design or manufacturing deviations before they reach the shelves
Amazon FBA Sellers
Selling through Amazon FBA comes with perks like Prime delivery and warehousing, but it also comes with high expectations and strict rules. If your product doesn’t meet quality or compliance standards, Amazon won’t hesitate to suspend your listing—or worse, your account.
For Amazon FBA sellers, product inspection is a no-brainer.
Here’s why it’s a must:
- Prevents poor-quality products from triggering negative reviews
- Ensures packaging and labeling meet Amazon’s specific requirements
- Verifies barcode placement, bundle accuracy, and packaging weight
- Helps sellers avoid chargebacks, suspensions, or ASIN deactivation
With Amazon’s algorithm prioritizing seller performance, even a minor spike in returns or complaints can push your listing down the rankings—or get it removed altogether. A simple pre-shipment inspection can be the difference between a best-seller and a business-ending nightmare.
Manufacturers Working With Third-Party Suppliers
Not all manufacturers produce everything in-house. Many rely on third-party suppliers, often located in different regions or countries, to fulfill parts of their production. In these cases, product inspection services act as a neutral and reliable control point to monitor external partners.
Inspection helps manufacturers:
- Ensure parts or components meet internal specs before integration
- Confirm that external suppliers follow agreed-upon production protocols
- Catch inconsistencies or shortcuts before they affect final assembly
- Manage multiple supply chain partners without losing oversight
Regardless of size, industry, or structure, one thing is clear: if you’re producing, sourcing, or selling physical goods, product inspection isn’t just optional—it’s mission-critical. It protects your investment, defends your reputation, and keeps your customers coming back.
Product inspection is not just about finding flaws—it’s about building confidence. It gives you visibility where you need it most: on the factory floor, during production, and before goods ever leave the supplier. With consistent inspection protocols in place, you can safeguard your business against costly mistakes, ensure regulatory compliance, and deliver the kind of quality your customers expect—every single time.
From small Amazon sellers to global importers and manufacturers, those who take inspection seriously are the ones who scale without compromise. They catch problems early, maintain control, and grow with peace of mind.
At ECQA, we specialize in third-party product inspection services tailored to your specific needs—whether you’re managing complex supply chains, launching a new product, or simply trying to avoid another bad batch. Our experts are your eyes on the ground, making sure what you ordered is exactly what you receive.