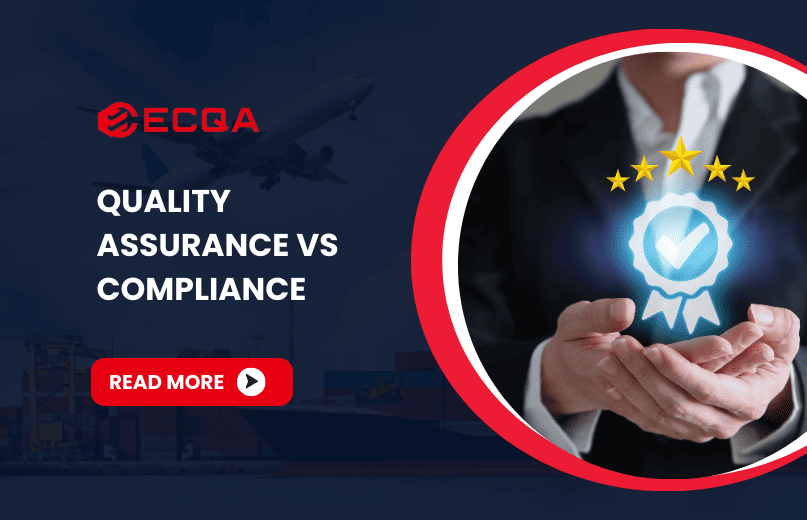
Quality Assurance vs Compliance
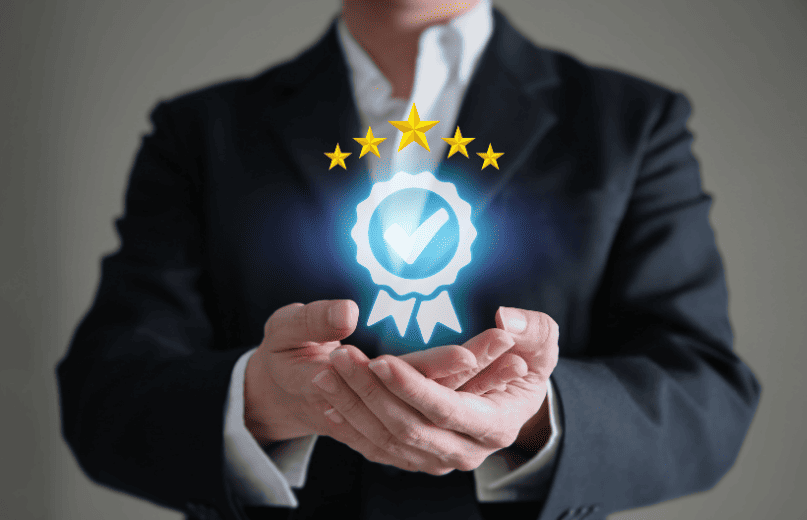
Why Quality Assurance and Compliance Matter
As global trade continues to expand, businesses face an increasingly complex web of regulatory requirements designed to safeguard consumers and ensure fair market practices. Governments and industry bodies worldwide enforce strict quality and safety standards, covering everything from product safety and environmental impact to ethical sourcing and workplace conditions. Failing to comply with these regulations can result in hefty fines, product recalls, legal action, and even loss of market access.
Beyond regulatory obligations, consumer expectations for quality, safety, and ethical production have never been higher. Modern buyers demand flawless, defect-free products and actively support brands that demonstrate transparency and responsibility in their supply chains. A single quality failure can tarnish a company’s reputation, leading to eroding customer trust, negative reviews, and declining sales.
This guide serves as a comprehensive roadmap for businesses seeking to establish robust quality assurance frameworks and maintain full regulatory compliance. By adopting proactive quality control measures, companies can minimize risks, enhance operational efficiency, and strengthen their competitive edge in the global marketplace.
Understanding Quality Assurance and Compliance
What is Quality Assurance (QA)?
Quality assurance (QA) refers to a systematic approach designed to ensure that products, services, and processes meet defined quality standards. It involves proactive measures that prevent defects rather than simply detecting them.
Key components of quality assurance include:
- Standardized operating procedures (SOPs) to maintain process consistency.
- Quality control inspections to detect issues early in production.
- Testing and validation protocols for raw materials and finished products.
- Process audits and continuous improvement initiatives to optimize performance.
- Corrective and preventive action (CAPA) programs to address non-conformities.
A strong quality assurance framework helps businesses minimize defects, enhance product reliability, and ensure compliance with industry regulations.
What is Compliance?
Compliance refers to the adherence to laws, regulations, and industry standards that govern product safety, environmental impact, labor conditions, and manufacturing practices. Regulatory compliance is mandatory and varies by region, industry, and product category. Some of the key compliance areas include:
- Product safety regulations (e.g., CE Marking, FDA, CPSIA).
- Environmental compliance (e.g., RoHS, REACH, WEEE).
- Workplace safety and labor laws (e.g., OSHA, ISO 45001).
- Consumer protection standards (e.g., fair labeling, GDPR, food safety laws).
The Relationship Between Quality Assurance and Compliance
While quality assurance and compliance serve distinct purposes, they are interconnected:
- Quality assurance ensures that a company consistently produces high-quality products, reducing compliance risks.
- Compliance ensures adherence to mandatory legal and regulatory requirements, preventing penalties and legal consequences.
- Companies with strong QA frameworks are better positioned to achieve regulatory compliance with minimal disruptions.
By integrating quality assurance and compliance, businesses can build trust with customers, improve operational efficiency, and avoid costly regulatory failures.
Global Standards and Regulatory Requirements
Ensuring quality and compliance requires businesses to implement and adhere to internationally recognized standards. Various regulatory bodies worldwide set benchmarks for product quality, safety, and sustainability.
Key International Standards for Quality and Compliance
ISO 9001: Quality Management System (QMS)
- The world’s most widely recognized quality management standard.
- Provides a framework for consistent product quality, risk management, and customer satisfaction.
- Applicable to all industries, including manufacturing, healthcare, and services.
ISO 14001: Environmental Management System (EMS)
- Focuses on reducing environmental impact, pollution control, and sustainability.
- Ensures companies comply with environmental laws and implement eco-friendly operations.
ISO 45001: Occupational Health & Safety Management System
- Protects worker safety by minimizing workplace hazards.
- Ensures compliance with labor laws and workplace safety regulations.
Industry-Specific Compliance Regulations
FDA (Food and Drug Administration) – USA
- Regulates food, pharmaceuticals, medical devices, and cosmetics.
- Non-compliance can result in product bans, recalls, and financial penalties.
CE Marking – European Union
- Mandatory for electronics, machinery, and medical devices in the EU market.
- Confirms that products meet EU safety, health, and environmental requirements.
RoHS (Restriction of Hazardous Substances) – Electronics Industry
- Prohibits the use of hazardous materials such as lead, mercury, and cadmium.
- Ensures compliance for selling electronics in the EU and other regulated markets.
REACH (Registration, Evaluation, Authorisation, and Restriction of Chemicals) – EU
- Governs chemical safety, product labeling, and material restrictions.
- Affects manufacturers of plastics, paints, and consumer goods.
Regional Compliance Frameworks
United States (CPSC, FDA, FCC, CPSIA)
- Covers consumer product safety, food, electronics, and pharmaceuticals.
- Requires product testing and certification before market entry.
European Union (CE, REACH, WEEE, GDPR)
- Enforces strict environmental and consumer protection laws.
- Non-compliance results in import bans and financial penalties.
China (CCC – China Compulsory Certification)
- Required for electronics, automotive parts, and industrial equipment.
- Includes mandatory product testing and factory audits.
ASEAN Regulations (ASEAN Harmonized Standards)
- Covers pharmaceuticals, food safety, and electrical appliances.
- Promotes smooth trade within ASEAN member states.
Businesses operating internationally must stay informed about regulatory updates to avoid compliance failures and supply chain disruptions.
The Hidden Costs of Non-Compliance
Many companies underestimate the serious financial and operational risks of non-compliance. Failure to meet quality and regulatory standards can lead to severe consequences, including:
1. Financial Penalties and Legal Action
- Governments impose heavy fines on non-compliant businesses.
- Companies may face lawsuits and compensation claims for defective products.
2. Import Bans and Market Restrictions
- Non-compliant products can be rejected at customs.
- Companies risk losing access to key global markets.
3. Product Recalls and Customer Complaints
- Poor quality leads to expensive recalls.
- Negative customer experiences result in brand damage and lost sales.
4. Reputational Damage and Consumer Distrust
- A single compliance failure can permanently harm brand reputation.
- Loss of customer trust leads to long-term financial losses.
Investing in quality assurance and compliance is essential for risk management, brand protection, and business sustainability.
Key Challenges in Quality Assurance and Compliance
Ensuring quality assurance and compliance presents numerous challenges for businesses across industries. Some of the most common obstacles include:
- Regulatory Complexity: Navigating evolving regulations and standards across different markets requires constant updates and compliance monitoring.
- Cost Implications: Implementing robust quality assurance systems can be costly, requiring investment in training, technology, and audits.
- Supply Chain Management: Maintaining consistent quality across global supply chains poses difficulties due to variations in supplier capabilities and adherence to standards.
- Technological Integration: Leveraging automation and data analytics for quality assurance is essential but requires proper infrastructure and expertise.
- Cultural Differences: Multinational businesses must align quality practices with diverse cultural attitudes toward compliance and process control.
Addressing these challenges proactively ensures a stronger compliance framework and improved operational efficiency.
Third-party inspections play a crucial role in maintaining high-quality standards and ensuring compliance with industry regulations. Key benefits include:
- Objective Evaluation: Independent assessments help identify defects and non-conformities that might be overlooked internally.
- Risk Mitigation: Early detection of quality issues reduces product recalls, warranty claims, and potential liabilities.
- Regulatory Adherence: Third-party inspectors ensure that products and processes comply with local and international regulatory requirements.
- Brand Reputation Protection: Businesses maintaining strict quality assurance standards enhance customer trust and brand credibility.
- Continuous Improvement: Regular inspections provide insights into process optimizations and improvements for long-term success.
Leveraging third-party inspection services strengthens overall quality management and compliance strategies.
Frequently Asked Questions (FAQ)
1. What is the difference between quality assurance and compliance?
Quality assurance focuses on preventing defects and ensuring consistent product or service quality through structured processes. Compliance, on the other hand, ensures adherence to industry regulations, legal requirements, and standards set by governing bodies.
2. Why is quality compliance important for businesses?
Quality compliance helps businesses avoid legal penalties, reduce product recalls, improve customer trust, and maintain brand reputation by meeting regulatory requirements and industry standards.
3. How can third-party inspection improve quality assurance?
Third-party inspection provides independent verification of product quality, identifies defects early, ensures compliance with regulations, and enhances supply chain reliability, reducing risks for businesses.
4. What industries require strict quality compliance?
Industries such as manufacturing, pharmaceuticals, food production, automotive, and consumer electronics require strict quality compliance due to regulatory oversight and safety concerns.
5. How can businesses ensure continuous compliance with regulations?
Businesses can ensure continuous compliance by implementing a robust Quality Management System (QMS), conducting regular audits, training employees, leveraging technology for tracking, and staying updated on regulatory changes.
Ensure Quality and Compliance with ECQA
At ECQA, we specialize in third-party inspections, quality assurance services, and regulatory compliance consulting to help businesses achieve excellence. Our experts ensure your products meet international standards, reducing risks and enhancing your brand reputation.
Get in touch with us today to safeguard your quality standards and compliance requirements.