Supplier Audit
Our supplier audit service provides an in-depth evaluation of manufacturers and suppliers to ensure they meet the required quality, compliance, and operational standards. By conducting comprehensive on-site inspections, we help businesses verify supplier reliability, assess production capabilities, and ensure adherence to international regulations. Our audit process identifies risks, uncovers non-conformities, and provides actionable recommendations to improve supplier performance and supply chain integrity.

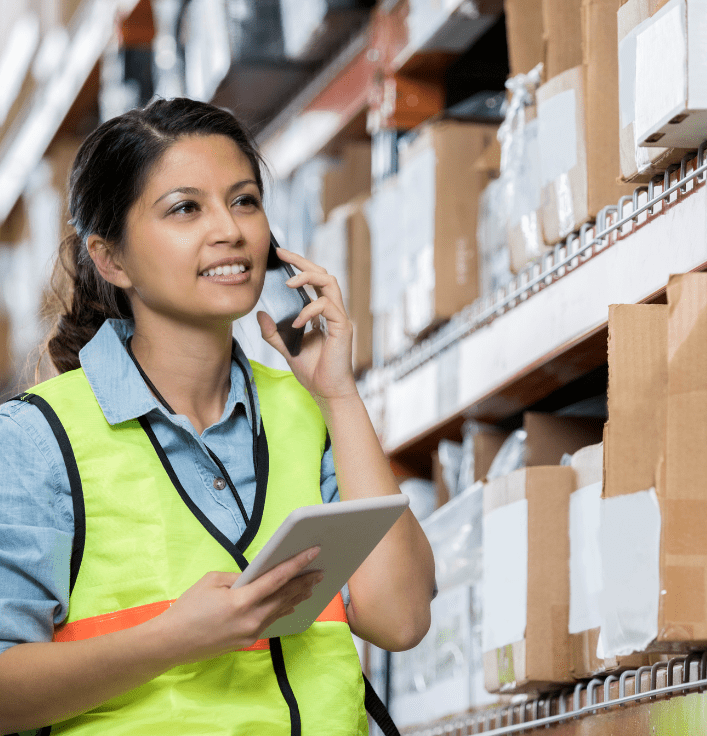
ECQA Supplier Audit Process
Before conducting an audit, we gather essential supplier details and define key evaluation criteria. We work closely with clients to understand their specific requirements, compliance concerns, and industry standards. This phase ensures that the audit is tailored to the client’s needs and effectively addresses potential risks.
2. On-Site Inspection
Our auditors visit the supplier’s manufacturing facility to perform a thorough assessment of their operations. This includes examining production processes, quality management systems, raw material sourcing, and operational efficiency. We also evaluate whether the supplier complies with relevant industry regulations and international standards.
3. Process & Quality Control Review
A key aspect of supplier audits is reviewing the supplier’s quality control measures. We assess how raw materials are inspected, how defects are managed, and whether quality assurance protocols align with required specifications. This step ensures that products consistently meet quality expectations and that suppliers follow standardized testing and inspection procedures.
4. Workplace Compliance Assessment
Ensuring ethical labor practices and workplace safety is crucial for responsible sourcing. Our audits include verifying labor conditions, health and safety policies, worker treatment, and adherence to ethical sourcing requirements. We assess compliance with international labor laws, corporate social responsibility (CSR) guidelines, and environmental policies.
5. Audit Reporting & Corrective Actions
Following the on-site inspection, we provide a detailed audit report that outlines findings, identifies areas of non-compliance, and suggests corrective actions. The report includes insights into the supplier’s strengths and weaknesses, risk factors, and recommendations for improvements. Where necessary, we assist in follow-up audits to monitor corrective actions and ensure continuous improvement.
Types of Supplier Audit
1. Quality System AuditThis audit evaluates whether a supplier’s quality management system complies with ISO 9001 and other applicable standards. It ensures that suppliers have effective procedures in place to maintain consistent product quality.
2. Manufacturing Process Audit
We assess the supplier’s production capacity, equipment maintenance, workflow efficiency, and overall manufacturing capabilities. This type of audit helps businesses determine if a supplier can meet production demands while maintaining high-quality standards.
3. Social Compliance Audit
This audit focuses on workplace conditions, labor rights, ethical business practices, and corporate social responsibility (CSR) compliance. It verifies whether suppliers follow ethical sourcing guidelines, fair labor laws, and industry best practices.
4. Environmental Compliance Audit
We evaluate whether a supplier adheres to environmental regulations, waste management policies, and sustainability practices. This type of audit is crucial for businesses aiming to maintain eco-friendly supply chains and meet global environmental compliance standards.
5. Security & Anti-Terrorism Audit
Our security audit verifies whether a supplier follows global supply chain security regulations, such as the Customs-Trade Partnership Against Terrorism (C-TPAT). This ensures that supply chain operations are protected against security threats, unauthorized access, and smuggling risks.
Key Benefits of Conducting Supplier Audit
A supplier audit ensures that manufacturers adhere to strict quality standards, reducing the risk of defective products, customer complaints, and costly recalls. It helps businesses verify if suppliers meet ISO 9001 and other relevant quality management standards.
2. Compliance with Regulations & Standards
Supplier audits help companies ensure compliance with local and international regulations, such as ISO standards, FDA, CE, RoHS, and REACH. This reduces legal risks and ensures that all supplied products meet the required safety and environmental guidelines.
3. Reduced Supply Chain Risks
By conducting supplier audits, businesses can identify potential risks related to raw materials, production processes, and operational inefficiencies. Early detection of risks helps prevent disruptions and ensures the continuity of the supply chain.
4. Verification of Supplier Capabilities
An audit evaluates the supplier’s manufacturing capacity, production efficiency, and overall operational reliability. This helps businesses confirm whether a supplier can meet order volumes, quality expectations, and delivery deadlines before committing to a contract.
5. Strengthened Supplier Relationships
Regular audits help build long-term, trust-based relationships with suppliers by fostering transparency and accountability. This encourages continuous improvement and ensures suppliers align with the company's business objectives.
6. Ethical & Social Compliance Assurance
A social compliance audit ensures that suppliers follow ethical labor practices, maintain fair wages, and provide a safe working environment. This is crucial for meeting CSR (Corporate Social Responsibility) commitments and avoiding reputational risks.
7. Cost Savings & Operational Efficiency
Identifying process inefficiencies, waste, and potential quality issues during an audit helps suppliers improve their operations. This leads to cost savings, improved productivity, and reduced waste, benefiting both suppliers and buyers.
8. Environmental Responsibility & Sustainability
A supplier audit can assess a company's environmental policies, waste management practices, and sustainability initiatives. This ensures suppliers comply with global environmental standards and align with corporate sustainability goals.
9. Supply Chain Security & Anti-Fraud Protection
Audits help verify suppliers’ adherence to supply chain security protocols, such as C-TPAT and other anti-fraud measures. This prevents counterfeit products, unauthorized subcontracting, and security breaches.
10. Data-Driven Decision Making
Audit reports provide valuable insights into supplier performance, quality trends, and potential risks. Businesses can use this data to make informed decisions about supplier selection, risk management, and strategic sourcing.
How to conduct a supplier audit?
The audit team will examine their processes, quality agreements, and overall adherence to industry standards. We will investigate your suppliers' operations to find any quality issues or areas that can be improved.
- Free consultation
A supplier audit is a crucial step in ensuring product quality, regulatory compliance, and supply chain reliability. Our expert auditors provide comprehensive assessments to help businesses mitigate risks, strengthen supplier relationships, and maintain high industry standards.Contact us today to schedule a supplier audit and gain full confidence in your supply chain.
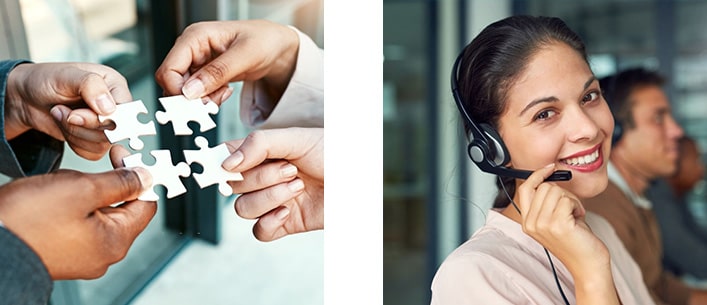
Email us Get a free quote
