
Retail Product Inspections
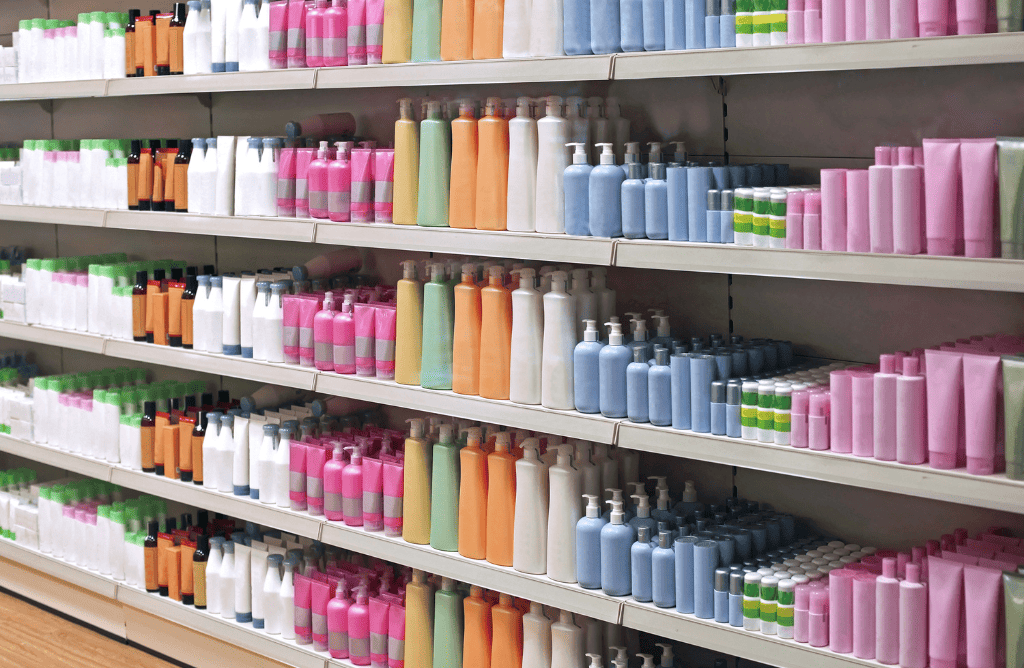
In the highly competitive world of retail, upholding the quality, safety, and compliance of your products is absolutely essential for success and brand reputation. As retailers navigate complex global sourcing networks, maintaining control over retail product standards can be a significant challenge. This is why hiring a third-party inspection service, specifically for retail product inspection, is a critical step to ensure robust quality control and mitigate the risks associated with supply chain inconsistencies.
At ECQA, we offer a comprehensive range of retail product inspections tailored to meet diverse needs, from ensuring the safety and quality of beauty products to essential baby supplies. We have successfully partnered with numerous leading brands and their global suppliers.
Our team of experienced retail product inspectors and auditors are strategically positioned worldwide, ready to monitor your entire manufacturing process, from initial production to final shipment. We proactively identify and address potential quality issues at the source, ensuring your retail products not only meet but exceed your precise specifications and, ultimately, delight your customers while ensuring full regulatory compliance.
Why Retail Product Inspections Matter
Retail product inspections serve as a critical safeguard, helping businesses mitigate risks and uphold their brand reputation.
Ensuring Compliance with Global Standards
Regulatory requirements vary across different markets, and non-compliance can lead to costly penalties or even product recalls. Third-party retail product inspections ensure that your products meet the safety, quality, and labeling regulations required by international standards such as:
- ISO (International Organization for Standardization) – General quality management and safety standards
- CPSC (Consumer Product Safety Commission) – U.S. consumer product safety requirements
- CE Marking – European safety compliance for retail goods
- ASTM (American Society for Testing and Materials) – Industry-specific product testing standards
- FDA (Food and Drug Administration) – Compliance for food, cosmetics, and medical-related retail items
By conducting inspections at various production stages, you can prevent compliance issues before they escalate, ensuring seamless market entry for your products.
Minimizing Defects and Inconsistencies
Product defects not only lead to financial losses but also damage customer trust. Without a structured inspection process, retailers risk receiving shipments with:
- Defective workmanship – Misaligned stitching, faulty assembly, or poor finishing
- Incorrect specifications – Size deviations, incorrect colors, or material substitutions
- Functional issues – Non-working electronic components or unstable structures
- Packaging flaws – Damaged, misprinted, or non-compliant labeling
Through systematic quality checks, third-party inspections identify these issues early in the production cycle, reducing the chances of defective products reaching store shelves.
Strengthening Brand Trust and Customer Loyalty
Quality issues can quickly erode consumer confidence, leading to negative reviews, product returns, and a decline in sales. In contrast, consistently high-quality products enhance brand loyalty and encourage repeat purchases. By investing in retail product inspections, businesses demonstrate their commitment to delivering superior products that meet customer expectations.
Additionally, many major retailers and e-commerce platforms require suppliers to adhere to strict quality standards. Implementing third-party inspections not only strengthens your brand credibility but also opens doors to premium retail partnerships.
Reducing Supply Chain Disruptions
Production delays, shipment rejections, and last-minute quality corrections can significantly impact a retailer’s supply chain. Inspections at critical stages—pre-production, during production, and pre-shipment—help detect potential issues early, preventing costly disruptions.
- Supplier Audits ensure that the manufacturer has the capability to meet your quality standards.
- Inline Inspections allow for real-time quality control, reducing rework and delays.
- Pre-Shipment Inspections provide a final assurance before goods leave the factory.
By integrating inspections into your supply chain strategy, you can maintain a smooth, efficient, and predictable production process, avoiding delays that could impact retail operations.
How to Develop a Quality Assurance Checklist for Retail Stores
Ensuring product quality and compliance is crucial for retailers looking to maintain consumer trust and meet regulatory requirements. A structured quality assurance checklist plays a key role in this process, helping retailers systematically evaluate product quality, labeling accuracy, and safety compliance.
For a detailed guide on creating an effective checklist, read How to Develop a Quality Assurance Checklist for Retail Stores to enhance your inspection process and ensure consistent quality control.
ECQA Range of Retail Product Inspections Services:
We offer an extensive suite of services designed to address the unique needs of the retail industry:
Supplier Audit
Our experienced retail product inspector will verify company information, licenses, workforce capabilities, and production processes to ensure product quality and identify improvement opportunities for buyers and factories, especially before a first-time production run at a new facility. This service is particularly crucial before a first-time production run at a new facility, reducing risk and ensuring a reliable supply chain for your retail goods.
Pre-Production Inspections
Before production commences, we thoroughly assess all materials, production lines, and crucial documentation to identify and address any potential issues. This proactive measure ensures a smooth and efficient sourcing and production journey for our clients, minimizing costly defects that could negatively impact your retail sales and erode customer trust. This inspection will ensure you are getting exactly what you paid for from your supplier.
During Production (Inline) Inspections
Our team monitors the manufacturing process in real-time, identifying and immediately rectifying any deviations from predefined quality parameters. This service ensures consistent retail product quality throughout the entire production run, guaranteeing retail readiness and reducing the risk of recalls and defects. This inline quality control ensures efficiency.
Pre shipment Inspections
Prior to shipment, we conduct comprehensive retail product inspections, aligned with internationally recognized standards, ensuring your products fully meet retail specifications and customer expectations regarding quantity, workmanship, functionality, color accuracy, size conformity, and packaging integrity. This provides a final check for your products prior to them hitting the shelves.
Loading Supervision
We provide comprehensive loading supervision to ensure that only inspected and approved products are loaded and shipped to your retail stores or distribution centers. Our inspectors meticulously monitor every step of the process, including quantity verification, packaging integrity, container conditions, and proper handling procedures, to minimize the risk of damage, contamination, or misplacement. By implementing strict quality control measures during loading, we help safeguard your supply chain, ensuring that your goods arrive in optimal condition and meet regulatory standards.
Social Audit
We evaluate your manufacturing partners for business risks, capacity, capabilities, workplace conditions, product quality, safety, security, and environmental sustainability. This comprehensive assessment provides a clear picture of your product pipeline’s strengths and weaknesses, enabling you to make informed decisions.
By partnering with ECQA, you gain a dedicated ally committed to safeguarding your brand’s reputation and ensuring the success of your products in the global marketplace. Our global team of experts, customizable retail product inspections solutions, and commitment to quality make us the ideal partner for retailers seeking to build a resilient, transparent, and successful product pipeline. Contact us today to discover how we can help elevate your retail business to new heights.
FAQ About Retail Product Quality Inspections
1. How does ECQA ensure the quality of your inspections?
Our team of retail product inspectors are highly trained experts with extensive experience in quality control and specific industry standards. We adhere to internationally recognized standards, use rigorous testing protocols, and provide transparent reporting with detailed findings. Our commitment to accuracy and thoroughness ensures you receive reliable and actionable results.
2. How quickly can ECQA perform inspections?
Our global network of inspectors enables us to conduct inspections efficiently and within your desired timeframe. The exact turnaround time depends on the scope of the inspection and your specific requirements. Contact us today to discuss your project details and we’ll provide a precise timeline.
3. What Industries do you work with?
ECQA has a broad range of experience across diverse retail industries, including, but not limited to: Apparel & Textiles, Toys & Children’s Products, Consumer Electronics, Cosmetics & Beauty Products, Footwear, Home Goods & Furnishings, Food and other Consumer Packaged Goods (CPG) and many more. Our expertise allows us to adapt our inspection services to the specific demands of each industry.
4. What are the key benefits of Pre-Production Inspections (PPI)?
Pre-Production Inspections are crucial for preventing potential quality problems before mass production begins. These inspections allow us to identify and rectify issues with raw materials, production setup, and documentation early on. This not only saves you valuable time and money but also reduces the risk of costly defects later on in the production cycle.
5. How do During Production Inspections (DPI) help maintain consistent product quality?
During Production Inspections (also known as Inline Inspections) allow us to monitor the manufacturing process in real-time. By identifying and addressing deviations from quality parameters as they occur, we can prevent entire batches of products from becoming defective. This ensures consistent quality throughout your production run, helping to protect your brand and reduce the risk of returns or customer complaints.
6. How does ECQA’s Pre-Shipment Inspection (PSI) process work?
Our Pre-Shipment Inspections are designed to provide you with a final quality check before your products leave the factory. We will conduct a comprehensive assessment of your products, covering key areas such as quantity, workmanship, functionality, color, size, packaging, and other specifications based on internationally recognized standards. A detailed report is then provided, including pictures, so you can make an informed decision on whether to ship your products.
7. What is the purpose of a Social Audit for my retail manufacturing partners?
Social Audits play a vital role in ensuring ethical and responsible sourcing. These assessments evaluate your manufacturing partners based on various criteria, such as working conditions, safety protocols, environmental sustainability, and labor practices. This helps you reduce your risks and align your practices with your company’s values and regulatory requirements, building trust among your customers and suppliers.
8. Can ECQA tailor retail product inspection services to my specific needs?
Absolutely. We understand that each business is unique, and your product inspection needs might vary. We work closely with our clients to customize inspection protocols, reporting, and timelines to align with their specific requirements and ensure you get the results that you need.
9. What kind of reporting do you provide after inspections?
We provide comprehensive and easy-to-understand reports after each inspection. These reports typically include detailed findings, photos, pass/fail information, and recommendations. We can also create custom reports tailored to your specific requirements. You will receive this within 24 hours after the inspection has been completed.
10. What is the benefit of Loading Supervision?
Loading supervision provides an added layer of security to your supply chain. Our inspectors will make sure that the inspected, passed and approved goods are loaded into the container.
11. How can I get started with ECQA’s retail product inspection services?
Getting started with ECQA is easy. Simply contact us today through our website form, phone, or email. We’ll discuss your needs, answer your questions, and provide you with a customized quote. We’re here to help make your products the best they can be.
Leave a Comment