
Container Loading Supervision
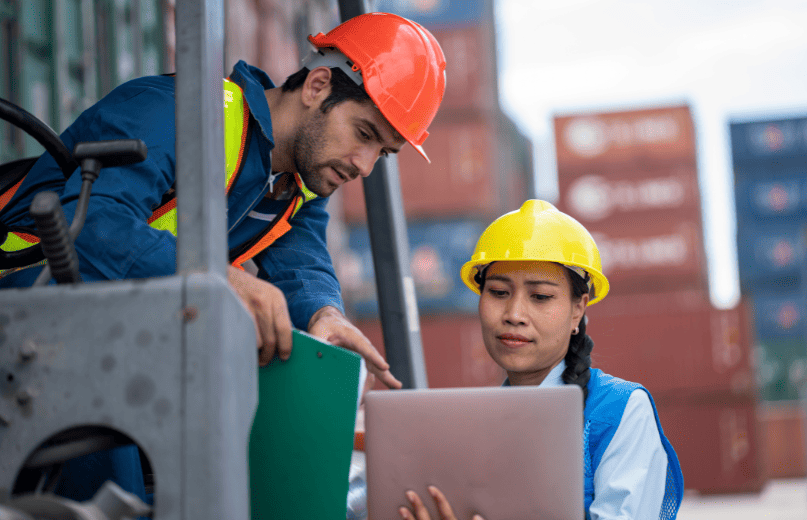
What Is Container Loading Supervision?
In international shipping, every step in the logistics chain plays a crucial role in ensuring cargo arrives safely and on time. One of the most critical yet often overlooked aspects is container loading supervision—a process that ensures goods are loaded correctly, securely, and in compliance with industry standards.
Container loading supervision (CLS) is a quality control and risk management service that oversees the loading process at factories, warehouses, or ports. The goal is simple but essential: to prevent costly mistakes that could lead to product damage, shipment delays, or regulatory violations.
This process involves trained inspectors who monitor, verify, and document every stage of loading, ensuring that:
- The correct products, quantities, and packaging materials are loaded according to the purchase order.
- The container is in optimal condition, free from leaks, rust, contamination, or structural weaknesses.
- Cargo is stacked and secured properly to prevent movement, crushing, or toppling during transit.
- Weight distribution is balanced to avoid issues with transportation, particularly in sea freight.
- Seals and security measures are correctly applied to prevent tampering or theft.
By implementing strict oversight and quality checks, container loading supervision reduces risks of damaged shipments, logistical errors, and non-compliance with international shipping regulations.
Who Needs Container Loading Supervision?
Any business that exports or imports goods on a large scale should consider container loading supervision as an essential part of their supply chain strategy. It provides an added layer of security and efficiency for:
- Importers & Exporters: Ensuring that shipments meet contractual requirements and arrive in the expected condition.
- Manufacturers: Verifying that finished products are correctly packed and protected before leaving the factory.
- Freight Forwarders & Logistics Providers: Mitigating risks related to improper loading and preventing liability issues.
- Retailers & Distributors: Avoiding stock losses and maintaining product integrity during long-distance transportation.
Key Industries That Rely on Container Loading Supervision
Certain industries are particularly vulnerable to improper loading, mishandling, and non-compliance issues. For these sectors, container loading supervision is not just an option—it’s a necessity:
- Retail & Consumer Goods: Fashion, apparel, furniture, and household products must be packed efficiently to prevent damage and optimize container space.
- Electronics & Technology: Fragile components require special handling and protection to prevent breakage and static damage.
- Automotive & Machinery: Large, heavy, or sensitive parts must be securely positioned to avoid shifting during transit.
- Food & Beverage: Hygiene, temperature control, and contamination risks make inspection of loading conditions essential for compliance with international safety standards.
- Pharmaceuticals & Healthcare Products: Strict regulations require precise documentation and quality control to ensure safety and efficacy.
With global supply chains facing increasing disruptions, businesses that invest in container loading supervision benefit from greater security, reduced risks, and improved shipment reliability. In the next section, we’ll explore the step-by-step process of how container loading supervision works and what inspectors look for during the inspection.
Why Is Container Loading Supervision Important?
Global trade moves at an unprecedented scale, with millions of containers shipped across oceans, railways, and highways every day. But behind the scenes, one misstep during the loading process can lead to costly damages, delays, and compliance violations. This is where container loading supervision (CLS) plays a vital role—acting as a safeguard against logistical nightmares.
Preventing Product Damage & Shipment Losses
Imagine a shipment of fragile electronics arriving at its destination only to be completely damaged due to improper stacking. Or a container of food products getting contaminated due to a leaking roof. These scenarios are more common than one might think, and they often stem from poor loading practices.
Container loading supervision ensures that products are properly handled, stacked, and secured, reducing risks of:
- Shifting during transit, which can lead to crushed, broken, or deformed goods.
- Improper weight distribution, causing instability in transit and increasing accident risks.
- Inadequate sealing and waterproofing, exposing shipments to environmental damage like moisture, mold, and rust.
- Overloading, which can lead to regulatory issues, rejection at ports, or safety hazards.
By having trained inspectors oversee the loading process, businesses can minimize product losses and ensure shipments arrive in the best possible condition.
Ensuring Compliance With International Shipping Laws & Safety Standards
In today’s interconnected world, regulatory compliance is more complex than ever. Countries have strict rules governing containerized shipments, covering everything from weight limits and fumigation requirements to hazardous material handling. A single mistake can lead to severe penalties, shipment rejections, or even legal action.
With container loading supervision, businesses can ensure that:
- Containers meet international shipping laws, including SOLAS (Safety of Life at Sea) weight verification.
- Packaging and labeling comply with industry regulations, preventing customs delays.
- Hazardous materials are handled and declared correctly, avoiding dangerous mishaps.
- Cold-chain logistics follow strict temperature control guidelines, essential for pharmaceuticals and perishable goods.
By proactively addressing compliance risks, companies can avoid unnecessary fines, delays, and operational headaches.
Reducing Financial Risks: Avoiding Claims, Disputes & Costly Re-Shipments
Logistics disputes are a common headache in international trade. Without proper documentation and oversight, buyers and sellers often face issues like:
- Claims over missing or incorrect products.
- Arguments about product damage during transit.
- Disputes regarding improper loading leading to losses.
Each of these problems can result in financial losses, strained supplier relationships, and even legal battles.
Container loading supervision provides a layer of accountability by documenting every stage of the loading process. This means:
- Photographic and written evidence of the loading process, protecting against false claims.
- Verification of quantity, quality, and packaging, ensuring the correct goods are shipped.
- Real-time reports and documentation, allowing immediate intervention if issues arise.
By preventing costly re-shipments and minimizing disputes, CLS helps businesses maintain profitability and operational efficiency.
Quality Control Assurance: Verifying That the Right Products & Quantities Are Loaded
For importers and exporters, one of the biggest risks is receiving the wrong goods or incorrect quantities. A single mistake in loading can result in:
- Stock shortages, impacting sales and production schedules.
- Rejected shipments, causing delays and financial losses.
- Quality control failures, leading to defective products reaching the market.
Container loading supervision acts as a last line of defense, ensuring that:
- The right products, quantities, and SKUs are loaded according to order specifications.
- Packaging meets quality standards, preventing damage and contamination.
- Seals and security tags are applied correctly, reducing the risk of tampering or theft.
Key Stages of Container Loading Supervision
Container loading supervision (CLS) isn’t just about watching workers load cargo—it’s a structured, multi-step process designed to ensure that shipments meet quality, safety, and regulatory standards. A professional third-party inspection team follows a series of critical checks to mitigate risks and provide transparency throughout the loading process. Let’s break down the four key stages of CLS and why each step matters.
1. Pre-Loading Inspection: Ensuring Goods Are Ready for Shipment
Before a single box is placed inside the container, inspectors conduct a thorough pre-loading inspection to verify the condition of the products, packaging, and labeling. This stage helps prevent issues before they escalate, ensuring that only properly packed and compliant goods proceed to the next step.
What Happens During Pre-Loading Inspection?
- Checking product condition – Ensuring that goods are free from visible defects, damages, or inconsistencies.
- Verifying packaging compliance – Confirming that packaging materials provide adequate protection against impact, moisture, and temperature fluctuations.
- Inspecting labeling and barcodes – Making sure that all shipping labels, barcodes, and handling instructions match the order specifications and regulatory requirements.
- Counting and reconciling quantities – Verifying that the correct number of units is ready for loading, minimizing the risk of shortages or overages.
A failed pre-loading inspection can delay shipments, increase costs, and damage supplier relationships. That’s why this step is crucial for quality assurance and regulatory compliance.
2. Container Condition Check: Ensuring a Safe Storage Environment
A container is more than just a steel box—it’s the first line of defense against environmental and logistical hazards. Before loading begins, a detailed container condition check ensures that the shipping unit is structurally sound, clean, and secure.
Critical Aspects of a Container Condition Check
- Inspecting for structural damage – Checking for dents, rust, leaks, or compromised areas that could expose goods to external damage.
- Verifying cleanliness and dryness – Ensuring that the interior is free from debris, odors, moisture, and contaminants that could affect sensitive products.
- Checking for pest infestations – Looking for signs of insects or rodents, especially for shipments of food, textiles, or pharmaceuticals.
- Confirming container markings – Validating that the container number, seal placement, and shipping documentation align with the order.
Overlooking container condition can lead to disastrous consequences, including moisture damage, contamination, or structural failures during transit. By catching these issues early, businesses can prevent costly rejections and shipping delays.
3. Loading Supervision: Ensuring Secure and Efficient Cargo Placement
Once the products pass the pre-loading and container condition checks, the actual loading process begins. This is where precision matters most—incorrect placement or improper securing can cause irreversible damage during transit.
What Happens During the Loading Supervision Stage?
- Monitoring weight distribution – Ensuring that the weight is evenly distributed to prevent tipping, shifting, or overloading.
- Checking stacking methods – Confirming that heavier goods are placed at the bottom, and fragile items are secured properly to prevent crushing.
- Securing cargo with appropriate fastenings – Ensuring that products are strapped, braced, or cushioned to minimize movement inside the container.
- Tracking loading sequence – Verifying that items are placed according to the unloading plan, especially for shipments with multiple destinations.
Failure to supervise the loading process can result in:
- Damaged goods due to improper stacking or inadequate securing.
- Container weight imbalances that could cause truck or vessel instability.
- Regulatory violations if hazardous materials are incorrectly loaded.
By overseeing the entire loading operation, professional inspectors significantly reduce risks and enhance cargo safety.
4. Sealing and Documentation: Protecting Shipment Integrity
The final stage of container loading supervision is sealing the container and completing all necessary documentation. This step serves as proof of compliance, security, and accountability—ensuring that shipments remain intact and untampered with until they reach their destination.
Key Tasks During Sealing and Documentation
- Applying high-security seals – Ensuring that the container is locked with tamper-proof, numbered seals that align with shipping records.
- Recording container and seal numbers – Documenting these details in official reports to prevent fraud or unauthorized access.
- Capturing photographic evidence – Taking photos of the loaded container, cargo arrangement, and seal application for transparency and dispute resolution.
- Issuing a final loading report – Providing shippers with a detailed inspection report that confirms compliance with all agreed standards.
A well-documented sealing and verification process helps businesses:
- Avoid customs issues by ensuring all paperwork is in order.
- Prevent cargo theft and tampering through traceable seals.
- Facilitate insurance claims in case of transit-related losses.
Each of these four stages plays a crucial role in ensuring the success of a shipment. By investing in professional container loading supervision, companies can:
- Minimize shipment losses and damages through proactive monitoring.
- Comply with international trade laws and avoid regulatory penalties.
- Enhance supply chain transparency and accountability for all stakeholders.
- Protect financial interests by preventing disputes and costly re-shipments.
Common Problems in Container Loading and Their Impact
Even with careful planning, container loading presents several challenges that can compromise shipment safety, quality, and compliance. If overlooked, these issues can lead to financial losses, legal disputes, and reputational damage for businesses. Below are the most common problems encountered during the loading process—and their potential consequences.
1. Overloading and Underloading: The Hidden Dangers of Uneven Weight Distribution
Weight distribution is one of the most critical factors in safe container transportation. When cargo is improperly loaded, it can cause serious safety hazards during handling, transit, and unloading.
Why Overloading Is a Serious Risk
- Structural damage to the container – Containers have weight limits for a reason. Overloading can lead to container deformations, weakened structures, or even collapses during stacking.
- Transportation instability – Overweight containers affect the balance of trucks, ships, and cranes, increasing the risk of accidents or rollovers.
- Regulatory fines and shipment delays – Many countries enforce strict weight restrictions. Exceeding these limits can result in customs penalties, forced cargo reductions, and costly reloading.
The Consequences of Underloading
- Wasted shipping space and higher costs – If a container is underloaded, businesses end up paying for unused capacity, leading to unnecessary shipping expenses.
- Increased risk of cargo shifting – Lighter loads are more susceptible to movement during transit, which can damage products and cause instability inside the container.
Solution: Professional loading supervision ensures that weight is distributed evenly, preventing both overloading and underloading.
2. Cargo Damage from Improper Stacking: Why Correct Positioning Is Crucial
Incorrect cargo placement is one of the leading causes of product damage in international shipping. If goods are stacked carelessly, even minor vibrations from road transport or rough seas can lead to breakages, crushing, or shifting.
Common Cargo Stacking Mistakes
- Heavy items placed on top of lighter goods – This causes fragile products to be crushed under excessive weight.
- Inadequate securing of cargo – Without proper fastenings, braces, or airbags, items may move freely within the container.
- Poor pallet stacking – If pallets are not aligned correctly, they can tip over, damaging both themselves and surrounding products.
Impact on Businesses
- High return and replacement costs – Damaged goods lead to customer complaints, refund requests, and reshipping expenses.
- Supply chain delays – A compromised shipment disrupts inventory management, affecting downstream operations.
- Reputational damage – Consistently damaged shipments erode customer trust and business credibility.
Solution: CLS professionals monitor stacking techniques, weight distribution, and securing methods to minimize risks.
3. Fraud and Substitution Risks: Ensuring Accurate Product Loading
Cargo theft and fraudulent product substitution are growing concerns in global trade. Without proper loading supervision, businesses are vulnerable to counterfeit goods, missing shipments, or tampered cargo.
How Fraud and Substitution Happen
- Product swaps at loading points – Unattended containers provide opportunities for criminals to replace genuine products with lower-quality imitations.
- Partial shipment fraud – A supplier may underload the container intentionally, reducing product quantities while still charging full price.
- Seal tampering – If container seals are not applied correctly or documented properly, it becomes easier for unauthorized access and cargo theft.
The Business Impact of Cargo Fraud
- Financial losses – Stolen or substituted goods reduce profit margins and create supply chain gaps.
- Legal liabilities – Fraudulent shipments can lead to contract disputes, customs violations, and potential lawsuits.
- Brand damage – Customers receiving counterfeit or incorrect products may lose confidence in a company’s reliability.
Solution: Sealing verification, loading supervision, and photographic documentation help prevent fraud and unauthorized substitutions.
4. Container Contamination and Pest Infestation: Hygiene Concerns for Perishable Goods
For industries like food & beverage, pharmaceuticals, and textiles, container cleanliness is non-negotiable. A single contaminated shipment can jeopardize an entire supply chain, resulting in recalls, regulatory penalties, and health risks.
Common Causes of Contamination and Infestation
- Moisture buildup inside containers – Excess humidity creates the perfect breeding ground for mold and bacteria.
- Leftover residues from previous shipments – If a container was previously used to transport chemicals, waste, or hazardous materials, residue contamination could affect new cargo.
- Pest infestations – Insects and rodents often hide in improperly cleaned containers, posing a significant threat to food safety and textile integrity.
Consequences of Contaminated Shipments
- Health risks and regulatory violations – Unsafe shipments can be rejected by customs, incurring heavy penalties.
- Product recalls and financial losses – A contaminated batch can force businesses to discard entire shipments, leading to major revenue losses.
- Reputation damage – If customers associate a brand with hygiene concerns or quality issues, long-term damage is inevitable.
Solution: Thorough container condition checks, pest control inspections, and moisture prevention strategies help safeguard shipments.
How CLS Helps Prevent These Issues
Every container loading issue comes with significant financial, legal, and operational risks. The good news? Proactive container loading supervision can prevent these costly problems.
By implementing professional loading inspections, weight checks, stacking supervision, and fraud prevention measures, businesses can:
- Minimize product damage and losses
- Comply with global shipping regulations
- Enhance supply chain security
- Protect brand reputation and customer trust
Global Regulations and Compliance in Container Loading
Ensuring proper compliance with international shipping regulations is critical for businesses engaged in global trade. Non-compliance can lead to cargo rejection, fines, and legal issues, making it essential to follow the global standards governing container loading and shipping.
From international maritime laws to country-specific customs requirements, businesses must navigate a complex regulatory landscape to avoid costly delays.
1. International Maritime Organization (IMO) and SOLAS Regulations
The International Maritime Organization (IMO) sets global safety and environmental standards for international shipping. One of the most crucial IMO regulations affecting container loading is SOLAS (Safety of Life at Sea).
Key SOLAS Container Loading Requirements:
- Verified Gross Mass (VGM) Rule – Every packed container must have an accurate weight declaration before it can be loaded onto a vessel.
- Container Structural Integrity – Containers must be fit for transport, ensuring they are not damaged, leaking, or structurally compromised.
- Proper Stowage and Securing – Cargo must be secured to prevent shifting, which could endanger crew members and other shipments.
⚠️ Non-compliance with SOLAS can result in shipment rejection, penalties, and operational delays.
2. ISO Standards for Packaging and Loading
The International Organization for Standardization (ISO) provides global benchmarks for safe and efficient cargo handling. These standards cover everything from container strength to loading procedures, helping businesses comply with international best practices.
Important ISO Standards in Container Loading:
- ISO 668 – Defines standard container sizes and dimensions for uniformity in global shipping.
- ISO 1496 – Specifies container structural requirements, ensuring they can withstand the stresses of transport.
- ISO 22000 – Covers food safety management for perishable goods during shipment.
- ISO 9001 – Provides a framework for quality control in logistics and supply chain management.
Adhering to ISO standards not only ensures compliance but also enhances cargo safety, minimizes losses, and improves supply chain efficiency.
3. Country-Specific Import/Export Compliance Requirements
Each country enforces its own regulations for containerized shipments, often including product labeling, customs duties, and restricted goods lists. Understanding these regulations reduces the risk of shipment delays or confiscation.
Examples of Country-Specific Regulations:
- United States – U.S. Customs and Border Protection (CBP) requires ISF (Importer Security Filing) before shipment departure.
- European Union – The EU’s CE Marking applies to specific product categories, ensuring compliance with safety directives.
- China – The General Administration of Customs (GAC) mandates China Compulsory Certification (CCC) for various imported goods.
- Australia – Strict biosecurity and quarantine regulations apply, especially for food, plants, and animal-based products.
4. Customs Clearance and Essential Shipping Documents
Before a shipment can be released, it must undergo customs clearance in both the exporting and importing country. This process involves verifying documents, taxes, and compliance with trade regulations.
Essential Shipping Documents for Containerized Cargo:
- Bill of Lading (BOL) – A legal document that confirms cargo ownership and shipping details.
- Commercial Invoice – Provides product descriptions, value, and payment terms for customs authorities.
- Packing List – Details the contents, weight, and dimensions of the shipment.
- Certificate of Origin (COO) – Declares the country where the goods were manufactured, often required for tariff reductions.
- Customs Declaration Forms – Vary by country but are necessary for duties, tariffs, and import controls.
Missing or incorrect documentation can result in shipment delays, additional costs, or customs seizure.
Conclusion: Ensuring Smooth and Secure Container Loading for Global Trade
Proper container loading supervision is not just an added precaution—it’s a necessity. Every step, from pre-loading inspections to securing cargo and verifying documentation, plays a crucial role in ensuring shipments arrive safely, on time, and in compliance with international regulations.
Failure to implement strict loading controls can lead to cargo damage, regulatory penalties, and financial losses. Businesses that prioritize professional inspection services gain a competitive edge by reducing risks, improving efficiency, and maintaining compliance with global standards.
Why Choose ECQA for Container Loading Supervision?
As a leading third-party inspection company, ECQA ensures that every container loading supervision process meets strict quality and safety standards.
With years of experience, ECQA’s inspection team understands the complexities of international logistics and ensures smooth, error-free loading operations. We offer customized supervision plans based on industry needs, cargo type, and client requirements, ensuring maximum cargo protection.Learn more about The Role of Third-Party Inspection Companies in Loading Supervision and how professional inspection services help safeguard your shipments.
Get Professional Container Loading Supervision Services Today
Contact us today to learn more about our loading supervision services and secure your international shipments with certified quality control experts.
Frequently Asked Questions (FAQ) About Container Loading Supervision
1. What is container loading supervision, and why is it important?
Container Loading supervision is a quality control process where inspectors oversee the loading of cargo to ensure it is properly handled, securely packed, and compliant with international regulations. This prevents damage, mismanagement, and shipping delays, ensuring safe and efficient transportation.
2. What does a container loading supervisor check during an inspection?
A professional loading supervisor verifies:
- Cargo condition before loading
- Proper stacking and weight distribution
- Container integrity and security seals
- Documentation accuracy to meet customs and regulatory requirements
- Compliance with packaging and shipping regulations
3. Who needs container loading supervision services?
Businesses involved in international trade, logistics, and manufacturing benefit from loading supervision. This includes importers, exporters, freight forwarders, and e-commerce businesses that require cargo protection and quality assurance.
4. How does third-party loading supervision improve supply chain reliability?
Hiring a third-party inspection company ensures independent, unbiased verification of cargo handling. This helps businesses:
- Reduce risks of shipment rejection
- Prevent financial losses from damaged goods
- Comply with international shipping laws and safety standards
- Increase customer trust by ensuring cargo integrity
5. Can container loading supervision prevent cargo theft and tampering?
Yes. Professional inspectors monitor the entire loading process, ensuring that containers are properly sealed, access is restricted, and security measures are in place to prevent theft or unauthorized handling.
6. How much does container loading supervision cost?
The cost depends on several factors, including cargo type, location, inspection scope, and regulatory requirements. For a customized quote, businesses can contact ECQA to discuss their specific needs.
7. How do I book ECQA’s loading supervision services?
You can request a quote through our website or contact our inspection experts for a personalized consultation tailored to your shipping needs.