Accessories Inspection
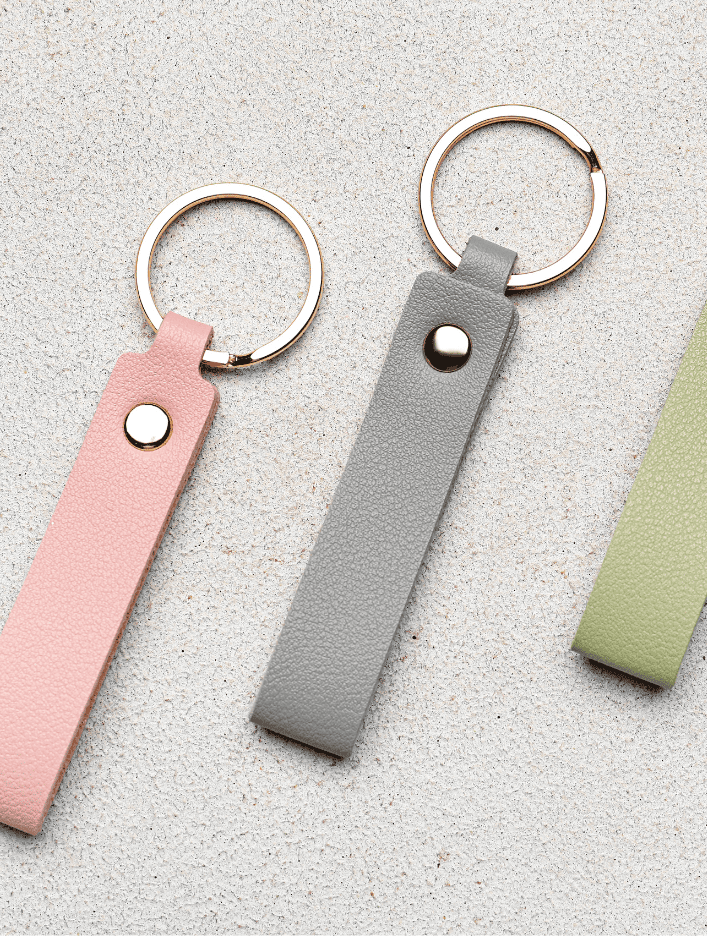
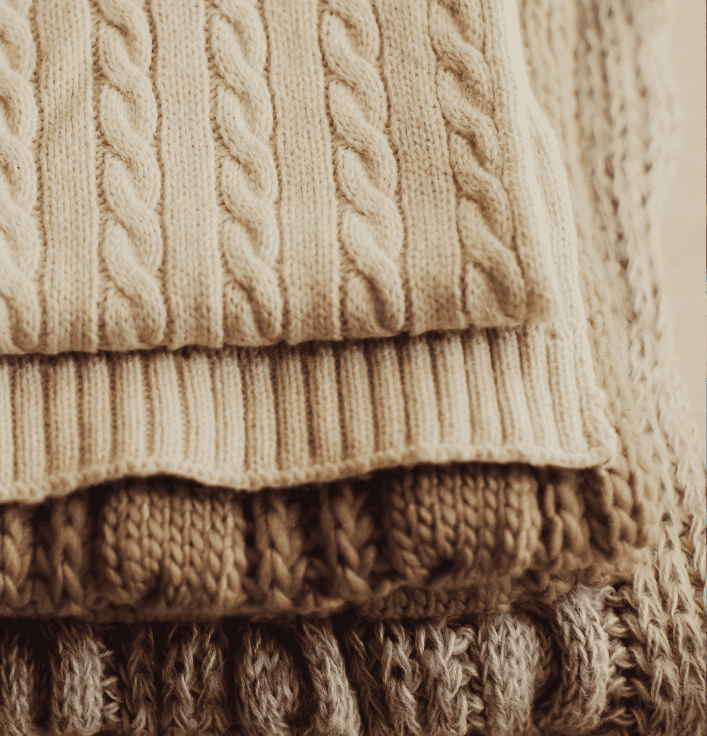
ECQA Accessories Inspection covers the following aspects:
1. Workmanship and Functional Inspection
We conduct thorough checks on the appearance and functionality of each accessory to detect any visible defects, faulty workmanship, or issues with the product’s intended use. This includes examining stitching, assembly quality, material integrity, and surface finishes. Any signs of damage, poor craftsmanship, or functional problems are recorded. Our inspection process adheres to the Acceptance Quality Limit (AQL) standards, categorizing defects as minor, major, or critical, depending on their severity and potential impact. Common workmanship checks include:- Identifying scratches, stains, or discoloration on metal and fabric surfaces.
- Checking for sharp edges or points that could pose safety risks.
- Ensuring that moving parts, such as clasps, buckles, or zippers, function smoothly.
- Verifying the strength and durability of seams, joints, and fasteners.
2. Quantity Verification
We ensure that the quantity of accessories produced matches the order specifications. Our inspectors confirm that the correct number of items is present and that they are packaged in the right quantities as stated in the purchase order. This step is crucial for maintaining supply chain accuracy and meeting contractual obligations.3. Packaging Inspection
Proper packaging plays a key role in protecting accessories during storage and transportation. We review the packaging methods used, including the type of materials, protective layers, and sealing processes. Our accessories inspection ensures that the packaging meets the required standards for quality and durability, protecting products from potential damage. Key aspects of packaging inspection include:- Checking the quality and thickness of polybags, boxes, and other materials used.
- Verifying the presence of warning labels, barcodes, or air holes where necessary.
- Inspecting the dimensions and weight of packaging for consistency.
- Ensuring that all products are correctly labeled, including outer labels and shipping marks.
4. Product Measurement and Testing
Accurate measurements are essential for ensuring that the accessories meet specified requirements. Our inspection team measures the dimensions, weight, and other key parameters of the products to verify compliance with the approved samples and specifications. This step is vital for items where size and fit are critical, such as belts, wristbands, or wearable accessories. We also conduct on-site tests to assess the product’s durability and performance, which may include:- Drop Testing: Assessing the impact resistance of packaging and products.
- Odor Testing: Detecting any unusual smells that may indicate material contamination.
- Load Testing: Verifying the strength of key components, such as straps, hooks, and fasteners.
5. Defect Classification and Reporting
We classify defects found during the inspection into critical, major, or minor categories based on the Acceptance Quality Limit (AQL). Our team provides a detailed report that outlines each issue, including photographs and descriptions, to give you a clear understanding of the product’s condition. This comprehensive report helps you make informed decisions about accepting, rejecting, or requesting rework for the inspected goods.Why Choose ECQA for Accessories Inspection?
At ECQA, we understand the challenges involved in maintaining the quality of accessories, especially when dealing with different suppliers and manufacturers. Our accessories inspection services provide a reliable solution to ensure that your products meet quality standards and customer expectations. Here’s why ECQA stands out:
- Expert Inspectors: Our inspectors have extensive experience in assessing a wide variety of accessories, ensuring a thorough and accurate evaluation.
- Flexible Inspection Solutions: Whether you need pre-production inspection, during production inspection, or final random inspection, we offer customizable services to suit your requirements.
- Global Coverage: With inspection teams based in key manufacturing regions, including China, Malaysia, and Africa, we can perform on-site inspections wherever your suppliers are located.
- Quick Turnaround Time: We understand the time-sensitive nature of the supply chain and offer prompt reporting to help you make timely decisions.
- Transparent Reporting: Our detailed inspection reports provide clear and actionable insights, enabling you to address any quality issues proactively.
ECQA Accessories Inspection Services Coverage is as follows:
- Scarf
- Hat
- Socks
- Gloves Tie
- Bowtie Belt
- Headband
- Handkerchief
- Kneepads
- Wristbands, etc.
- Free consultation
Protect your brand reputation and ensure your accessories are of the highest quality with ECQA's expert inspection services. Whether you’re dealing with keyrings, fashion accessories, or other small products, we’ve got you covered. Contact us today to schedule your accessories inspection or learn more about our comprehensive range of quality control services. Let us help you deliver exceptional products that exceed your customers’ expectations.
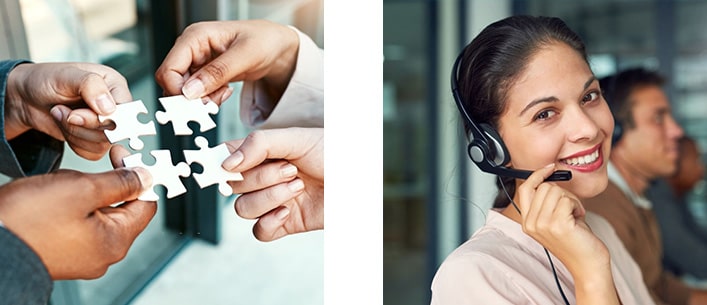
Email us Get a free quote
