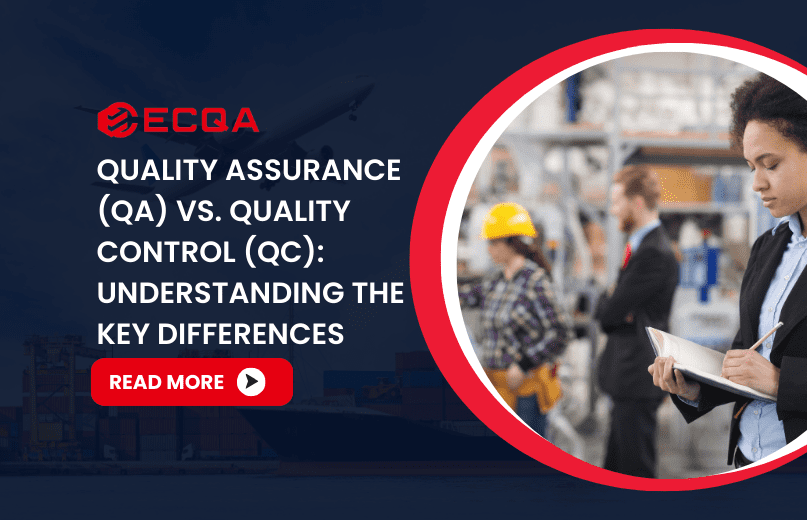
Quality Assurance (QA) vs. Quality Control (QC): Understanding the Key Differences
The terms Quality Assurance (QA) and Quality Control (QC) are often used interchangeably, but they serve distinct roles in the quality management system. Understanding the difference between Quality Assurance and Quality Control is essential for businesses aiming to meet industry standards, comply with regulations, and enhance customer satisfaction.
Whether you’re working in manufacturing, software development, healthcare, or service industries, both QA and QC are fundamental components of quality management systems that help prevent defects, improve performance, and maintain consistent product or service standards. While Quality Assurance focuses on process-oriented activities that ensure a quality product is being produced, Quality Control is more concerned with product-oriented activities that verify whether a product meets the defined standards.
Both QA and QC play crucial roles in optimizing efficiency and minimizing defects, but they do so in different ways. In this article, we will delve into the key differences, the importance of both practices, and how businesses can effectively integrate them to enhance their overall quality. By the end of this article, you will gain a comprehensive understanding of Quality Assurance vs. Quality Control and how these two elements can work together to help your company thrive in a highly competitive market.
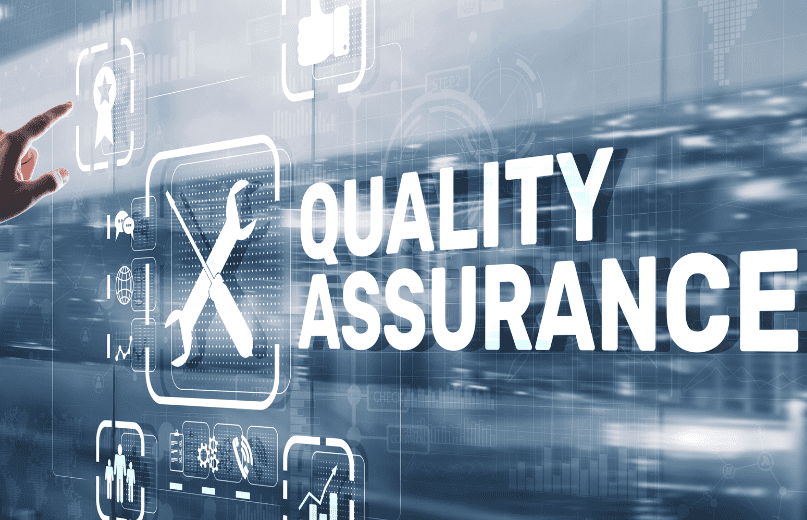
What is Quality Assurance (QA)
Quality Assurance (QA) refers to the systematic process of ensuring that a product or service meets specific standards of quality before it reaches the customer. Rather than focusing on identifying defects in the final product, QA is proactive. Its primary goal is to improve and stabilize production and development processes to prevent issues before they arise. By implementing a consistent approach to managing processes and continuous improvement, QA ensures that all activities are aligned with the goal of delivering high-quality outcomes.
The Role of QA in Process Management
The main function of QA is to create and maintain procedures that lead to the desired outcomes, regardless of the production scale. This is achieved by developing standards, guidelines, and best practices that guide the team through every step of production or service delivery. This includes documenting processes, training staff, and regularly auditing the processes to ensure compliance with established guidelines.
For example, in software development, QA involves testing the development process itself, making sure that coding standards, project management techniques, and communication protocols are in place and followed throughout the lifecycle. The goal is to ensure that the product can be built efficiently and with minimal defects.
Key QA Activities and Strategies
Some of the core QA activities include:
- Process audits to ensure that procedures and standards are followed
- Training employees to consistently follow quality processes
- Standard Operating Procedures (SOPs) for every phase of production or service
- Continuous process improvement through tools like Six Sigma or Lean Manufacturing
- Prevention-focused planning that identifies and mitigates risks at every stage
- Root cause analysis to address process inefficiencies
The Focus on Prevention in QA
Quality Assurance’s central philosophy is prevention. Rather than waiting for a defect to be found in the product, QA aims to eliminate errors before they occur. By focusing on improving the processes and techniques used in product development or service delivery, businesses can save time and resources, reduce waste, and minimize the potential for costly errors.
For instance, a QA team may examine the materials used in manufacturing or the software development framework to ensure that they are of the highest standard. They also evaluate supplier quality and monitor internal workflows to prevent issues from arising during production.
Benefits of Implementing QA
By establishing a robust Quality Assurance system, businesses can enjoy a wide range of benefits, including:
- Reduced costs due to fewer defects and recalls
- Increased customer satisfaction because of higher-quality products and services
- Faster time-to-market as more efficient processes lead to quicker product releases
- Enhanced reputation in the marketplace
- Regulatory compliance with industry standards and certifications
Examples of QA Practices in Various Industries
Quality Assurance practices are tailored to meet the specific needs of different industries. In manufacturing, QA may include comprehensive inspections of raw materials and the use of statistical process controls to ensure products meet predefined specifications. In software development, QA involves rigorous testing procedures such as unit testing, integration testing, and regression testing to ensure the product functions as expected across various environments. Similarly, in healthcare, QA procedures ensure that patient care processes follow the necessary protocols to maintain safety and effectiveness.

What is Quality Control (QC)
While Quality Assurance (QA) focuses on improving processes to prevent defects, Quality Control (QC) is centered around identifying and correcting defects in the final product. QC is a reactive process that ensures that the output of a particular system, process, or service meets the predefined quality standards. Essentially, QC inspects the quality of the finished product and ensures that any deviations from quality standards are addressed before the product is delivered to the customer.
The Role of QC in Product Testing and Inspections
Quality Control’s primary function is to detect any defects or inconsistencies that may have occurred during the production or service delivery phase. This involves rigorous inspection, testing, and evaluation to ensure that the final product aligns with the required specifications and standards.
QC often employs various tools and techniques such as statistical sampling, visual inspection, performance testing, and product verification. In manufacturing, for example, QC inspectors may measure a product’s dimensions or check the final assembly for defects. In software, QC might involve bug tracking systems to identify and fix any issues in the code.
Key QC Activities and Techniques
Key QC activities typically include:
- Final product inspections to ensure specifications are met
- Testing for defects in various aspects such as performance, durability, and reliability
- Use of control charts to monitor quality over time
- Statistical sampling techniques to identify potential defects in batch production
- Verification and validation to ensure the product meets customer expectations
- Calibration of instruments and equipment used in production to ensure accuracy
The Focus on Detection in QC
Quality Control is reactive because it focuses on detecting defects in the final product. When QC identifies any inconsistencies, corrective measures are taken to fix the issue. For instance, if a defect is discovered during the inspection phase of a manufacturing process, QC might halt production to address the problem, repair faulty equipment, or reject substandard materials.
QC is crucial for ensuring that customers receive a product that meets their expectations. It ensures the product’s quality, whether it’s in terms of functionality, aesthetic standards, or performance.
Benefits of Implementing QC
Effective Quality Control practices provide several key benefits:
- Ensuring consistency of product quality over time
- Early detection of defects, reducing the risk of customer complaints or recalls
- Maintaining high standards in line with industry regulations and customer expectations
- Boosting brand credibility by consistently delivering reliable products
- Reducing waste and rework by catching problems before they escalate
Examples of QC Practices Across Industries
In the automobile industry, QC may involve end-of-line inspections, where vehicles are checked for defects such as improper fitting or paint discrepancies.
In electronics manufacturing, QC might include testing the functionality of components and ensuring that they meet electrical standards.
In the pharmaceutical industry, QC ensures that the drugs are produced under stringent conditions and meet all regulatory guidelines before they are shipped out.
Key Differences Between Quality Assurance and Quality Control
While QA and QC have different focuses and approaches, they are interrelated and complementary.These differences impact how each practice is applied in different industries and how they contribute to a business’s overall quality management strategy. Understanding these distinctions is crucial for selecting the right approach for your organization.
Focus and Objectives
The primary distinction between QA and QC lies in their focus and objectives. Quality Assurance is a preventive approach that focuses on improving and establishing processes to ensure quality from the start. It is process-oriented, aiming to eliminate issues before they occur by setting up effective procedures, monitoring, and controlling how products are created or services are delivered.
On the other hand, Quality Control is product-oriented, focusing on identifying defects or issues in the final product. QC’s goal is to ensure that the finished product meets the required quality standards and functions as expected. Therefore, while QA ensures that the right processes are in place, QC verifies that the right products are produced.
Process vs. Product
Another key difference between QA and QC is that QA focuses on process management, while QC is concerned with product testing and validation. QA sets the stage for quality by defining standard operating procedures (SOPs), training staff, and ensuring consistency throughout the production or service delivery process. QC, in contrast, involves inspecting and testing the finished products or outcomes to ensure they meet predefined criteria.
In essence, QA’s role is to create the systems that ensure products will be made correctly, while QC’s role is to test the products and confirm they are up to standard.
Preventive vs. Corrective Measures
QA is inherently preventive, as it focuses on eliminating potential problems in the process before they can affect the final product. This is achieved through proper planning, training, and ongoing monitoring to ensure adherence to quality protocols.
QC, however, is more corrective in nature. When QC detects issues in the final product, the team addresses them by either correcting the defect or removing the faulty items from production. Detection and correction are the cornerstones of QC.
Tools and Techniques Used
QA and QC rely on different tools and techniques to fulfill their objectives. Some common QA tools include:
- Process maps to visualize workflows
- Risk analysis to predict potential issues
- Root cause analysis to identify systemic issues
- Training programs for team members
In contrast, QC tools are more product-focused, such as:
- Statistical process control (SPC) to monitor production consistency
- Sampling techniques to evaluate product quality
- Inspection checklists to ensure product specifications are met
Scope and Application in Various Industries
Both QA and QC are applicable across various industries, but their specific use cases vary. In manufacturing, QA ensures that production processes follow standards, while QC inspects the final products for defects. In software development, QA may involve continuous integration practices and coding standards, while QC involves testing phases such as unit testing and system testing to catch defects before release.
Why Both QA and QC Are Essential for Business Success
While QA and QC have distinct functions, both are essential for a business’s success in ensuring high-quality products and services. When implemented together, these practices work synergistically to minimize defects, reduce costs, and enhance customer satisfaction.
How QA and QC Complement Each Other
The relationship between QA and QC is complementary rather than competitive. While QA focuses on creating and managing the processes to ensure high quality, QC tests the products to verify that they meet the expected standards. By combining both, businesses can ensure that their products not only meet industry regulations but also satisfy customer expectations.
For example, in the automotive industry, QA ensures that the manufacturing processes are controlled and standardized, while QC inspects each vehicle for defects before it leaves the assembly line. This integration ensures that both the process and the end product are aligned with quality standards.
Impact of QA and QC on Customer Satisfaction and Brand Reputation
The effectiveness of QA and QC directly impacts a company’s reputation. A company that consistently delivers high-quality products or services is more likely to retain customers, attract new business, and build a strong brand reputation. Moreover, customers who experience consistent quality are more likely to recommend the business to others.
By adopting both QA and QC practices, businesses can ensure that they consistently deliver quality, meet customer expectations, and maintain brand loyalty.
Common Challenges in Quality Assurance and Quality Control
Despite their importance, Quality Assurance (QA) and Quality Control (QC) face numerous challenges that can hinder their effectiveness. Understanding these challenges allows businesses to be better prepared and develop solutions that enhance their quality management processes.
1. Lack of Clear Communication and Coordination
One of the most common challenges faced by organizations is the lack of communication between QA and QC teams. Without effective communication, there is often confusion regarding quality standards, procedures, and expectations, leading to inefficiencies or errors.
- Solution: Establish a collaborative environment where both teams are involved in the planning and execution of quality protocols. Frequent meetings, cross-departmental training, and shared platforms can improve communication.
2. Resistance to Change
Employees may resist new processes or systems, particularly if they feel that current practices are sufficient or fear the added workload of new standards. This resistance can delay the adoption of QA and QC practices or cause them to be ineffective.
- Solution: Leadership should actively communicate the benefits of quality initiatives and involve employees at every level. Offering incentives, providing training, and explaining how QA and QC contribute to business success can help overcome resistance.
3. Inadequate Resources
Implementing QA and QC effectively requires adequate resources, including time, personnel, and technology. A lack of investment in these areas can lead to poor quality practices or overlooked defects.
- Solution: Ensure that the organization allocates sufficient resources to quality management. This includes hiring skilled personnel, acquiring the necessary tools, and investing in technology that facilitates efficient quality management.
4. Inconsistent Application of Quality Standards
In many organizations, quality standards may be inconsistently applied across different departments, teams, or regions. This leads to variability in product quality, which can harm brand reputation and customer satisfaction.
- Solution: Develop standard operating procedures (SOPs) and enforce consistent application of these standards across the organization. Regular audits and performance reviews can ensure that standards are consistently applied.
5. Overlooking the Role of Data and Analytics
Many organizations fail to leverage data and analytics in their quality management processes. Data can provide insights into process performance, customer feedback, and product defects, but without it, businesses may struggle to identify improvement areas.
- Solution: Use data-driven tools and techniques such as lean manufacturing, Six Sigma, or Total Quality Management (TQM) to identify inefficiencies, defects, and areas for improvement in both QA and QC processes.
In summary, while Quality Assurance (QA) and Quality Control (QC) serve different purposes within a quality management system, both are equally important in ensuring the delivery of high-quality products and services. QA focuses on the prevention of defects, creating processes and standards that help avoid issues before they arise, while QC deals with identifying defects in finished products, ensuring that they meet the required specifications before reaching the customer.
For businesses seeking to maintain a competitive edge, the integration of both QA and QC processes is vital. Quality Assurance lays the foundation for smooth operations, reducing errors in the long term, whereas Quality Control acts as the final checkpoint, ensuring consistency and customer satisfaction. When implemented together, these systems not only prevent waste but also enhance customer loyalty, and ultimately contribute to long-term business success.
By adopting and refining these complementary practices, organizations can improve operational efficiency, reduce costs, and achieve superior quality standards, resulting in a stronger market presence and better customer trust.
At ECQA, we recognise how essential Quality Assurance and Quality Control are to achieving excellence in the supply chain. Our third-party inspection services cover a broad spectrum of QA and QC tasks, such as inspections, testing, audits, and certification. By working with us, you can tap into our expertise and global capabilities, ensuring your products meet the highest quality standards, reduce risks, and support sustainable success
Frequently Asked Questions about Quality Assurance and Quality Control.
1. What is the difference between Quality Assurance and Quality Control?
Quality Assurance (QA) is focused on preventing defects by improving processes and ensuring they meet specific standards. Quality Control (QC), on the other hand, involves inspecting and testing products after production to identify defects and ensure they meet quality specifications.
2. Why is Quality Assurance important for businesses?
Quality Assurance is important because it helps prevent defects in products or services by focusing on improving processes and creating a structured framework. It leads to fewer errors, reduced waste, and improved overall efficiency, benefiting the business in the long term.
3. How does Quality Control help ensure product quality?
Quality Control ensures that products meet predefined standards by testing, inspecting, and measuring them before they reach the customer. It identifies defects and prevents subpar products from being delivered, thereby maintaining high-quality standards and customer satisfaction.
4. Can Quality Assurance and Quality Control work together?
Yes, Quality Assurance and Quality Control complement each other. While QA ensures that processes are optimized to prevent defects, QC acts as a final checkpoint to identify and correct defects before the product is shipped. When integrated, they ensure both process reliability and product quality.
5. Which is more important: Quality Assurance or Quality Control?
Both QA and QC are essential to maintaining product quality. QA focuses on preventing defects before they happen, while QC ensures that the final product meets quality standards. Businesses should implement both for a well-rounded approach to quality management
6. How does Quality Assurance help in process improvement?
Quality Assurance involves creating systems, processes, and standards that focus on prevention. By continuously evaluating and improving processes, QA helps reduce errors, streamline production, and create more efficient workflows, leading to higher quality outcomes.
7. How does Quality Control impact customer satisfaction?
Quality Control directly impacts customer satisfaction by ensuring that only products meeting quality standards are delivered. By identifying and eliminating defects, QC ensures that customers receive reliable and functional products, leading to increased trust and satisfaction.
8. Are Quality Assurance and Quality Control the same in every industry?
No, while the principles of QA and QC are consistent, their application may vary depending on the industry. For example, in manufacturing, QC may involve physical testing of products, while in software development, QC might include bug testing. However, both are vital across all sectors
9. How can a company integrate Quality Assurance and Quality Control?
A company can integrate QA and QC by aligning both practices within a unified quality management system. QA should focus on continuous process improvement, while QC should verify that the final products adhere to established quality standards. Regular audits and training programs can ensure their effective integration.
10. What are the long-term benefits of investing in Quality Assurance and Quality Control?
Investing in both QA and QC leads to long-term benefits such as cost savings, improved customer loyalty, reduced waste, and enhanced operational efficiency. Companies that implement both practices tend to have more consistent product quality, stronger reputations, and a competitive advantage in the market