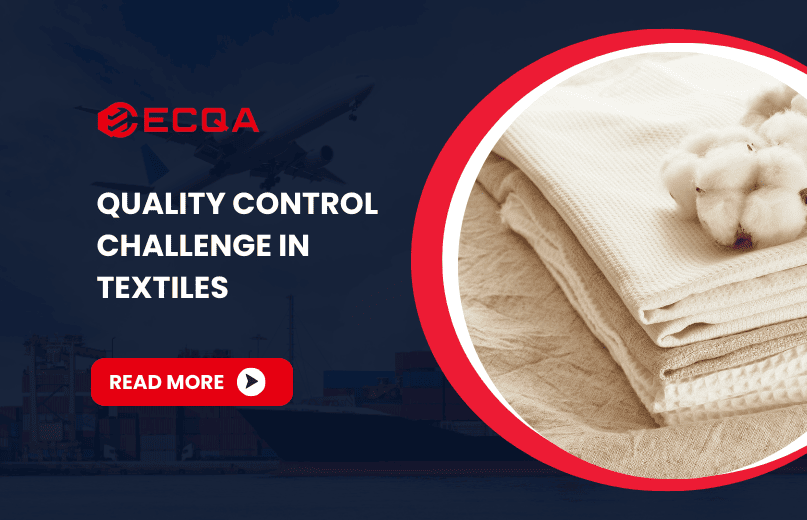
Quality Control Challenge in Textiles
Quality assurance in the textile industry remains a critical factor in product success. Despite rigorous manufacturing controls and industry standards, common quality issues persist, affecting product performance and brand reputation. According to recent industry reports, nearly 30% of textile products face quality-related challenges that lead to returns and customer complaints.
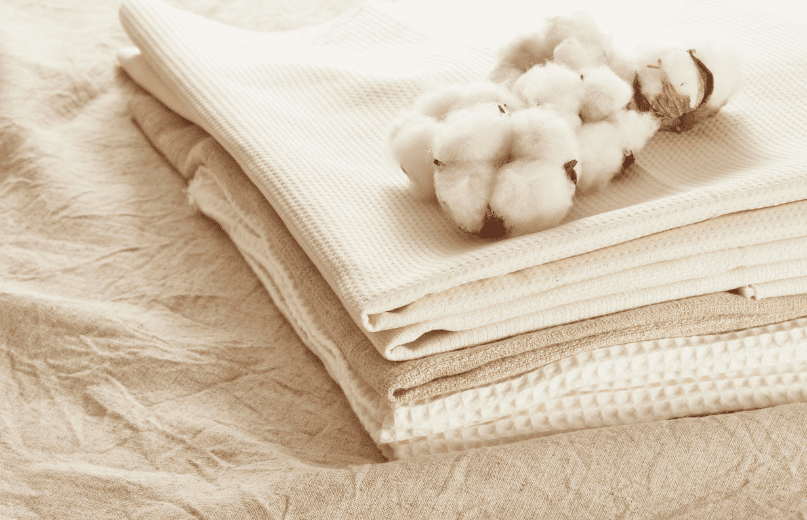
This article delves into the most frequent textile quality issues. By addressing these challenges early, manufacturers can ensure better product performance and customer satisfaction. For additional insights into ensuring consistent quality, check out our article on Home Textiles Quality Control for more strategies and best practices.
1. Fabric Shrinkage After Washing
One of the most common and frustrating complaints in home textiles is fabric shrinkage. This issue typically arises when fabrics contract after washing, leading to a product that no longer fits as expected. Shrinkage can occur in nearly all textile products, but it’s particularly problematic in high-stress areas like bed linens, towels, and clothing.
Root Causes:
- Improper Fiber Treatment: Many textiles, especially cotton, require specific pre-shrinking processes to ensure they don’t shrink excessively after their first wash. Without proper pre-treatment, fibers may contract unpredictably once exposed to moisture and heat.
- Excessive Heat During Laundering: Excessive temperatures during washing and drying can cause fibers to tighten. This is especially the case with natural fibers like cotton and wool, which are highly sensitive to heat.
- Low-Quality Synthetic Blends: Some manufacturers use synthetic blends with poor dimensional stability. These fibers may not behave consistently in different environmental conditions, leading to shrinkage or stretching.
2. Color Fading and Dye Bleeding
Color fading and dye bleeding are some of the most noticeable and disappointing issues in home textiles. When a fabric loses its vibrancy or the dye runs, it can render a product unsellable, damaging both the item’s appearance and the brand’s reputation.
Root Causes:
- Use of Substandard Dyes: Some manufacturers opt for lower-cost dyes that aren’t formulated to withstand repeated washes, light exposure, or friction. These dyes may begin to fade or leach out over time, especially when exposed to detergents or sunlight.
- Improper Dyeing Techniques: Inadequate dye application or poor-quality dyeing techniques can result in uneven color retention or color bleeding during washing. Failing to bind dyes to fibers properly can lead to issues, especially with products that experience frequent washing, such as bed sheets or towels.
- Overexposure to UV Light or Harsh Chemicals: Ultraviolet (UV) light from sunlight or exposure to harsh detergents can significantly degrade dye particles, leading to color fading. Fabrics exposed to these elements may lose their richness and vibrancy faster than expected.
3. Weak Seams and Stitching Defects
Seams are the structural backbone of most textile products. Weak seams, poorly executed stitching, or unraveling can drastically reduce the durability of home textiles, leading to high rates of product returns, warranty claims, and poor customer reviews.
Root Causes:
- Low-Quality Threads: Poor-quality threads or low-tensile-strength fibers may not hold up under the tension of regular use or washing, leading to seam breakdown or unraveling.
- Incorrect Stitch Density: If the stitch density is too sparse, it can result in loose stitches, which are more likely to break or cause fabric to pull apart. Alternatively, too much stitch density can stress the fabric, causing distortion or puckering.
- Excessive Tension During Sewing: Applying too much tension to fabric during the sewing process can cause distortions along the seam, which may lead to premature wear or breakage under stress.
4. Pilling and Surface Abrasion
Pilling is one of the most frustrating quality issues for consumers. It occurs when fibers break free from the fabric surface and form small, unsightly balls of fuzz. This issue not only impacts the aesthetic appeal of textiles but also affects the comfort and durability of the product.
Root Causes:
- Cheap Synthetic Fibers: Many lower-quality home textiles are made from short-staple synthetic fibers, such as polyester or nylon, which are more prone to pilling due to their inherent brittleness.
- Repeated Friction: Products like cushion covers, blankets, and upholstered furniture experience repeated friction, causing fibers to break and form pills over time. Laundering can exacerbate this effect, especially in tumble dryers.
- Inadequate Finishing Processes: Some textiles don’t undergo proper fiber stabilization or finishing processes to prevent pilling. These processes help smooth fibers and prevent them from catching and breaking.
5. Chemical Residues and Skin Irritation
Chemical residues in textiles are a growing concern, particularly when it comes to items like bedding, clothing, and children’s products. These residues, often left over from manufacturing processes, can trigger allergic reactions or skin irritations in sensitive individuals.
Root Causes:
- Formaldehyde-Based Finishes: Formaldehyde is commonly used in textiles for wrinkle resistance. However, its overuse can leave harmful residues that may irritate the skin or cause respiratory issues.
- Contamination with Hazardous Dyes: Some textiles may be contaminated with azo dyes, heavy metals, or residual pesticides that are harmful to human health.
- Inadequate Rinsing: Poor rinsing during the manufacturing process can leave behind detergent or other chemical traces, which can accumulate over time, causing skin reactions, especially in sensitive individuals or infants.
6. Inconsistent Fabric Density and GSM Fluctuations
Fabric density and grams per square meter (GSM) are critical measurements that directly affect the weight, feel, and performance of home textiles. Inconsistent GSM can lead to significant discrepancies in product quality, especially for high-end items like towels, bed linens, and upholstery fabrics.
Root Causes:
- Machinery Miscalibration: Textile manufacturing machines require precise calibration to maintain consistent GSM throughout production. Variations in machine settings or failure to check calibration regularly can result in inconsistent fabric weight.
- Raw Material Inconsistency: Different batches of raw materials, such as cotton or synthetic fibers, may have slight variations in density or fiber length, leading to discrepancies in final product weight and texture.
- Incorrect Weft/Warp Tension: If tension is too loose or too tight in the weaving process, fabric density can fluctuate across a single roll, leading to uneven quality in finished products.
7. Odor Retention in Synthetic Blends
Odor retention, particularly in synthetic blends like polyester, is a growing concern for textiles that come into direct contact with the skin. Synthetic fabrics can trap moisture and bacteria, causing fabrics to hold onto unpleasant odors even after washing, leading to poor customer satisfaction.
Root Causes:
- Poor Antimicrobial Treatment: Some synthetic fibers lack antimicrobial finishes that can help inhibit the growth of bacteria, mold, and mildew, which are often the culprits behind odor retention.
- Tight Weave or Low Air Permeability: Fabrics that don’t breathe well can trap moisture, creating a damp environment conducive to odor buildup. Products like athletic wear and upholstered furniture are particularly susceptible to this issue.
- Residual Oils and Sweat: Synthetic fibers can also hold onto body oils and sweat, which can lead to persistent odors even after laundering.
8. Sustainability & Traceability in Textile Quality
As consumers grow more conscious of the environmental impact of their purchases, sustainability and ethical sourcing have become key drivers of purchasing decisions in the home textile industry. However, sustainability isn’t just about materials; it also encompasses manufacturing practices, waste management, and supply chain transparency.
Root Causes:
- Lack of Fiber Traceability: Many textile products don’t provide clear traceability regarding where the fibers were sourced, whether they are organic, or whether sustainable practices were employed in the production.
- Limited Eco-Friendly Certifications: While some companies claim to use eco-friendly processes, a lack of verified certifications like Global Organic Textile Standard (GOTS) or Fair Trade means that claims are often unverified. Check out our article on the 7 Key Textile Sustainability Certifications.
- Resource-Intensive Manufacturing: Traditional textile manufacturing is often resource-intensive, consuming large amounts of water and energy, leading to a higher carbon footprint and negative environmental impacts.
Addressing common quality issues before products hit the market is not just about meeting regulatory standards; it’s also about protecting brand reputation, building customer loyalty, and ensuring sustainability in an increasingly competitive marketplace. Proactive quality assurance goes beyond compliance—it’s about delivering consistently excellent products that meet evolving consumer expectations for durability, safety, and ethical sourcing.
If you’d like to book a textile inspection or discuss how we can help optimize your textile quality, ECQA can help! Email us today at sales@ecqa.com