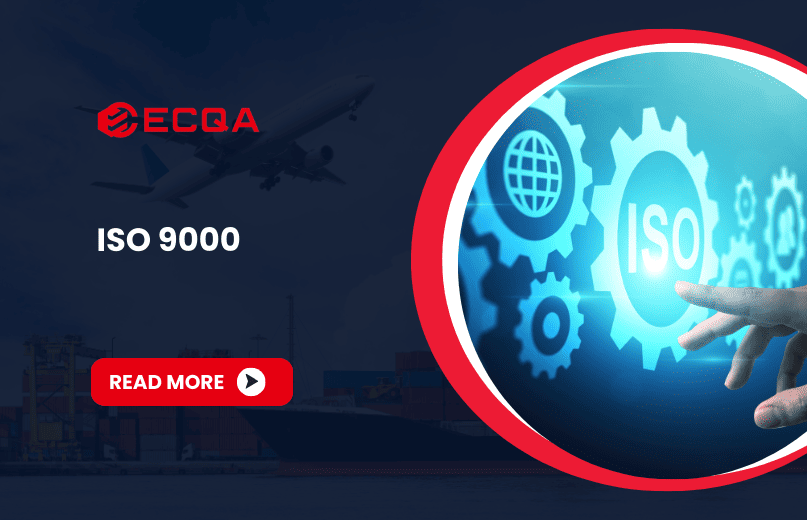
ISO 9000
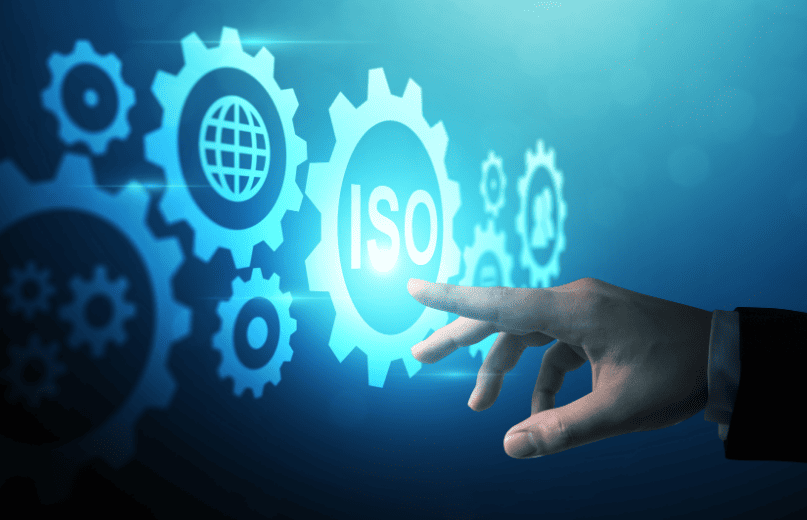
As a globally recognized framework for quality management, ISO 9000 helps organizations streamline operations, improve efficiency, and enhance customer satisfaction. Whether you’re a small business or a multinational corporation, understanding and implementing ISO 9000 principles can significantly impact your long-term success.
In this guide, we’ll explore everything you need to know about ISO 9000, including:
- What ISO 9000 is and how it differs from ISO 9001
- The seven core principles of ISO 9000 and why they matter
- How ISO 9000 benefits businesses across different industries
- A step-by-step process for implementing ISO 9000 effectively
- Common challenges and practical solutions
By the end of this guide, you’ll have a comprehensive understanding of ISO 9000 and how to leverage it to build a strong, efficient, and competitive organization.
What is ISO 9000?
Many businesses assume that ISO 9000 is a certification they can obtain, but this is a common misconception. ISO 9000 is not a single standard or certification—it is a family of standards that define the fundamental principles of quality management.
At its core, ISO 9000 serves as a framework for organizations looking to implement, maintain, and improve a Quality Management System (QMS). It outlines the terminology, principles, and best practices necessary to achieve consistency, efficiency, and customer satisfaction in business operations.
ISO 9000 vs. ISO 9001: Understanding the Difference
One of the most important distinctions to make is between ISO 9000 and ISO 9001. While they are often used interchangeably, they serve different purposes:
- ISO 9000 – A guideline document that provides the fundamental concepts, principles, and vocabulary for quality management. It helps businesses understand the foundation of a QMS, ensuring a solid framework for future improvements.
- ISO 9001 – The actual certifiable standard that companies must adhere to in order to achieve ISO certification. It contains specific requirements that organizations must implement within their QMS to demonstrate compliance.
Think of ISO 9000 as the theory behind quality management, while ISO 9001 is the practical application that companies must follow to become certified.
Why ISO 9000 Matters
Even though ISO 9000 itself is not certifiable, it plays a crucial role in shaping global quality management practices. It provides businesses with:
- A universal language for quality management, ensuring clear communication across industries.
- A strong foundation for implementing ISO 9001 or other quality-focused initiatives.
- A flexible approach that applies to businesses of all sizes, from startups to multinational corporations.
By understanding ISO 9000, organizations can build a robust quality management system that improves efficiency, reduces errors, and enhances customer satisfaction.
The Core Principles of ISO 9000
At the heart of ISO 9000 lies a set of seven quality management principles that guide organizations in building a strong, effective Quality Management System (QMS). These principles are not rigid rules but strategic guidelines that help businesses focus on efficiency, customer satisfaction, and continuous improvement.
Let’s break down each principle and explore how they contribute to a high-performing, quality-driven organization.
1. Customer Focus
The first and most fundamental principle of ISO 9000 is customer focus. Every business thrives on customer satisfaction, and an effective QMS ensures that products and services meet or exceed customer expectations.
To implement customer-focused quality management, organizations should:
- Understand customer needs through surveys, feedback, and market research.
- Deliver consistent quality by reducing defects and improving reliability.
- Foster long-term relationships by prioritizing customer service and loyalty.
A real-world example? Amazon’s relentless commitment to customer satisfaction—from fast delivery to responsive service—has made it a dominant global brand. By putting customers at the center, businesses can drive loyalty, reputation, and profitability.
2. Leadership
Strong leadership is the backbone of any successful quality management system. When top management commits to quality-driven goals, employees follow suit.
A quality-focused leadership team:
- Defines a clear vision that aligns business goals with quality standards.
- Encourages accountability, ensuring that employees understand their role in delivering quality.
- Inspires a culture of excellence, making quality a shared responsibility across the organization.
Example: Toyota’s leadership pioneered lean manufacturing and Kaizen (continuous improvement), embedding quality into every level of production. The result? Industry-leading reliability and efficiency.
3. Engagement of People
A quality management system is only as strong as the people behind it. Engaged employees take ownership of their work, contribute ideas, and strive for excellence.
To foster engagement:
- Empower employees with training and development.
- Encourage open communication, allowing workers to share feedback on processes.
- Recognize contributions, creating motivation for quality improvement.
Companies like Google and Apple invest heavily in employee engagement, leading to innovation, efficiency, and superior product quality.
4. Process Approach
Instead of viewing tasks in isolation, ISO 9000 promotes a process-driven mindset. Every business function is interconnected, and optimizing processes leads to better outcomes, fewer errors, and increased efficiency.
A strong process approach:
- Identifies key workflows and removes bottlenecks.
- Standardizes procedures, reducing variability and improving consistency.
- Uses performance metrics to track efficiency and optimize results.
Example? McDonald’s standardized cooking processes ensure consistent taste, quality, and speed across thousands of locations worldwide.
5. Continuous Improvement
In today’s fast-changing market, stagnation is not an option. ISO 9000 encourages organizations to embrace a continuous improvement mindset, ensuring that quality processes evolve over time.
How businesses implement continuous improvement:
- Use data analytics to identify inefficiencies.
- Encourage innovation by allowing employees to suggest improvements.
- Regularly review and update quality standards to keep up with industry trends.
Companies like Tesla constantly innovate and refine their manufacturing processes, ensuring their vehicles remain cutting-edge.
6. Evidence-Based Decision Making
Rather than relying on assumptions or gut feelings, ISO 9000 emphasizes decision-making based on real data. This ensures that changes and improvements are driven by facts, not guesswork.
To apply evidence-based decision-making, organizations should:
- Collect and analyze key performance indicators (KPIs).
- Use quality audits to assess compliance and effectiveness.
- Base strategic decisions on measurable outcomes.
For example, Airlines like Delta and Emirates use real-time flight and maintenance data to enhance safety and operational efficiency.
7. Relationship Management
No business operates in isolation. Suppliers, partners, and stakeholders play a vital role in maintaining quality standards. Strong relationships ensure better supply chain management, fewer disruptions, and higher efficiency.
Best practices for relationship management:
- Build long-term supplier partnerships based on trust and quality expectations.
- Ensure transparency in communication to prevent misunderstandings.
- Monitor supplier performance to maintain high standards.
A great example is Apple’s strict supplier quality control, ensuring that every component in its devices meets high-performance standards.
By implementing these seven core principles, businesses can create a culture of quality, improve operational efficiency, and build long-term customer trust.
Why is ISO 9000 Important?
1. Enhancing Business Credibility and Trust
In a crowded marketplace, credibility is everything. When a company aligns with ISO 9000 standards, it signals to customers, investors, and partners that it prioritizes quality and efficiency.
How does ISO 9000 improve credibility?
- It demonstrates a commitment to continuous improvement.
- It assures customers that products and services meet consistent quality standards.
- It helps businesses compete for high-value contracts, as many large corporations require suppliers to comply with ISO standards.
2. Boosting Operational Efficiency and Reducing Waste
An effective Quality Management System (QMS) isn’t just about meeting standards—it’s about streamlining operations and eliminating inefficiencies. ISO 9000 helps businesses:
- Optimize workflows, reducing redundant tasks.
- Lower production costs by identifying and eliminating waste.
- Improve employee productivity with well-defined roles and responsibilities.
Example: Siemens, a global engineering company, implemented ISO 9000 to reduce operational errors and enhance production efficiency. The result? Lower costs, higher product reliability, and a more efficient supply chain.
3. Strengthening Customer Satisfaction and Loyalty
Customers expect consistency and reliability. If a product works perfectly once but fails the next time, trust is lost. ISO 9000 ensures that businesses maintain uniform quality, leading to higher customer satisfaction.
Companies that prioritize ISO 9000’s customer focus:
- Reduce defects and minimize product recalls.
- Improve service consistency, building brand reputation.
- Enhance response times through structured feedback mechanisms.
4. Ensuring Regulatory Compliance and Market Expansion
Many industries require businesses to comply with international quality standards. Without ISO 9000, companies may struggle to enter regulated markets or obtain necessary certifications.
Key regulatory benefits of ISO 9000:
- Simplifies compliance with safety and quality regulations.
- Reduces legal risks by ensuring adherence to industry requirements.
- Opens doors to new markets, especially in international trade.
By embracing ISO 9000, businesses can enhance credibility, streamline operations, improve customer satisfaction, and ensure regulatory compliance.
ISO 9000 vs. ISO 9001: What’s the Difference?
When discussing ISO 9000 and ISO 9001, many businesses assume they refer to the same thing. However, there’s a crucial difference between them.
ISO 9000: The Guiding Framework
ISO 9000 is a set of guidelines and principles designed to help organizations develop an effective Quality Management System (QMS). It outlines the core concepts of quality management but does not contain specific requirements for certification.
✔ Purpose: Provides the fundamental principles and vocabulary for quality management.
✔ Scope: Helps organizations understand the philosophy behind quality assurance.
✔ Applicability: Used as a reference document to guide businesses in structuring their QMS.
Think of ISO 9000 as a blueprint—it defines the key concepts but doesn’t dictate how a business must implement them.
ISO 9001: The Certifiable Standard
ISO 9001, on the other hand, is the actual standard that businesses get certified for. It sets specific requirements for establishing, maintaining, and improving a Quality Management System.
✔ Purpose: Ensures businesses meet internationally recognized quality standards.
✔ Scope: Defines mandatory requirements that organizations must follow to achieve certification.
✔ Applicability: Used by companies seeking ISO certification to prove their commitment to quality.
Unlike ISO 9000, which serves as a conceptual guide, ISO 9001 is a structured set of rules and criteria that companies must comply with to earn certification.
Key Differences at a Glance
Feature | ISO 9000 | ISO 9001 |
Type | Conceptual framework | Certifiable standard |
Purpose | Defines quality principles | Outlines QMS requirements |
Certification? | No | Yes |
Scope | Broad guidelines | Detailed requirements |
Usage | Reference for quality management | Mandatory for certification |
How They Work Together
While ISO 9000 and ISO 9001 are different, they are closely connected. ISO 9000 lays the foundation, while ISO 9001 builds upon it with specific, actionable requirements.
For businesses seeking ISO 9001 certification, understanding ISO 9000 is the first step. By mastering the principles in ISO 9000, companies can effectively implement ISO 9001 and achieve compliance.
By understanding the difference between ISO 9000 and ISO 9001, businesses can make informed decisions about quality management. In the next section, we’ll explore How to Implement ISO 9000 in Your Business.
Steps to Implementing ISO 9000 in Your Business
Adopting ISO 9000 is a strategic move that requires careful planning and execution. Unlike ISO 9001, which involves a formal certification process, ISO 9000 serves as a guiding framework for establishing a structured Quality Management System (QMS).
For businesses looking to integrate ISO 9000 principles, here’s a step-by-step guide to ensure a seamless transition and lasting success.
1. Understand the Requirements
Before implementing ISO 9000, it’s essential to understand its principles and how they align with your business operations. ISO 9000 emphasizes quality management best practices, helping businesses create a system that fosters continuous improvement, efficiency, and customer satisfaction.
What to do:
✔ Familiarize yourself with ISO 9000’s core principles, including customer focus, process approach, and continuous improvement.
✔ Assess how your current quality practices compare to these principles.
✔ Consider consulting an expert or using official ISO resources for deeper insights.
2. Perform a Gap Analysis
A gap analysis helps businesses evaluate their existing processes against ISO 9000 principles. This step identifies deficiencies and areas for improvement, ensuring a clear roadmap for implementation.
What to do:
✔ Conduct an internal audit of your current quality management practices.
✔ Identify weaknesses, inefficiencies, and non-compliance areas.
✔ Gather feedback from employees and customers to pinpoint operational gaps.
Example: A manufacturing company performing a gap analysis might discover inconsistent quality checks, leading to product defects. By addressing these gaps, the company can enhance its quality control processes before implementing ISO 9000.
3. Develop a Quality Management System (QMS)
A Quality Management System (QMS) is the foundation of ISO 9000 implementation. It consists of documented policies, procedures, and guidelines that ensure consistency, accountability, and compliance with quality management principles.
What to do:
✔ Define standard operating procedures (SOPs) for key processes.
✔ Establish clear quality policies and objectives aligned with ISO 9000.
✔ Implement document control measures to ensure proper record-keeping.
Example: A logistics company developing a QMS might create standardized checklists for shipment handling, ensuring consistency and reducing errors in deliveries.
4. Train Your Team
Successful implementation of ISO 9000 requires full organizational commitment. Employees at all levels should understand the importance of quality management and their role in upholding it.
What to do:
✔ Conduct training sessions to educate employees on ISO 9000 principles.
✔ Promote a quality-driven culture by involving all departments.
✔ Provide ongoing coaching and refresher courses to ensure continuous engagement.
Example: A customer service team trained on ISO 9000 might implement structured complaint resolution processes, improving response times and customer satisfaction.
5. Monitor and Improve Processes
ISO 9000 encourages continuous improvement through regular monitoring, internal audits, and performance reviews. Businesses should establish a feedback loop to identify areas for enhancement and refine their QMS over time.
What to do:
✔ Set up performance metrics to track quality improvements.
✔ Conduct internal audits to ensure compliance with ISO 9000 principles.
✔ Use customer and employee feedback to refine processes and drive improvements.
Example: A software company might analyze customer bug reports to identify recurring issues and implement process improvements, ensuring higher software reliability.
6. Prepare for ISO 9001 Certification (If Applicable): Align with Certifiable Requirements
While ISO 9000 itself is not a certifiable standard, businesses aiming for ISO 9001 certification should align their QMS with ISO 9001 requirements. This involves formal audits, documentation, and compliance with specific quality management criteria.
What to do:
✔ Review ISO 9001 standards and compare them with your QMS.
✔ Conduct a pre-certification audit to identify any gaps.
✔ Work with a certification body to complete the audit process.
Example: A supplier seeking ISO 9001 certification might undergo an external audit, demonstrating compliance with documented quality standards to gain certification.
By following these step-by-step guidelines, businesses can effectively integrate ISO 9000 principles, leading to stronger operational efficiency, better risk management, and enhanced customer satisfaction.
To successfully implement ISO 9000, businesses should conduct regular audits and inspections. Partnering with professional Third-Party Inspection Services can help identify gaps and maintain compliance
Common Challenges in Implementing ISO 9000 and How to Overcome Them
While ISO 9000 provides a structured approach to quality management, implementing its principles is not without challenges. Many businesses face resistance from employees, struggle with documentation requirements, or find it difficult to maintain long-term improvements.
Understanding these obstacles and applying effective solutions can ensure a smooth transition and sustained success.
1. Resistance to Change
One of the most common challenges businesses face when implementing ISO 9000 is resistance from employees and management. People often fear disruptions to their workflow, additional responsibilities, or uncertainty about new processes.
How to Overcome It:
✔ Communicate the benefits of ISO 9000 clearly, emphasizing how it improves efficiency and reduces errors.
✔ Involve employees early in the process to gain buy-in and make them feel part of the transformation.
✔ Offer training and support to help employees understand ISO 9000’s role in their daily tasks.
✔ Encourage a culture of continuous improvement by recognizing and rewarding contributions to quality initiatives.
2. Documentation Overload
ISO 9000 emphasizes proper documentation, but businesses often struggle with excessive paperwork, making implementation feel overwhelming. Managing policies, procedures, and reports efficiently is crucial to avoid operational slowdowns.
How to Overcome It:
✔ Use digital tools like document management software to organize and track ISO-related documentation.
✔ Streamline processes by eliminating redundant paperwork while keeping essential records.
✔ Assign dedicated roles for document control to ensure compliance without burdening employees.
✔ Focus on simplicity—documents should be clear, concise, and relevant to daily operations.
3. Maintaining Continuous Improvement
Many businesses achieve initial ISO 9000 compliance but struggle with sustaining quality improvements over time. Without a strategy for continuous monitoring and adaptation, processes may gradually fall back into old habits.
How to Overcome It:
✔ Schedule regular internal audits to assess compliance and identify areas for improvement.
✔ Encourage employee feedback to refine processes based on real-world application.
✔ Use data analytics to track performance trends and adjust strategies proactively.
✔ Set up a continuous improvement team to drive ongoing quality initiatives.
By addressing these common challenges proactively, businesses can successfully integrate ISO 9000, ensuring smoother adoption, long-term compliance, and continuous improvement.
The Value of ISO 9000 in Achieving Long-Term Quality Excellence
Implementing ISO 9000 standards is more than just a procedural requirement—it’s a strategic investment that enhances business credibility, operational efficiency, and customer satisfaction. By following its guiding principles and aligning quality management practices with international standards, organizations can achieve sustainable growth and maintain a competitive edge in the global market.
However, successful ISO 9000 adoption requires commitment from leadership, engagement from employees, and a structured approach to continuous improvement. By overcoming challenges such as resistance to change, documentation overload, and long-term compliance, businesses can fully leverage ISO 9000’s benefits and position themselves for long-term success.
Whether you’re looking to improve quality control, enhance customer trust, or prepare for ISO 9001 certification, adopting ISO 9000 principles is a proven pathway to excellence in today’s quality-driven business environment.
Need help with ISO 9000 implementation? Learn more about Quality Assurance & Compliance or explore our Third-Party Inspection Services to ensure your business meets global quality standards
Frequently Asked Questions (FAQ) About ISO 9000
1. What is meant by the ISO 9000 standard?
ISO 9000 is a set of internationally recognized quality management principles that provide guidelines for businesses to establish an effective Quality Management System (QMS). It is not a certifiable standard but serves as a foundation for ISO 9001 certification.
2. What is the difference between ISO 9000 and ISO 9001?
ISO 9000 provides theoretical guidelines and principles for quality management.
ISO 9001 is the actual certifiable standard that outlines specific requirements businesses must meet to achieve certification.
3. What are the 7 quality principles as given in ISO 9000?
The seven quality management principles in ISO 9000 are:
1. Customer Focus – Meeting customer needs and exceeding expectations.
2. Leadership – Establishing a clear vision and strong quality culture.
3. Engagement of People – Encouraging employee involvement in quality improvement.
4. Process Approach – Structuring operations for efficiency and effectiveness.
5. Continuous Improvement – Enhancing processes and performance over time.
6.Evidence-Based Decision Making – Using data to drive informed business strategies.
7. Relationship Management – Strengthening relationships with suppliers, stakeholders, and customers.
4. What is ISO 9000 and its objectives?
1. Ensuring consistent product and service quality.
2. Improving customer satisfaction and trust.
3. Standardizing business operations for efficiency.
4. Reducing errors, defects, and inefficiencies.
5. Supporting continuous improvement in quality management.
5. Do I need to get certified for ISO 9000?
No, ISO 9000 itself is not a certifiable standard. Businesses looking for official certification should aim for ISO 9001, which is based on ISO 9000 principles.
6. What industries use ISO 9000?
ISO 9000 is widely adopted across industries such as manufacturing, healthcare, logistics, IT services, retail, and construction. Any business seeking to improve its quality management system (QMS) can benefit from ISO 9000.
7. How long does it take to implement ISO 9000?
The time required varies based on company size and complexity. On average, it takes 6 to 12 months to integrate ISO 9000 principles and prepare for ISO 9001 certification.
8. How does ISO 9000 help improve business operations?
ISO 9000 enhances operations by:
1. Standardizing processes for better efficiency.
2. Reducing defects and operational risks.
3. Ensuring compliance with industry regulations.
4. Strengthening customer relationships through consistent quality.
5. Driving data-driven improvements for long-term success
9. What is the first step in adopting ISO 9000?
The first step is to understand ISO 9000 requirements and conduct a gap analysis to assess your current quality management practices. Then, you can develop a Quality Management System (QMS) aligned with ISO principles.
10. Can small businesses benefit from ISO 9000?
Yes! ISO 9000 is beneficial for businesses of all sizes. Small businesses can use it to improve efficiency, build customer trust, and gain a competitive edge in their industry.
11. How does ISO 9000 support continuous improvement?
ISO 9000 promotes ongoing enhancements by encouraging data-driven decision-making, employee engagement, and systematic process evaluation. Businesses that follow its principles can identify inefficiencies and implement long-term improvements.