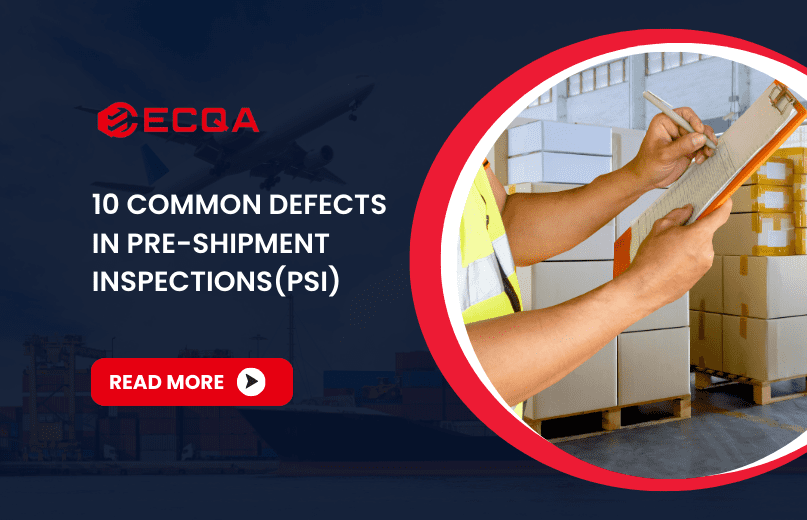
10 Common Defects in Pre-Shipment Inspections(PSI)

Pre-shipment inspections defects can lead to costly recalls, customer dissatisfaction, and damage to brand reputation. A thorough PSI process helps manufacturers and buyers detect quality issues before products reach the market, ensuring compliance with specifications and industry standards.
Without proper inspections, defects like poor assembly, missing components, and safety hazards may go unnoticed until after distribution—resulting in refunds, negative reviews, and operational setbacks. Identifying these issues early is crucial for maintaining supply chain integrity and delivering high-quality goods.
This article highlights 10 common defects found during pre-shipment inspections and provides practical strategies to prevent them from becoming costly problems.
Why Pre-Shipment Inspections Are Important
1. Avoiding Costly Product Recalls
A single defective batch of products can result in a massive recall, costing companies millions in losses—not to mention the damage to brand credibility. Take the case of a major toy manufacturer that had to recall thousands of units due to safety hazards from loose components. Had proper pre-shipment inspections been conducted, this issue could have been caught early.
2. Preventing Quality Inconsistencies
Consistency is key in manufacturing. Customers expect every unit of a product to match specifications, whether in color, size, or functionality. Without detailed PSI checks, shipments might include items with incorrect labeling, non-compliant materials, or defective parts, leading to high return rates.
3. Reducing Supplier Miscommunication
Many quality defects stem from miscommunication between buyers and suppliers. A company might request specific materials or manufacturing techniques, only to receive goods that don’t meet expectations. Regular PSI inspections help bridge this gap, ensuring factories follow agreed-upon quality standards.
4. Enhancing Compliance with International Standards
Different markets impose strict regulatory requirements for safety, durability, and environmental compliance (e.g., CE marking in Europe, FDA regulations in the U.S.). Skipping inspections means risking non-compliance penalties or import rejections, making PSI an essential step for businesses exporting to multiple regions.
5. Building Customer Trust and Satisfaction
When customers receive flawless products, they trust your brand and are more likely to become repeat buyers. Poor-quality shipments, on the other hand, lead to negative reviews, refunds, and lost market share. A robust PSI process helps brands maintain high consumer confidence by consistently delivering top-quality products.
10 Common Defects Found in Pre-Shipment Inspections (PSI)
1. Workmanship Defects (Poor Craftsmanship & Assembly Issues)
One of the most frequent issues discovered during PSI is poor workmanship. Whether it’s uneven stitching on garments, misaligned components in electronics, or rough finishing in plastic parts, subpar craftsmanship directly affects a product’s functionality and aesthetic appeal.
Examples of Workmanship Defects:
- Uneven seams or loose threads in textiles
- Gaps, cracks, or misaligned parts in assembled products
- Rough edges or burrs in plastic molding
- Inconsistent surface finishing on metals or ceramics
- Loose or improperly fastened screws in machinery and furniture
2. Color & Material Discrepancies
Imagine ordering a batch of blue corporate uniforms, only to receive them in slightly different shades of blue—or worse, in completely different colors. This is a common issue in manufacturing, where dye variations, material substitutions, or supplier errors cause inconsistencies between approved samples and final products.
Common Material & Color Issues:
- Fabric shades that don’t match across different production lots
- Plastic parts appearing more opaque or glossy than the original sample
- Metal components with different finishing (e.g., matte vs. polished)
- Substituted materials that don’t meet specifications (e.g., lower-grade plastic)
3. Functional Failures & Performance Issues
A product might look perfect, but if it doesn’t function as intended, it’s still a defective product. Functional defects range from toys that won’t light up to electrical appliances with faulty circuits. These issues are especially critical in consumer electronics, medical devices, and mechanical components.
Common Functional Issues:
- Electronic gadgets that fail power-on tests
- Misaligned or unresponsive buttons on appliances
- Wheels, hinges, or moving parts that don’t operate smoothly
- Leakage issues in liquid containers
- Weak structural integrity in load-bearing products
4. Incorrect Product Specifications
Sometimes, manufacturers produce items that don’t match the approved specifications—even if they look similar at first glance. This can include size variations, incorrect labeling, missing features, or even entirely different product models.
Common Specification Errors:
- Wrong dimensions or weight (e.g., furniture slightly larger than requested)
- Missing accessories or components (e.g., a phone without a charging cable)
- Incorrect labeling or packaging (e.g., wrong barcodes, typos in product info)
- Different product model or SKU substituted without approval
5. Poor Packaging & Inadequate Protection
Even a flawless product can arrive damaged if the packaging isn’t up to standard. Weak, poorly sealed, or improperly cushioned packaging leads to breakage, scratches, or transit damage.
Common Packaging Defects:
- Thin, flimsy cartons that collapse under pressure
- Lack of internal cushioning for fragile items
- Poorly sealed boxes, increasing risk of theft or damage
- Inconsistent labeling (wrong address, missing handling instructions)
6. Contamination & Foreign Materials
In industries like food, pharmaceuticals, textiles, and electronics, contamination is a serious quality risk. Dust, metal shavings, loose threads, oil stains, or even insects can find their way into products if factories lack proper hygiene controls.
Common Contamination Issues:
- Metal or plastic fragments in food and medical products
- Oil or chemical stains on fabrics and clothing
- Loose fibers or dust particles inside electronics
- Insect infestation due to poor storage conditions
7. Functionality & Performance Issues
A product might look perfect on the outside but fail where it matters most—its performance and functionality. Whether it’s electronics that won’t power on, zippers that won’t close, or chairs that wobble, defects in functionality can frustrate customers and lead to returns.
Common Functionality Defects:
- Electronic devices that don’t turn on or charge properly
- Mechanical failures (e.g., wheels that don’t roll smoothly, doors that don’t latch)
- Defective buttons or switches that don’t respond
- Zippers, hinges, or moving parts that jam or break easily
8. Inconsistent Colors, Finishes, and Materials
Consistency in color, texture, and material quality is critical for branding and product satisfaction. A slight shade difference in fabric or a glossy finish instead of matte might seem minor, but it can ruin a product’s aesthetic and perceived value.
Common Inconsistencies:
- Color mismatches between batches (e.g., different shades of “navy blue”)
- Uneven surface finishes (e.g., glossy in some areas, matte in others)
- Material substitutions (e.g., plastic used instead of metal)
- Variations in fabric texture or stitching patterns
9. Sharp Edges and Safety Hazards
Safety is a non-negotiable aspect of quality control, especially for children’s products, tools, and household items. Sharp edges, loose screws, or unstable structures can cause injuries, leading to product recalls and legal action.
Common Safety Hazards:
- Exposed sharp edges on metal or plastic components
- Loose screws or weak joints in furniture and machinery
- Electrical hazards (e.g., faulty wiring, overheating components)
- Toxic materials (e.g., lead in paint, non-FDA-approved plastics)
10. Incorrect Quantity & Missing Items
Receiving the wrong quantity of goods or missing items in a shipment can disrupt supply chains and lead to financial losses. Under-packed or over-packed orders often result from poor inventory management, miscommunication, or human error during packaging.
Common Quantity Issues:
- Short shipments (fewer units than ordered)
- Over-shipments (more units than ordered, causing stock imbalances)
- Missing accessories or parts (e.g., missing screws in furniture sets)
- Mislabeled bulk orders (wrong SKU or item count)
Selecting a reliable pre-shipment inspection company is crucial to avoiding costly mistakes. A trusted provider ensures compliance, product quality, and smooth supply chain operations. Learn how to make the best choice in our guide: How to Choose the Best Pre-Shipment Inspection Company.
How ECQA Can Help with Pre-Shipment Inspections (PSI)
At ECQA, we provide professional pre-shipment inspection services that ensure your products meet quality standards before they leave the factory. Companies that regularly use third-party inspection services see a 10-15% reduction in defect rates, which improves brand reputation and customer satisfaction.
Ready to safeguard your shipments? Explore our Quality Inspection Services today and ensure your products are of the highest quality before they reach your customers.