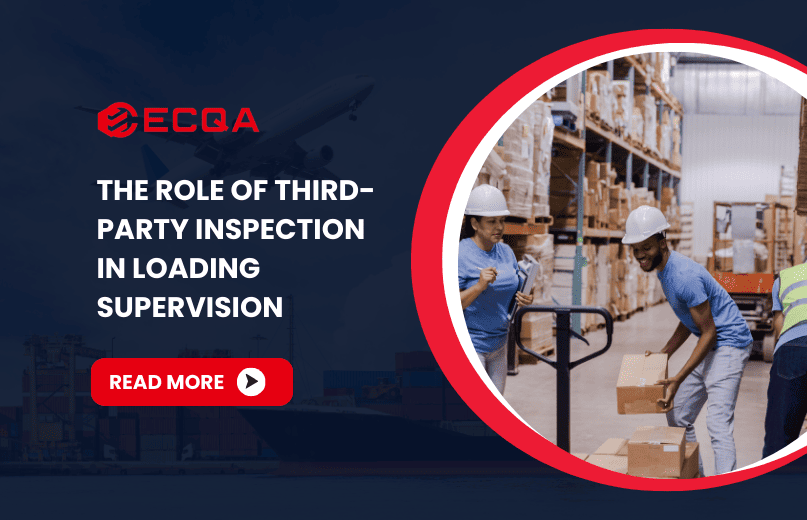
Third-Party Loading Supervision
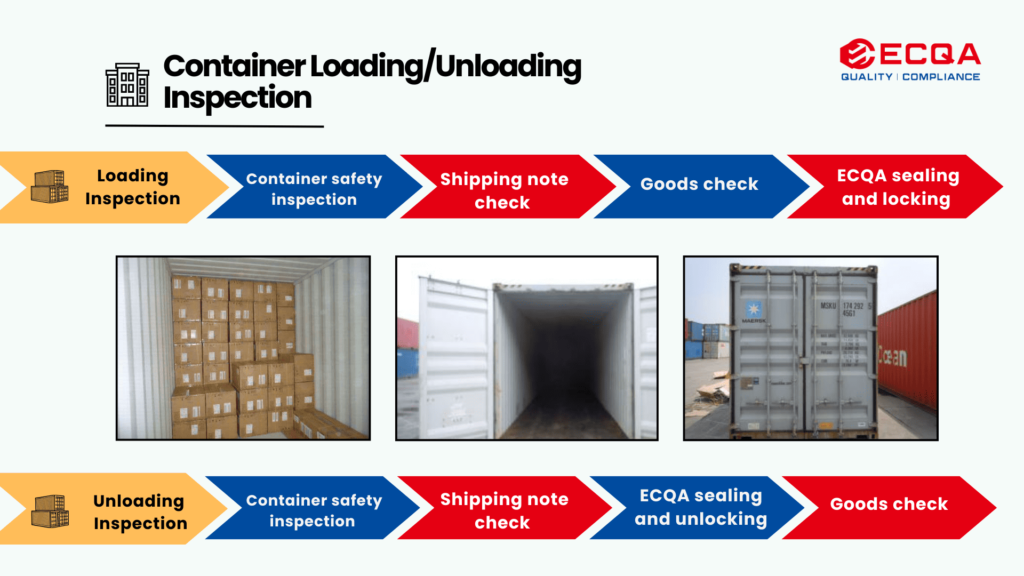
Container Loading supervision by a third party has become a critical component for companies seeking to maintain quality control and avoid costly disputes. This service provides an impartial, on-site inspection during the loading process, ensuring that goods are handled properly, documented accurately, and loaded according to the client’s specifications.
This is where professional third-party loading inspection services play a vital role. By following a structured loading supervision process, inspectors ensure that packaging, weight distribution, and securing methods meet industry standards. With real-time reporting, photo documentation, and regulatory checklists, professional inspections minimize risks and enhance shipment reliability.
Why Choose Third-Party Loading Supervision
Some businesses rely on internal staff or suppliers to oversee the loading process. While this might seem cost-effective, it comes with significant risks:
- Lack of specialized expertise – Internal teams may not have the necessary training to identify issues related to weight distribution, securing methods, or compliance.
- Conflicts of interest – Suppliers and manufacturers may prioritize speed over quality, potentially overlooking critical loading mistakes.
- Limited visibility and control – Importers and buyers often operate remotely, making it impossible to monitor loading firsthand.
How Third Party Improve Loading Supervision
1. Step-by-Step Supervision Process Followed by Inspectors
A professional container loading inspection (CLS) follows a structured process to identify and eliminate risks before shipment. The goal is to guarantee product safety, compliance, and proper handling from the loading site to final departure.
Step 1: Pre-Loading Inspection
Before a single item is loaded, inspectors examine all cargo to verify that it meets quality standards and order specifications. This includes:
- Checking packaging integrity to ensure no damaged or poorly packed products are loaded.
- Verifying labeling accuracy to confirm all labels comply with shipping regulations and contain the correct product details.
- Inspecting product conditions for defects, contamination, or unauthorized substitutions.
Step 2: Container Condition Check
A damaged or contaminated container can compromise an entire shipment. Inspectors conduct a full evaluation of the container to ensure it is:
- Clean and dry – Free of moisture, debris, and chemical residues.
- Structurally sound – No holes, rust, or broken door seals.
- Free from pest infestation – No signs of rodents or insects.
Step 3: Loading Supervision
Once loading begins, inspectors oversee the entire process to ensure that:
- Weight is evenly distributed – Preventing overloading, underloading, or imbalance.
- Cargo is stacked correctly – Heavy items placed at the bottom, fragile goods properly cushioned.
- Securing methods are applied – Cargo is fastened with braces, airbags, or straps to prevent movement.
Step 4: Sealing and Documentation
To ensure the shipment remains tamper-proof, inspectors:
- Verify container seals – Ensuring proper application to prevent unauthorized access.
- Record shipment details – Documenting seal numbers, loading time, and final cargo condition.
- Capture photographic and video evidence – Providing visual proof of compliance.
2. Use of Real-Time Reporting, Photos, and Video Documentation
Real-time reporting plays a crucial role in modern container loading inspections. Clients receive live updates, photographic evidence, and detailed reports throughout the process, ensuring full transparency.
Key Benefits of Real-Time Reporting:
- Immediate issue resolution – If a problem arises (e.g., damaged products or incorrect labeling), businesses can take immediate corrective action.
- Proof of compliance – Photos and videos serve as evidence in case of disputes with suppliers, shipping companies, or customs authorities.
- Improved supply chain visibility – Clients can track inspection progress remotely, reducing uncertainties.
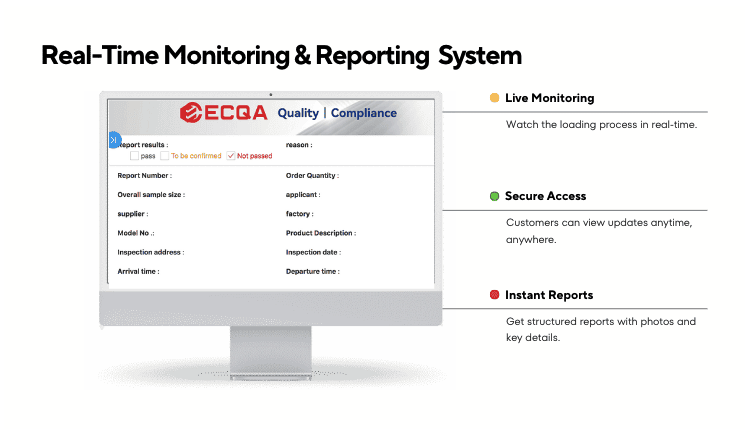
ECQA uses a reporting system that allows inspectors to upload data instantly, providing businesses with real-time insights into their shipments.
3. Compliance Verification to Meet Regulations
Shipping regulations vary depending on the destination country, product category, and industry standards. Professional inspectors follow detailed checklists to verify compliance and reduce the risk of shipment rejections or fines.
Key Compliance Factors Checked During CLS:
- Weight & cargo limits – Ensuring the shipment adheres to international shipping weight restrictions.
- Packaging & labeling laws – Verifying compliance with FDA, EU, or other regulatory body requirements.
- Product quality and safety – Ensuring that hazardous materials, perishable goods, and fragile items meet industry safety standards.
- Container seal integrity – Documenting and verifying tamper-proof sealing.
By using standardized checklists and compliance verification, professional inspection services reduce the risk of legal penalties, shipment delays, and rejected cargo.
Learn more about third-party inspection services in China in our Complete Guide to Quality Inspection Services in China for Importers.
Benefits of hiring Third Party Inspection Firm – ECQA
Choosing a trusted third-party inspection company can make all the difference in securing safe, compliant, and efficient shipments. Companies like ECQA offer specialized container loading supervision services tailored to the needs of importers, exporters, manufacturers, and freight forwarders.
Why Partner with ECQA for Container Loading Supervision?
- Industry Expertise – ECQA’s experienced inspectors understand the complexities of international shipping and loading best practices.
- Customized Inspection Plans – Services are tailored to specific industry needs, including retail, electronics, automotive, and food & beverage.
- Advanced Reporting & Transparency – Clients receive real-time reports, high-resolution photos, and detailed inspection summaries.
- Compliance Assurance – ECQA ensures that shipments meet international shipping laws and quality regulations, preventing costly fines and rejections.
- Global Coverage – With a network of inspectors in key manufacturing and shipping hubs, ECQA provides reliable container loading supervision worldwide.
Partnering with a reputable third-party inspection provider ensures businesses maintain full control over cargo loading, prevent product damage, and meet compliance standards—without the challenges of self-supervision.