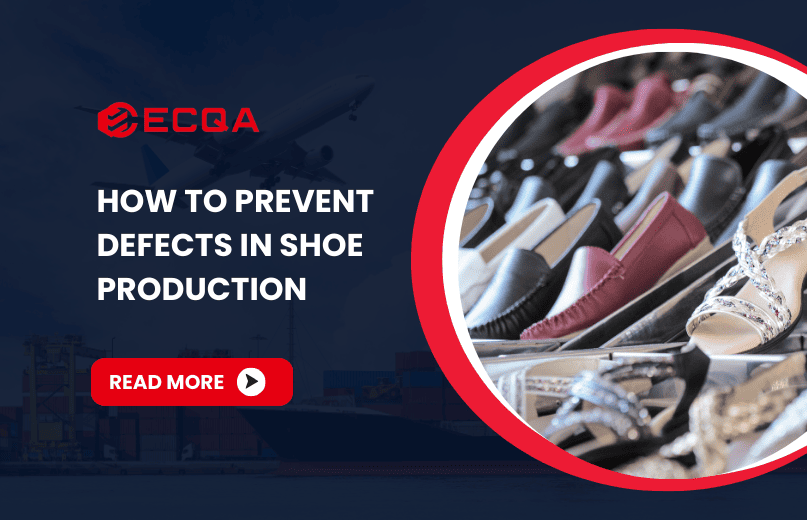
How to Prevent Defects in Shoe Production
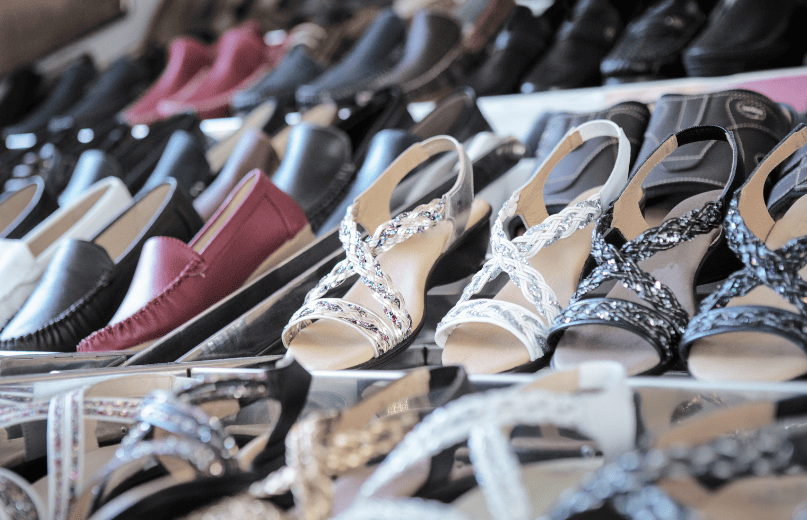
Footwear manufacturers face numerous challenges in producing high-quality shoes that meet stringent industry standards. Even minor defects—such as improper stitching, weak adhesives, or material inconsistencies—can compromise product durability and customer satisfaction. Beyond financial losses, defective shoes can erode consumer confidence and harm a brand’s long-term success.
Shoe defect prevention plays a critical role in minimizing product returns, rework costs, and quality-related complaints, all of which can impact a company’s bottom line.
By implementing rigorous quality control measures, lean manufacturing techniques, and advanced inspection processes, manufacturers can significantly reduce defects, enhance product longevity, and optimize production efficiency. This article will examine the most common shoe defects, their root causes, and effective defect prevention strategies to help manufacturers maintain exceptional quality standards in shoe production.
Common Shoe Defects and Their Causes
Understanding the most frequent defects in footwear production is the first step toward preventing quality issues. Defects can arise due to poor material selection, improper manufacturing techniques, or inadequate quality inspections. Below are the most prevalent shoe defects and their root causes:
Upper Material Defects
- Wrinkles and Creases: Occur due to improper handling and storage of raw materials.
- Color Inconsistencies: Result from dyeing process issues or batch variations.
- Weak Bonding: Happens when adhesives fail to adhere properly, leading to material separation.
- Material Tears: Caused by low-quality fabric or excessive stretching during production.
Sole Defects
- Detachment of Sole: Often due to poor adhesive application or insufficient curing time.
- Air Bubbles in the Sole: Occur when air gets trapped during molding, affecting durability.
- Uneven Thickness: Results from inconsistencies in material flow during manufacturing.
- Weak Durability: Arises when subpar rubber or polyurethane is used.
Stitching Issues
- Loose Threads: Indicate poor-quality stitching or improper thread tension.
- Skipped Stitches: Happen due to faulty sewing machines or untrained labor.
- Misaligned Stitching: A result of manual errors or inconsistent sewing guides.
Adhesion Problems
- Weak Glue Application: Leads to peeling soles or upper separation.
- Peeling Sole Layers: Caused by incorrect bonding methods or poor-quality adhesives.
Structural Defects
- Incorrect Shoe Shape: Results from errors in mold design or assembly mistakes.
- Improper Sizing: Occurs due to inconsistencies in cutting patterns.
- Misaligned Components: Develop due to inaccurate assembly or production line misalignment.
Identifying and addressing these common defects early in production is essential to maintain consistent footwear quality and reduce costly rework.
Key Factors in Preventing Shoe Defects
Manufacturers must take proactive steps to prevent defects at every stage of production. This includes material selection, manufacturing control, and skilled labor training to ensure a consistent and high-quality output.
Material Selection and Testing
- Use high-quality raw materials to ensure product durability and performance.
- Conduct rigorous testing on leather, synthetic fabrics, rubber, and adhesives.
- Implement flexibility, wear resistance, and stress testing to verify material integrity before production.
Manufacturing Process Control
- Ensure precision cutting, stitching, and assembly through automated and manual inspections.
- Implement standardized work procedures to maintain consistency across production lines.
- Utilize real-time monitoring systems to detect irregularities and prevent defects early.
Workforce Training and Quality Awareness
- Train workers on best manufacturing practices and defect identification techniques.
- Establish strict standard operating procedures (SOPs) for each production stage.
- Foster a culture of quality awareness to encourage proactive defect prevention.
By implementing these key factors, manufacturers can reduce production errors, improve efficiency, and enhance overall product quality.
Effective Quality Control Measures in Shoe Manufacturing
Ensuring high-quality footwear requires a structured approach to quality control. The following are essential inspection techniques to minimize defects and maintain consistency:
Pre-Production Inspection (PPI)
- Verify the quality of raw materials and components before production begins.
- Conduct compliance checks to ensure materials meet design and safety specifications.
- Identify potential defects early to prevent issues in mass production.
In-Process Quality Inspection (DUPRO – During Production Inspection)
- Detect defects at key production stages such as cutting, stitching, assembly, and finishing.
- Use random sampling methods to monitor product consistency.
- Ensure that production meets the required standards before final assembly.
Final Random Inspection (FRI)
- Conduct Acceptance Quality Limit (AQL) sampling before shipment.
- Inspect overall appearance, functionality, and packaging to meet customer requirements.
- Prevent defective products from reaching customers, reducing returns and complaints.
Implementing a robust quality control system is essential for manufacturers looking to produce defect-free shoes while maintaining customer trust and brand integrity.
To ensure compliance with global footwear standards, refer to ASTM, ISO, and EN regulations on their official websites.
Supplier Quality Management for Footwear Manufacturing
A strong supplier quality management system is fundamental to defect prevention in shoe production. The quality of raw materials, adhesives, textiles, and components directly affects a shoe’s durability, comfort, and overall performance. Poor-quality inputs lead to manufacturing defects, product failures, and customer dissatisfaction.
The Importance of Supplier Selection in Footwear Manufacturing
- Choosing Reliable Suppliers – Partner with vendors that have a proven track record of delivering high-quality materials for footwear production.
- Supplier Audits & Certifications – Conduct rigorous audits to assess a supplier’s manufacturing capabilities, quality control processes, and ethical sourcing.
- Compliance with Sustainability Standards – Ensure that suppliers follow environmental and ethical guidelines, such as sustainable material sourcing and fair labor practices.
Implementing Supplier Audits & Performance Evaluations
To maintain consistent material quality, footwear brands should implement a structured supplier assessment framework:
- Supplier Scorecards – Track supplier performance based on quality consistency, on-time delivery, and defect rates.
- On-Site Supplier Inspections – Conduct factory visits to verify compliance with quality control standards and production best practices.
- Material Testing & Certifications – Require third-party test reports and certifications to confirm that raw materials meet industry safety standards.
Strategies for Ensuring Consistent Supplier Quality
- Develop Long-Term Supplier Partnerships – Establishing strong relationships with trusted suppliers fosters consistency and accountability in material quality.
- Implement Quality Agreements – Set clear material specifications, defect tolerances, and rejection criteria in supplier contracts.
- Use Random Sampling & Batch Testing – Conduct randomized quality checks on incoming materials to detect variations or defects early.
By enforcing strict supplier quality control, footwear manufacturers can prevent material-related defects, streamline production, and maintain superior product standards—ultimately delivering high-quality, defect-free shoes to consumers.
The Role of Third-Party Inspection Services in Shoe Defect Prevention
One of the most effective ways to prevent defects in shoe manufacturing is by leveraging third-party inspection services. These independent audits help manufacturers identify and eliminate defects before products reach consumers, reducing the risk of costly returns, recalls, and reputational damage.
Key Benefits of Third-Party Inspections in Footwear Quality Control
- Unbiased Quality Assessment – Third-party inspectors provide objective evaluations of footwear quality, ensuring that products meet industry standards and customer expectations.
- Detection of Hidden Defects – External inspections catch defects that may go unnoticed during in-house quality control, such as poor stitching, improper adhesive bonding, or material inconsistencies.
- Enhanced Brand Credibility – A commitment to third-party quality assurance strengthens consumer confidence, demonstrating that a brand prioritizes high-quality craftsmanship.
Ensuring Compliance Through Independent Audits
Beyond quality assurance, third-party inspections play a crucial role in regulatory compliance. Footwear manufacturers must adhere to various safety, environmental, and labor regulations to avoid legal penalties and maintain ethical production practices. Third-party footwear audits help by:
- Verifying Material Compliance – Ensuring that raw materials meet regulatory and industry-specific requirements.
- Ensuring Environmental & Ethical Standards – Confirming that supply chains adhere to sustainability and labor laws.
- Preventing Costly Recalls – Identifying potential compliance risks before products are released to market, minimizing financial and legal liabilities.
By integrating third-party inspections into their quality control strategy, footwear manufacturers can reduce defect rates, improve compliance, and maintain high product standards—ultimately protecting their brand reputation and market position.