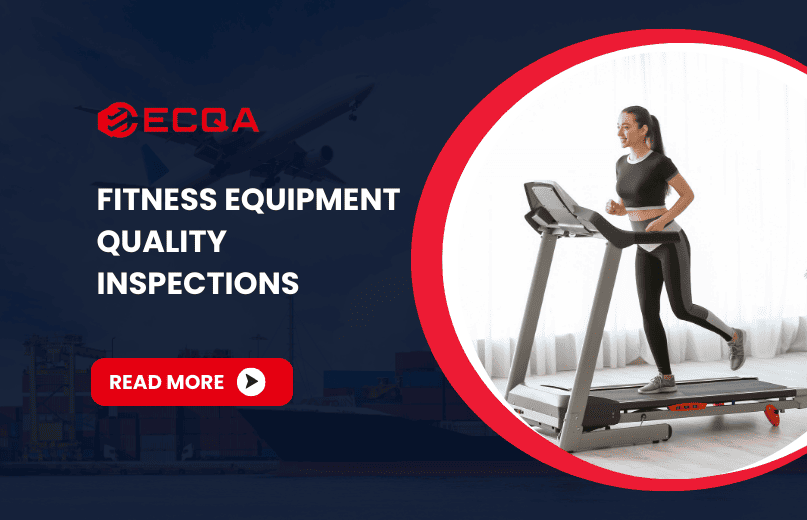
Fitness Equipment Quality Inspections
The global fitness industry is growing rapidly, with more gyms, hotels, and wellness centers investing in high-quality fitness equipment to meet customer expectations. At the same time, individual buyers are purchasing treadmills, exercise bikes, and strength training machines for personal home gyms. This rising demand creates an opportunity for distributors, brands, and suppliers, but it also brings a critical responsibility—ensuring that the equipment they sell is safe, durable, and free from defects.
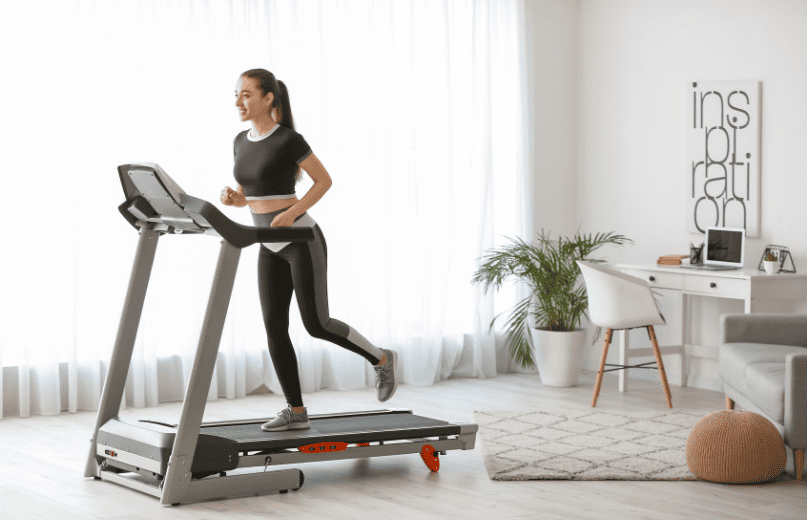
Selling substandard or unsafe fitness equipment can lead to serious consequences. A faulty treadmill or a weak weightlifting machine isn’t just a quality issue—it’s a safety hazard. Equipment failures can result in injuries, leading to liability claims, expensive product recalls, and damaged brand reputation. Whether supplying equipment to a high-end gym, a five-star hotel, or a home fitness enthusiast, ensuring consistent quality control is essential for protecting both businesses and end users.
In this article, we’ll break down the essential fitness equipment quality checklist—helping sellers, distributors, and brands understand what to inspect, how to prevent common defects, and why professional inspections are crucial for maintaining high industry standards.
Why Fitness Equipment Inspections Are Critical
For fitness equipment distributors, suppliers, and brands, ensuring quality control before selling is not just a formality—it’s a business necessity. Whether supplying to gyms, hotels, fitness centers, or individual buyers, sellers must guarantee that their equipment is safe, durable, and free from defects. Neglecting inspections can lead to expensive returns, customer complaints, and even legal issues. Here’s why a comprehensive fitness equipment inspection is essential for every seller:
1. Ensure Buyer Satisfaction with Reliable and Well-Built Equipment
Buyers expect high-performance fitness machines that function smoothly and safely. No gym owner or hotel manager wants to deal with equipment breakdowns just weeks after installation. By inspecting every critical component—from frame stability to electronic features—sellers can ensure their products meet customer expectations, leading to higher satisfaction rates and repeat business.
2. Avoid Costly Returns and Warranty Claims
Defective equipment doesn’t just harm users—it also hurts the seller’s bottom line. Faulty treadmills, loose weight machines, or malfunctioning digital displays can result in frequent returns and warranty claims, forcing sellers to cover repair or replacement costs. A quality inspection before shipment helps detect defects early, reducing financial losses and improving profitability.
3. Enhance Brand Reputation with Safe and Durable Equipment
Reputation is everything in the fitness industry. Selling unreliable or unsafe equipment can lead to negative reviews, loss of trust, and long-term brand damage. On the other hand, consistent quality control builds a strong brand image, positioning the seller as a trusted supplier of professional-grade fitness equipment. A commitment to safety and durability increases credibility and encourages long-term business relationships with gyms, hotels, and fitness centers.
4. Reduce Legal Risks by Meeting Safety Standards
Fitness equipment must comply with international safety standards such as:
- ISO 20957 – Safety and performance requirements for fitness machines.
- ASTM F2276 – Standards for exercise equipment used in commercial settings.
- EN 957 – European fitness equipment safety standards.
Failure to meet these certifications and regulations can lead to serious legal consequences, including fines, product recalls, and liability claims. An independent inspection ensures that fitness equipment meets all required safety standards, protecting both the seller and the end user.
5. Gain a Competitive Edge with High-Quality Products
The fitness equipment market is highly competitive, with buyers looking for well-built, long-lasting machines. Sellers that prioritize quality control can differentiate themselves by offering high-performance, safety-tested equipment. Investing in third-party inspections ensures that products meet professional industry standards, making them more attractive to buyers in commercial and personal fitness markets.
Essential Inspection Points for Fitness Equipment Sellers
To ensure high-quality, defect-free fitness equipment, sellers must conduct a thorough inspection covering multiple critical areas. From structural integrity to electronic functionality, every component must be tested to guarantee safety, durability, and performance. Below is a detailed inspection checklist that every distributor, supplier, and brand should follow before delivering fitness equipment to customers.
1. Structural Integrity & Frame Strength
The frame is the foundation of any fitness machine. Weak joints, poor welding, or rust can compromise stability and safety, leading to potential equipment failure. Inspectors should check for:
- Welding defects – Look for cracks, incomplete welds, or weak joints.
- Rust and corrosion – Ensure metal components have anti-corrosion coatings and show no signs of oxidation.
- Frame stability – Test for wobbling, bending, or unusual flexing when weight is applied.
- Material thickness – Verify that metal frames meet industry strength standards for commercial and home use.
2. Mechanical & Moving Parts
Most fitness machines rely on moving components, such as cables, pulleys, resistance bands, and weight stacks. A smooth and precise operation is essential to prevent premature wear or mechanical failures. Key inspection points include:
- Cables and pulleys – Check for fraying, misalignment, and tension consistency.
- Weight stacks – Ensure plates are properly aligned, securely fastened, and easy to adjust.
- Resistance bands and springs – Inspect for elasticity loss, cracks, or breakage risks.
- Bearings and rollers – Test for smooth movement without excessive noise or friction.
3. Electronic Features & Digital Components
Modern fitness equipment often includes touchscreens, heart rate monitors, Bluetooth connectivity, and tracking sensors. These features must be fully functional and user-friendly. Sellers should verify:
- Touchscreen responsiveness – Ensure the display reacts properly to touch inputs.
- Heart rate and sensor accuracy – Test pulse grips and chest strap compatibility.
- Connectivity features – Verify Bluetooth, Wi-Fi, and app synchronization capabilities.
- Power supply and wiring – Inspect power cords, battery connections, and adapters for safety and performance.
4. Material Quality & Durability
Low-quality materials can lead to premature wear, discomfort, and safety hazards. All components should be inspected for durability, comfort, and resistance to damage.
- Metal parts – Ensure high-strength steel or aluminum is used where required.
- Plastic and rubber parts – Check for cracks, warping, or brittleness in footrests, grips, and panels.
- Upholstery and padding – Verify stitching, cushioning density, and tear resistance.
- Coatings and finishes – Ensure scratch resistance and non-slip coatings meet quality standards.
5. Assembly & Fasteners
Loose or improperly installed fasteners can cause equipment failures. Inspectors must ensure all bolts, screws, and locking mechanisms are properly secured.
- Bolt tightness – Test for loose or over-tightened bolts that could strip or break.
- Locking pins and adjustment levers – Ensure they function smoothly and hold their position under load.
- Alignment of parts – Check that all components are correctly positioned according to specifications.
6. Load Testing & Weight Capacity
Buyers rely on weight capacity ratings to determine whether a piece of equipment is suitable for their needs. Sellers must confirm that advertised weight limits are accurate and safe.
- Stress testing – Apply maximum recommended loads to test for structural integrity.
- Dynamic load testing – Simulate real-world use to check for flexing, bending, or failure points.
- Repetitive motion testing – Run components through thousands of cycles to assess long-term durability.
7. Packaging & Labeling Compliance
Proper packaging prevents shipping damage, and correct labeling ensures compliance with safety regulations. Key inspection points include:
- Protective packaging – Verify the use of foam, plastic wrap, and reinforced cardboard to prevent transit damage.
- Instruction manuals – Ensure the correct language, diagrams, and safety warnings are included.
- Branding and compliance labels – Confirm that logos, barcodes, model numbers, and certification marks are correctly applied.
- Shipping tests – Conduct drop tests and vibration tests to simulate transportation stress.
Common Fitness Equipment Defects That Can Affect Sales
Fitness equipment must meet high durability, safety, and performance standards before it reaches the market. However, defects in construction, materials, or assembly can lead to customer dissatisfaction, product returns, and even safety hazards. Sellers must be aware of these common fitness equipment defects to prevent reputational damage and financial losses.
1. Weak Frames & Poor Welding
A weak frame is one of the most dangerous defects in fitness equipment. Poor welding, thin metal tubing, and low-quality materials can cause instability, leading to:
- Excessive wobbling during use, which can make workouts unsafe.
- Cracked or broken welds, increasing the risk of sudden structural failure.
- Bent or warped frames, reducing the machine’s lifespan and functionality.
- Rust and corrosion, which weaken metal over time, especially in humid environments.
2. Malfunctioning Digital Displays
Many modern fitness machines include digital displays to track time, speed, heart rate, calories burned, and resistance levels. However, defective electronics can lead to:
- Unresponsive touchscreens, frustrating users.
- Inaccurate tracking, causing users to question the equipment’s reliability.
- Intermittent power issues, where the display randomly turns off.
- Connectivity failures, preventing Bluetooth or app synchronization.
3. Snapping Resistance Bands & Cables
Resistance bands, pulleys, and cables are essential in many strength-training machines, but they can snap unexpectedly if they are made from low-quality materials or improperly assembled. This can result in:
- Serious injuries to users, including sudden recoil impacts.
- Equipment damage, leading to costly repairs or replacements.
- Decreased lifespan, as weakened components break prematurely.
4. Worn-Out Upholstery & Padding
Seats, backrests, and handles are typically covered in foam padding and upholstery to provide comfort. However, poor material quality can lead to:
- Cracking and peeling, making the equipment look old and unappealing.
- Flattened cushions, reducing comfort and ergonomic support.
- Torn seams and stitching, allowing internal padding to be exposed.
- Absorbed sweat and odor retention, which creates hygiene concerns.
5. Loose Bolts & Misaligned Parts
Even small defects, like loose bolts, misaligned adjustment levers, or improperly installed components, can pose serious safety risks. Common issues include:
- Seats or handles shifting unexpectedly, causing accidents.
- Pedals, pulleys, or belts slipping, leading to equipment malfunctions.
- Fasteners loosening over time, requiring constant maintenance.
Step-by-Step Inspection Process for Fitness Equipment
Ensuring fitness equipment meets high-quality standards requires a structured inspection process at multiple stages of production. By implementing a systematic approach, sellers can identify defects early, prevent costly returns, and maintain a strong brand reputation. Below is a step-by-step inspection process that covers all critical stages.
1. Pre-Production Inspection
Before manufacturing begins, a pre-production inspection ensures that the raw materials and components meet required safety, durability, and compliance standards. This step is crucial because low-quality materials can lead to weak frames, faulty electronics, and safety hazards.
Key Inspection Checks:
- Frame Materials: Inspect metal tubing, welding materials, and coatings to ensure strength, rust resistance, and structural integrity.
- Electronic Components: Check circuit boards, sensors, displays, and power cables for quality and compatibility.
- Upholstery & Padding: Verify fabric, foam density, and stitching durability to ensure comfort and longevity.
- Fasteners & Mechanical Parts: Assess screws, bolts, cables, and pulleys for proper dimensions, strength, and corrosion resistance.
2. During Production Inspection (DUPRO)
A During Production Inspection (DUPRO) takes place when 20-50% of production is complete. This step helps identify manufacturing inconsistencies and defects before full production is completed, allowing adjustments without costly delays.
Key Inspection Checks:
- Welding & Frame Assembly: Ensure joints are properly welded and free from cracks or misalignment.
- Mechanical Functionality: Test weight stacks, pulleys, resistance bands, and moving parts for smooth operation.
- Electronic Features: Verify that touchscreens, heart rate monitors, and Bluetooth connections work as intended.
- Component Assembly: Check for loose bolts, screws, and fasteners that could affect durability and safety.
3. Pre-Shipment Inspection (PSI)
A Pre-Shipment Inspection (PSI) is conducted when 100% of the products are manufactured and at least 80% are packed for shipment. This is the final opportunity to verify quality, functionality, and compliance before the products reach buyers.
Key Inspection Checks:
- Full Product Testing: Perform stress tests on weight capacity, moving parts, and electronic functions.
- Aesthetic & Build Quality: Inspect for scratches, dents, misaligned parts, and poor paint finishes.
- Safety Compliance: Verify adherence to ISO 20957, ASTM, EN 957, and other applicable standards.
- Correct Model & Specifications: Ensure all units match the purchase order and product specifications.
- Packaging & Labeling: Check carton strength, barcode accuracy, and included user manuals.
4. Loading & Packaging Inspection
Even high-quality products can get damaged during transit if packaging and loading procedures are not handled correctly. A Loading & Packaging Inspection ensures that fitness equipment is securely packed, labeled correctly, and protected for shipment.
Key Inspection Checks:
- Carton Strength & Packing Materials: Verify box durability, foam padding, and shock absorption to prevent damage.
- Proper Labeling & Documentation: Ensure product labels, barcodes, and shipping marks match regulatory requirements.
- Loading Process Verification: Check container conditions, stacking methods, and secure placement to prevent movement during transit.
The fitness equipment industry is highly competitive, and sellers must ensure their products meet strict quality, safety, and durability standards. Distributors, brands, and suppliers who fail to inspect their products risk customer dissatisfaction, costly returns, and potential legal issues due to faulty or unsafe equipment.
This is where third-party inspections come into play. A comprehensive fitness equipment inspection by professionals like ECQA helps verify quality at every stage—from manufacturing to final delivery. By conducting thorough structural assessments, safety tests, and compliance checks, suppliers can eliminate defective products before they reach customers. This not only reduces return rates and warranty claims but also strengthens customer trust and brand credibility in a competitive market.